Desde una perspectiva profesional sobre los procesos de modificación de partículas de polvo, las diferencias fundamentales entre los métodos húmedos y secos se pueden analizar en seis dimensiones clave:
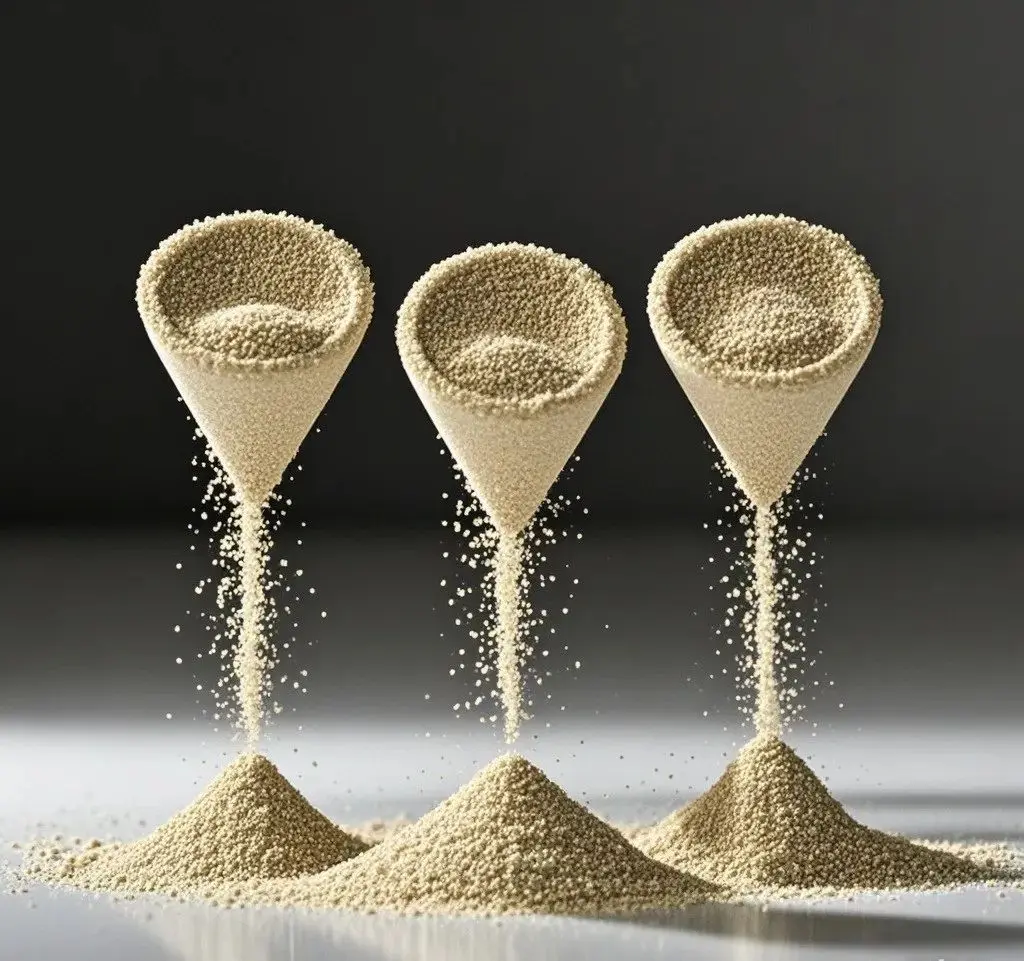
Adaptabilidad del proceso
Método húmedo: Adecuado para polvos ultrafinos con tamaños de partículas
≤5 μm (p. ej., nanocarbonato de calcio). El entorno líquido evita la aglomeración dura durante el secado. Por ejemplo, en la producción de pigmentos de mica perlada que requieren un recubrimiento de TiO₂, el método húmedo garantiza una uniformidad del recubrimiento dentro de ±5 nm.
Método seco: Adecuado para polvos micrométricos con D50 ≥10 μm (p. ej., carbonato de calcio molido convencional). Los mezcladores de alta velocidad (300-1500 rpm) permiten una modificación rápida, con una capacidad de procesamiento de hasta 5 t/h en una sola unidad.
Mecanismo de dispersión de modificadores
Método húmedo: Utiliza disolventes (p. ej., agua, etanol) para formar una doble capa de difusión. Se logra una suspensión estable cuando el potencial zeta se controla a ±30 mV. Por ejemplo, los agentes de acoplamiento de silano se hidrólisis y luego se condensan con grupos hidroxilo en superficies de SiO₂, lo que aumenta la eficiencia de unión a más de 90%.
Método seco: Se basa en energía mecánica (fuerza de corte >10⁴ s⁻¹) para romper los aglomerados del modificador. Sin embargo, las tasas de recubrimiento reales no suelen superar los 751 TP⁻T, lo que requiere la adición de 0,5-11 TP⁻T de dispersantes (p. ej., ácido esteárico).
Equipos y consumo de energía
Método húmedo: Requiere calderas de reacción con camisa (coeficiente de transferencia de calor: 200-500 W/m²·K). Tras la modificación, los materiales se someten a deshidratación centrífuga (consumo de energía: 0,8 kWh/kg) y secado por aspersión (temperatura del aire de entrada: 180-220 °C).
Método seco: Utiliza máquinas de modificación continua tipo SLG, con un consumo energético específico de aproximadamente 0,15 kWh/kg. La inversión en equipos se reduce en 40%, pero la concentración de polvo debe controlarse por debajo de 10 mg/m³.
Indicadores clave de calidad
Método húmedo: Índice de activación ≥98%, con valor de absorción de aceite reducido en 30% (por ejemplo, el caolín modificado disminuye de 80 g/100 g a 55 g/100 g).
Método seco: desviación del espesor del revestimiento ±15 nm, resistividad de volumen ajustable entre 10¹² y 10¹⁵ Ω·cm (por ejemplo, hidróxido de aluminio modificado para aplicaciones de cable).
Escenarios de aplicación
Método húmedo:
Los plásticos de ingeniería de alta gama (por ejemplo, PA6 + fibra de vidrio 30%) requieren rellenos modificados con D99 ≤3 μm.
Recubrimiento de Al₂O₃ para materiales de cátodo de baterías de litio (por ejemplo, NCM811).
Método seco:
Carbonato de calcio pesado modificado (malla 1250) para tuberías de PVC, con control de costos a 800 RMB/tonelada.
Caolín calcinado para recubrimientos arquitectónicos, manteniendo un nivel de blancura superior a 92%.
Economía de procesos
Método húmedo: El costo total es entre 25 y 401 TP³T mayor que el del método seco, y la recuperación del solvente representa 181 TP³T. Sin embargo, el sobreprecio del producto puede alcanzar entre 30 y 501 TP³T (por ejemplo, los pigmentos perlados se venden a 80 000-150 000 RMB/tonelada).
Método seco: el consumo de energía por tonelada se reduce en 60%, lo que lo hace adecuado para la modificación de polvo a gran escala (producción anual >50.000 toneladas), con un período de recuperación de la inversión acortado a 2-3 años.
Los avances tecnológicos actuales indican que el método húmedo está evolucionando hacia el procesamiento continuo en microrreactores (tiempo de residencia <5 minutos), mientras que el método seco está logrando avances en equipos integrados de modificación de molinos de vórtice (incrementando la superficie específica en 20%). Al seleccionar un proceso de modificación, las empresas deben evaluar exhaustivamente el posicionamiento del producto (producción de alta gama vs. producción a gran escala), la intensidad de la inversión de capital (diferencia de CAPEX de 2 a 3 veces) y la normativa ambiental (límites de emisión de COV: 30 mg/m³).
Conclusión
Polvo épico Machinery se especializa en soluciones avanzadas de modificación de partículas de polvo, ofreciendo tecnologías de procesamiento tanto en húmedo como en seco para satisfacer diversas necesidades industriales. Con una sólida experiencia europea y décadas de experiencia, proporcionamos equipos de modificación de alta eficiencia que garantizan un recubrimiento óptimo de partículas, eficiencia energética y rentabilidad. Ya sea para materiales de alta gama como cátodos de baterías de litio o para el procesamiento de polvo a gran escala, Polvo épico La maquinaria ofrece soluciones personalizadas para mejorar el rendimiento del producto y satisfacer las cambiantes demandas del mercado.