Developing adhesive formulas can be incredibly challenging. The primary issue lies in the need for targeted formulations. Many suitable raw materials must be combined to achieve the desired properties, requiring continuous trial and error to resolve inherent contradictions. Especially when facing a bottleneck, introducing one more option could lead to a significant breakthrough.
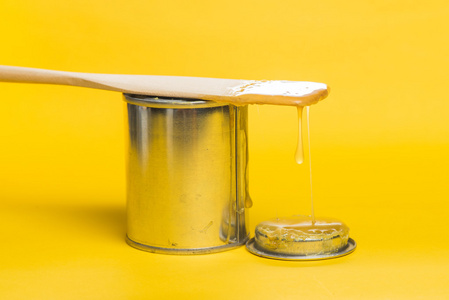
Key Difficulties in Adhesive Formula Development
The challenges in creating adhesive formulas can be better understood through practical examples. Tang Long et al. explored a novel formula development method specifically for polyol components in two-component polyurethane adhesives. Their approach aimed to balance the performance trade-off between low hardness and high bonding strength.
Optimizing Raw Materials
The authors began by employing orthogonal experimental design to optimize the types of raw materials used. This step was crucial for identifying the most suitable components for the adhesive formulation.
Fine-tuning Ratios
Following this, they utilized JMP customized experimental design to optimize the ratios of the selected raw materials. This method effectively sidesteps the common challenge of addressing both material types and ratios simultaneously in conventional formula development.
The results of their study demonstrate that this innovative method successfully addressed the conflicting requirements of low hardness and high bonding strength in adhesives. They achieved a polyurethane adhesive characterized by:
- Colloid Hardness: 40D
- Tensile Shear Strength: 11.34 MPa (aluminum sheet-to-aluminum sheet)
- Bonding Strength: 283.5 kPa/D per unit hardness
Is the Development Experiment Complete? Not quite. The authors noted that several “problems” remain, highlighting the ongoing difficulties in adhesive formulation development. These challenges are often where significant innovations can arise.
The importance of evaluating the following incorrect assumptions
Interaction Between Major Categories: The optimization process did not account for the interactions among different categories of raw materials, which can significantly affect the test responses.
Physical Properties of Raw Materials: Factors such as purity, moisture content, and uniformity of the raw materials were overlooked in the analysis, potentially skewing results.
Independence of Raw Material Effects: The assumption that the type and proportion of raw materials affect the test responses independently is flawed, as these factors often influence one another.
Given these uncertainties in formulation, it is crucial to find ways to mitigate their impact. One effective strategy is to utilize relatively controllable factors to offset these uncertainties.
Leveraging Fillers in Adhesives
(1) Selecting Mainstream Fillers
Choosing widely used fillers—such as calcium carbonate and silica—can enhance adhesive performance. Mineral fillers not only provide a cost-effective solution but also offer a diverse range of functions. They have been a staple in adhesive formulation for years, allowing for fine-tuning of properties. Tang Long et al. highlighted that in their study, the range of the matrix resin and the chain extender/cross-linking agent had the largest effect on test outcomes. The rheological additive had a secondary influence, while fillers had a significant impact, positioned between primary and secondary effects.
When selecting fillers, there is considerable flexibility, and traditional fillers are often the best choice. Their long-standing use in production lends them higher cost-effectiveness and stability. For example, calcium carbonate—known for its fineness, uniformity, and high whiteness—has been widely utilized as a filler in adhesives.
Cui Lidong et al. conducted research using 850 mesh calcium carbonate as a filler in emulsion adhesives for wood. They studied the effects of varying addition ratios on adhesive performance through a single-factor experimental method. The results indicated that:
- Viscosity and Hardness: Increased with higher calcium carbonate ratios.
- Bonding Strength: Initially increased, then decreased at higher ratios.
- Stability: Deteriorated with increased filler content.
The Impact of Fillers on Adhesive Performance
Relationship Between Calcium Carbonate Addition Ratio and Shore A Hardness
Zhou Xiao et al. investigated the influence of quartz powder as a filler in single-component polyurethane adhesives. Their findings indicated that quartz powder exhibits good compatibility with polyurethane systems, significantly enhancing properties such as tensile strength, elongation at break, and tear strength of the resulting adhesive products.
(2) Exploring Advanced Fillers: Silicon Carbide and Alumina
Li Zhaoyuan et al. utilized cubic nano-silicon carbide (β-SiC) as a filler to develop modified inorganic adhesives. Their experiments revealed that with a filler content of 40%, the adhesive achieved remarkable performance metrics:
- Tensile Shear Strength: 13.5 MPa
- Fatigue Life Iteration Number: 67 cycles
- Peel Strength: 46.7 N/mm²
These results highlight that nanoparticle modification can significantly enhance the bonding performance of inorganic adhesives, providing superior reliability across various applications.
Chen Zeming et al. explored the effects of various inorganic fillers—including silica powder, Al₂O₃, mullite, boron nitride, talcum powder, and mica—on modified epoxy resin adhesives. Their study assessed how different types and dosages of fillers influenced bonding strength and the bonding interface. Key findings included:
Bonding Strength Trends: The bonding strength initially increased with the filler dosage, then decreased at higher levels.
Optimal Filler Performance: Among the fillers tested, 15 parts of Al₂O₃ yielded the best results, achieving shear strength and peel strength values of 22.42 MPa and 12.84 N/cm, respectively.
The addition of Al₂O₃ filler facilitates the formation of chemical bonds, such as C-Al and Al-O-C, which reduce the cohesive force of the modified epoxy resin. This enhancement increases the bonding force at the adhesive-aluminum alloy interface, thus improving both peel and shear strength.
(3) Systematic Study of Fillers in Adhesives
Two-component acrylic structural adhesives are widely used for bonding metal and non-metal materials in various industries, including aerospace, automotive, construction, and electronics. Although fillers are insoluble in adhesive systems due to their inherent properties, modifications can enhance the interaction between fillers and adhesives. This interaction improves the mechanical properties of the adhesives, increases viscosity, and promotes stronger adhesion to substrates.
Regulation of Mechanical Properties
Mechanical properties are critical for the performance of acrylic structural adhesives across different applications. Researchers have proposed several strategies to enhance these properties, including the incorporation of thermoplastic compounds and inorganic fillers.
Regulation of Thermal Conductivity
Incorporating appropriate inorganic fillers with electrical insulation properties can significantly enhance the thermal conductivity of acrylic adhesive systems. Suitable fillers include:
- Aluminum Hydroxide
- Magnesium Hydroxide
- Aluminum Oxide
- Magnesium Oxide
- Zinc Oxide
- Silicon Dioxide
- Titanium Dioxide
- Calcium Silicate
- Aluminum Silicate
- Calcium Carbonate
- Silicon Nitride
- Silicon Carbide
- Aluminum Borate
Additionally, whiskers made of silicon carbide, aluminum oxide, or aluminum borate can improve the adhesive’s thermal conductivity and flame retardancy while maintaining its mechanical and curing properties.
Regulation of Moisture and Heat Resistance
Liu Chengliang et al. introduced a method for preparing highly weather-resistant acrylic structural adhesives in their patent. By adding 0 to 30 parts of inorganic fillers, such as fumed silica, calcium carbonate, and nano-alumina, to components A and B, the adhesive demonstrated impressive performance:
- Tensile Shear Strength at Room Temperature: 9.36 MPa (stainless steel/PMMA) and 10.35 MPa (magnesium/PMMA).
- Tensile Shear Strength After Aging: Retained values of 9.83 MPa and 9.64 MPa after 2 weeks at 85°C and 85% humidity, with retention rates of 105% and 93%, respectively.
Regulation of Corrosion Resistance
Using acrylic structural adhesives can reduce or eliminate the need for costly finishing operations like riveting and welding, resulting in a more aesthetically pleasing appearance with fewer corrosion-prone holes or stress points. Different metals can be bonded with a lower risk of galvanic corrosion. Enhancing corrosion resistance can be achieved by adding mixtures of metal molybdates (e.g., zinc molybdate, calcium molybdate, barium molybdate, or strontium molybdate) and inert fillers such as zinc phosphate, calcium phosphate, and magnesium phosphate.
Regulation of Other Properties
In addition to enhancing mechanical and thermal properties, some inorganic fillers serve critical roles as thixotropic agents, thickeners, and reinforcing agents. They can effectively alter various characteristics of two-component acrylic structural adhesive systems, including density, viscosity, and thixotropy. Liu Suyu et al. developed a method for creating an acrylic adhesive specifically designed for bonding automotive skirtings. In this formulation, calcium carbonate was used as the primary filler. The inclusion of calcium carbonate led to several beneficial outcomes:
- Reduced Thixotropy: The adhesive became easier to apply and scrape.
- Lower Exothermic Temperature: The exothermic temperature was reduced from 115°C to below 85°C, promoting more stable curing.
- Minimized Curing Shrinkage: The curing shrinkage was kept below 1%, effectively shortening construction time.
Conclusion
When faced with challenges in adhesive formulation, consider leveraging inorganic fillers. Their versatility can provide effective solutions to various problems.