From a professional perspective on powder particle modification processes, the core differences between wet and dry methods can be analyzed across six key dimensions:
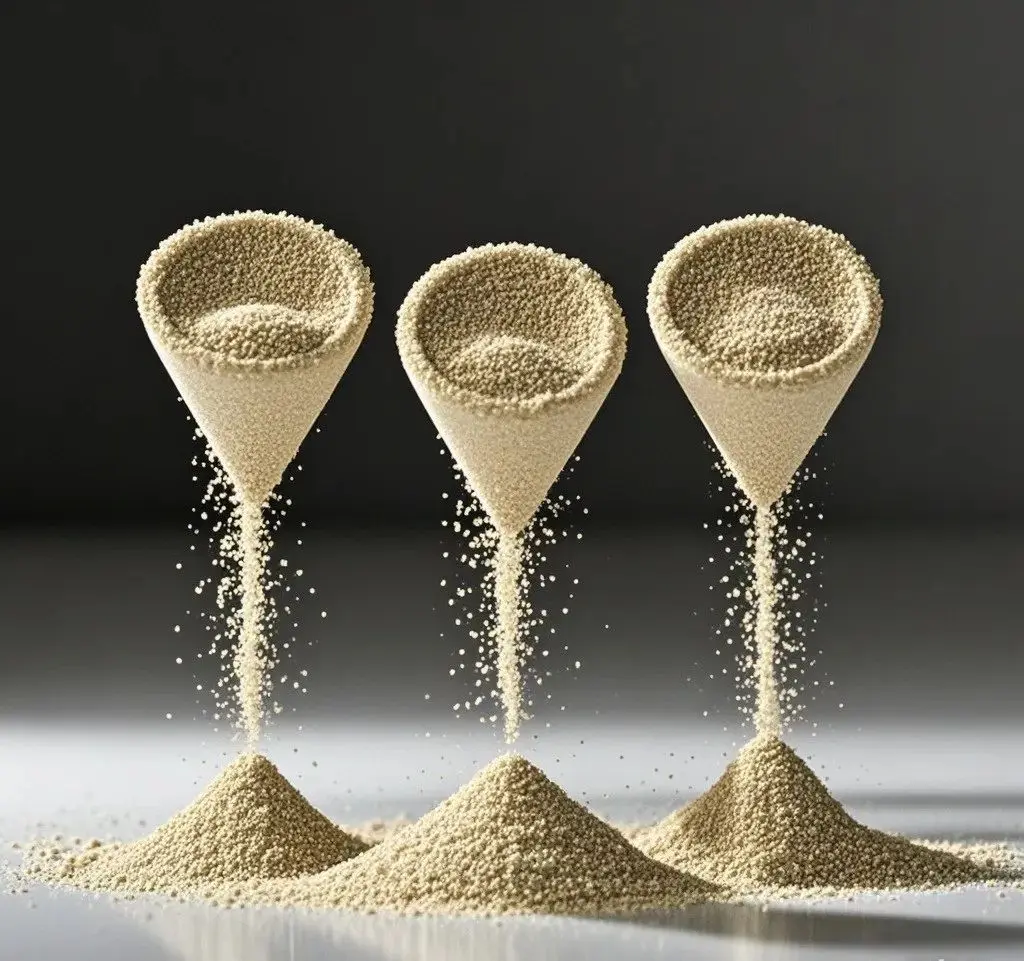
Process Adaptability
Wet Method: Suitable for ultrafine powders with particle sizes
≤5μm (e.g., nano calcium carbonate). The liquid environment prevents hard agglomeration during drying. For example, in the production of pearlescent mica pigments requiring TiO₂ coating, the wet method ensures coating uniformity within± 5nm.
Dry Method: Suitable for micron-sized powders with D50 ≥10μm (e.g., conventional ground calcium carbonate). High-speed mixers (300-1500 rpm) enable rapid modification, with a single unit processing capacity of up to 5t/h.
Modifier Dispersion Mechanism
Wet Method: Utilizes solvents (e.g., water, ethanol) to form a diffusion double layer. Stable suspension is achieved when the Zeta potential is controlled at ±30mV. For instance, silane coupling agents undergo hydrolysis and then condense with hydroxyl groups on SiO₂ surfaces, increasing bonding efficiency to over 90%.
Dry Method: Relies on mechanical energy (shear force >10⁴ s⁻¹) to break modifier agglomerates. However, actual coating rates typically do not exceed 75%, requiring the addition of 0.5-1% dispersing aids (e.g., stearic acid).
Equipment and Energy Consumption
Wet Method: Requires jacketed reaction kettles (heat transfer coefficient: 200-500 W/m²·K). After modification, materials undergo centrifugal dewatering (energy consumption: 0.8 kWh/kg) and spray drying (inlet air temperature: 180-220℃).
Dry Method: Uses SLG-type continuous modification machines, with specific energy consumption around 0.15 kWh/kg. Equipment investment is reduced by 40%, but dust concentration must be controlled below 10 mg/m³.
Key Quality Indicators
Wet Method: Activation index ≥98%, with oil absorption value reduced by 30% (e.g., modified kaolin decreases from 80g/100g to 55g/100g).
Dry Method: Coating thickness deviation ±15nm, volume resistivity adjustable within 10¹²-10¹⁵ Ω·cm (e.g., modified aluminum hydroxide for cable applications).
Application Scenarios
Wet Method:
High-end engineering plastics (e.g., PA6 + 30% glass fiber) require modified fillers with D99 ≤3μm.
Al₂O₃ coating for lithium battery cathode materials (e.g., NCM811).
Dry Method:
Modified heavy calcium carbonate (1250 mesh) for PVC pipes, with cost control at 800 RMB/ton.
Calcined kaolin for architectural coatings, maintaining a whiteness level above 92%.
Process Economics
Wet Method: Overall cost is 25-40% higher than the dry method, with solvent recovery accounting for 18% of costs. However, product premium can reach 30-50% (e.g., pearlescent pigments selling for 80,000-150,000 RMB/ton).
Dry Method: Per-ton energy consumption is reduced by 60%, making it suitable for large-scale powder modification (annual production >50,000 tons), with an investment payback period shortened to 2-3 years.
Current technological advancements indicate that the wet method is evolving toward continuous micro-reactor processing (residence time <5 minutes), while the dry method is making breakthroughs in integrated vortex mill modification equipment (increasing specific surface area by 20%). When selecting a modification process, companies must comprehensively evaluate product positioning (high-end vs. bulk production), capital investment intensity (CAPEX difference of 2-3 times), and environmental regulations (VOCs emission limits: 30 mg/m³).
Conclusion
Epic Powder Machinery specializes in advanced powder particle modification solutions, offering both wet and dry processing technologies to meet diverse industrial needs. With European core expertise and decades of experience, we provide high-efficiency modification equipment that ensures optimal particle coating, energy efficiency, and cost-effectiveness. Whether for high-end materials like lithium battery cathodes or large-scale bulk powder processing, Epic Powder Machinery delivers tailored solutions to enhance product performance and meet evolving market demands.