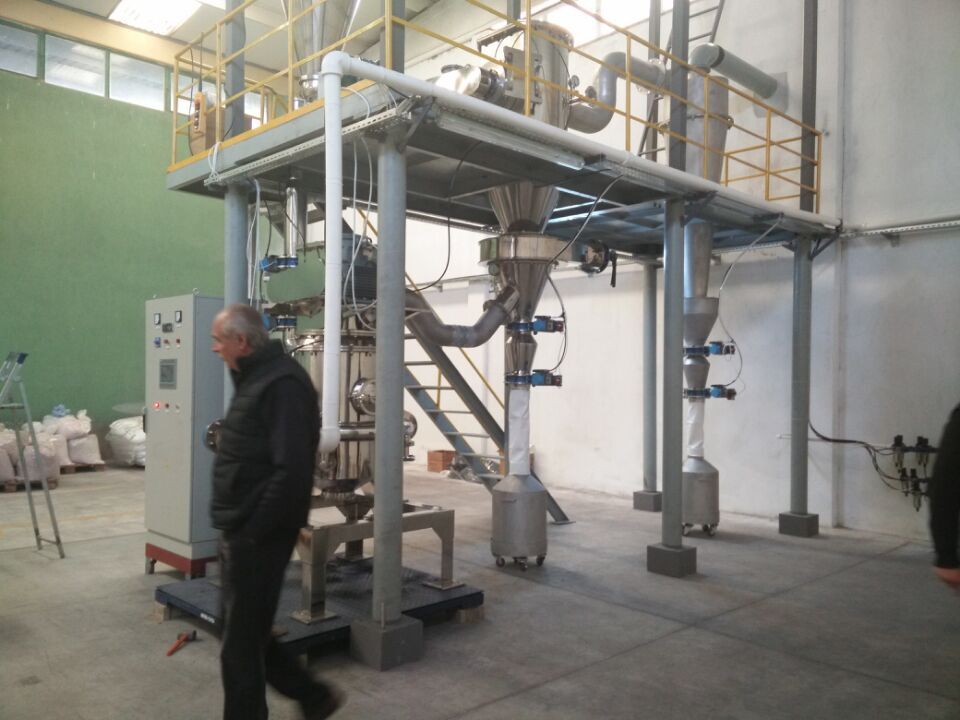
Un micronizador de molino de chorro es un dispositivo de alta precisión diseñado para reducir partículas a tamaños extremadamente finos. Chorros de aire comprimido o gas de alta velocidad para crear un vórtice dentro de una cámara cilíndrica o cónica. Este vórtice hace que las partículas colisionen a altas velocidades, rompiéndolas en fragmentos más pequeños. A diferencia de los métodos de molienda tradicionales, este proceso genera un calor mínimo, lo que lo hace ideal para materiales sensibles al calor. Industrias como la farmacéutica, la alimentaria y la química confían en esta tecnología para lograr tamaños de partículas consistentes. El control preciso garantiza un mejor rendimiento del producto, ya sea mejorando la biodisponibilidad de los medicamentos o mejorando la textura de los productos alimenticios.
Puntos clave
- Los micronizadores de chorro utilizan chorros de gas rápidos para fabricar partículas diminutas.
- No tienen partes móviles, por lo que se mantienen muy limpios.
- Esto los hace ideales para la industria farmacéutica y alimentaria.
- Cambiar la presión y el flujo del gas controla cómo llegan las partículas pequeñas.
- Una presión más alta produce partículas aún más pequeñas.
- Los molinos de chorro ahorran energía y funcionan bien en muchas industrias.
- Se utilizan para fabricar medicamentos, alimentos y productos electrónicos.
- Estas máquinas crean tamaños de partículas uniformes, mejorando la calidad del producto.
¿Cómo funciona un micronizador Jet Mill?
El papel del gas a alta velocidad
Cómo el gas acelera las partículas a velocidades cercanas a las supersónicas
En un micronizador de molino de chorro, el aire comprimido, el gas o el vapor impulsan las partículas a velocidades extremadamente altas. Este proceso se basa en el principio de la dinámica de fluidos, donde los chorros de gas crean un vórtice dentro de la cámara de molienda. A medida que el gas fluye a través de las boquillas, acelera las partículas a velocidades casi supersónicas. La ausencia de piezas móviles garantiza que las partículas permanezcan sin contaminar durante el proceso. Esto hace que el micronizador de molino de chorro sea ideal para aplicaciones que requieren pureza, como productos farmacéuticos o químicos finos.
La importancia de la presión y el caudal del gas en el proceso de molienda
La presión del gas y el caudal desempeñan un papel fundamental a la hora de determinar el rendimiento de un micronizador de molino de chorro. Las presiones de gas más altas, como 7-15 bar para vapor o 3,5-8,5 bar para aire, generan una mayor energía cinética. Esto da como resultado tamaños de partículas más finos. Por el contrario, las presiones más bajas producen partículas más gruesas. El ajuste del caudal también afecta a la eficiencia de molienda. Las velocidades de alimentación más rápidas reducen el tiempo que las partículas pasan en la cámara, lo que da lugar a tamaños de partículas más grandes. Para obtener los mejores resultados, debe equilibrar la presión del gas, el caudal y la velocidad de alimentación.
Choques de partículas y reducción de tamaño
El mecanismo de colisiones entre partículas para la micronización
Dentro de la cámara de molienda, las partículas chocan entre sí debido a la flujo de gas a alta velocidadEstas colisiones se producen debido a los fuertes gradientes de velocidad creados por el vórtice. Las fuerzas de impacto, compresión y cizallamiento generadas durante estas colisiones rompen las partículas en fragmentos más pequeños. Este método elimina la necesidad de medios de molienda, lo que reduce los riesgos de contaminación.
Cómo las colisiones logran tamaños de partículas micrométricas o submicrónicas sin medios de molienda
El micronizador de chorro de aire logra tamaños de partículas ultrafinos basándose únicamente en colisiones entre partículas. A medida que las partículas chocan repetidamente, su tamaño se reduce al rango de micrones o submicrones. La ausencia de medios de molienda garantiza que el proceso se mantenga limpio y sea adecuado para materiales sensibles. Esta característica es particularmente beneficiosa para industrias como la alimentaria y la electrónica, donde la pureza y la precisión son esenciales.
Separación y recolección de partículas
El papel de las fuerzas centrífugas en la separación de partículas finas
Una vez que las partículas alcanzan el tamaño deseado, entran en juego las fuerzas centrífugas. El vórtice dentro de la cámara crea una zona de clasificación donde las partículas finas se separan de las más grandes. La fuerza centrífuga empuja las partículas más gruesas hacia afuera, permitiendo que solo las partículas más finas se desplacen hacia el sistema de recolección.
Cómo se recogen eficientemente las partículas finas después de la reducción de tamaño
Una vez separadas, las partículas finas salen de la cámara a través de un clasificador o salida. El sistema de recolección garantiza que las partículas se recopilen de manera eficiente sin perder material. Este proceso de separación preciso permite que el micronizador de molino de chorro produzca polvos con tamaños de partículas uniformes, cumpliendo con los estrictos requisitos de varias industrias.
Tipos de molinos de chorro
Molinos de chorro de lecho fluidizado
Diseño y mecanismo de funcionamiento de molinos de chorro de lecho fluidizado
Los molinos de chorro de lecho fluidizado funcionan con un diseño exclusivo que incorpora un clasificador de aire activo. A diferencia de otros molinos de chorro, este clasificador utiliza una rueda giratoria con velocidad ajustable para controlar el tamaño final de las partículas. El material de alimentación ingresa a la cámara de molienda a través de una válvula rotatoria o un alimentador de tornillo. Las corrientes de gas de alta velocidad de boquillas opuestas arrastran el material, lo que provoca colisiones de partículas que reducen el tamaño. La fuerza centrífuga separa las partículas finas de las más gruesas. Las partículas finas salen a través de un separador ciclónico y un colector de polvo, mientras que las partículas más grandes regresan para seguir moliendo.
Características clave, como fresado eficiente e idoneidad para materiales sensibles al calor.
Este tipo de molino de chorro ofrece varias ventajas:
- Maneja materiales con una dureza Mohs de hasta 10, lo que lo hace versátil.
- Procesa materiales sensibles al calor de manera eficiente debido a la mínima generación de calor.
- Reduce el consumo energético y funciona con bajos niveles de ruido.
- Procesa de forma segura materiales inflamables o explosivos, como polvo de aluminio, minimizando la fricción mecánica.
Molinos de chorro circular
Diseño y mecanismo de funcionamiento de molinos de chorro circular
Los molinos de chorro circulares cuentan con un diseño de cámara simple que mejora el rendimiento. La cámara minimiza el efecto de la fuerza centrífuga sobre las partículas pequeñas, lo que les permite moverse de manera eficiente hacia la salida central. Este diseño mejora el proceso de reducción del tamaño de las partículas al garantizar colisiones consistentes y una clasificación precisa.
Características principales, incluido un diseño compacto y un control preciso del tamaño de partículas
Los molinos de chorro circulares son compactos y de fácil mantenimiento. Su diseño simple permite una limpieza rápida, lo que reduce el riesgo de contaminación cruzada. Logran tamaños de partículas muy finos con distribuciones ajustadas, lo que los hace ideales para aplicaciones que requieren precisión. La ausencia de piezas móviles en la cámara de molienda mejora la confiabilidad y elimina los riesgos de contaminación por fallas mecánicas.
Aplicaciones y beneficios de los molinos de chorro espiral
Los molinos de chorro espiral se utilizan ampliamente en todas las industrias debido a su versatilidad y eficiencia.
Solicitud/Beneficio | Descripción |
---|---|
Industria farmacéutica | Microniza los ingredientes farmacéuticos activos (API) para mejorar la biodisponibilidad. |
Industria alimentaria | Reduce el tamaño de los ingredientes alimentarios para mejorar la textura, el sabor y la vida útil. |
Industria química | Produce productos químicos finos y pigmentos con una distribución precisa del tamaño de partículas. |
Industria cosmética | Microniza los ingredientes cosméticos para una mejor textura y aplicación. |
Industria aeroespacial | Produce materiales de alto rendimiento con tolerancias estrictas. |
Industria electrónica | Crea polvos finos para componentes electrónicos para mejorar la conductividad y la confiabilidad. |
Alta eficiencia | Ofrece una reducción superior del tamaño de partículas con un desperdicio mínimo. |
Baja contaminación | Asegura la pureza evitando medios de molienda. |
Eficiencia energética | Consume menos energía en comparación con otras técnicas de fresado. |
Fácil de limpiar | Simplifica la limpieza y el mantenimiento, reduciendo el tiempo de inactividad. |
Versatilidad | Maneja una amplia gama de materiales, incluidas sustancias duras y abrasivas. |
Escalabilidad | Se adapta fácilmente a operaciones tanto de pequeña como de gran escala. |
Los molinos de chorro espiral son particularmente beneficiosos para las industrias que requieren tamaños de partículas uniformes y una contaminación mínima.
Ventajas y desventajas de los micronizadores Jet Mill
Ventajas
Conseguir tamaños de partículas ultrafinas con alta precisión
Los micronizadores de molino de chorro se destacan por producir polvos ultrafinos con tamaños de partículas que van desde 1 a 10 micrones. Esta precisión es esencial para industrias como la farmacéutica, donde el tamaño uniforme de las partículas mejora el rendimiento del fármaco. La tecnología también le permite clasificar partículas dentro de un rango de tamaño estrecho durante el proceso de molienda. Esta doble funcionalidad garantiza resultados consistentes adaptados a sus necesidades específicas.
Baja contaminación debido a la ausencia de partes móviles
A diferencia de los métodos de molienda tradicionales, los micronizadores de molino de chorro no tienen partes móviles dentro de la cámara de molienda. Este diseño elimina el desgaste mecánico y reduce el riesgo de contaminación. Puede confiar en esta característica para mantener la pureza de sus materiales, lo que es especialmente importante en aplicaciones como el procesamiento de alimentos y la fabricación de productos electrónicos.
Proceso no térmico adecuado para materiales sensibles al calor.
Los micronizadores de molino de chorro funcionan sin generar calor significativo. El flujo de gas a alta velocidad impulsa el proceso de molienda, manteniendo las temperaturas bajas. Esto hace que la tecnología sea ideal para procesar materiales sensibles al calor, como ingredientes farmacéuticos activos o ciertos polímeros. Puede lograr tamaños de partículas finas sin comprometer la integridad de sus materiales.
Desventajas
Alto consumo de energía en comparación con otros métodos de molienda.
Los micronizadores de molino de chorro requieren gas comprimido, que consume una cantidad significativa de energía. El proceso de compresión de aire o vapor a altas presiones exige equipos y recursos avanzados. Esto hace que la tecnología sea más adecuada para productos de alto valor donde la precisión y la pureza superan los costos de energía.
Costos operativos más elevados debido a la necesidad de gas comprimido
La dependencia del gas comprimido no solo aumenta el consumo de energía, sino que también eleva los gastos operativos. Es posible que el mantenimiento del suministro y la presión de gas necesarios aumente el costo general de uso de un micronizador de molino de chorro. Este factor puede limitar su viabilidad para productos de bajo margen.
Limitado a tipos de materiales específicos y rangos de tamaño de partículas
Los micronizadores de molino de chorro funcionan mejor con materiales que pueden soportar colisiones a alta velocidad sin degradarse. Son menos eficaces para sustancias pegajosas o muy elásticas. Además, si bien se destacan en la producción de partículas ultrafinas, es posible que no sean la mejor opción para requisitos de tamaño más grueso. Debe evaluar las propiedades de su material y los resultados deseados antes de seleccionar esta tecnología.
Aplicaciones industriales de los micronizadores de chorro
Productos farmacéuticos
Producción de polvos finos para formulaciones de medicamentos.
Puede confiar en los micronizadores de molino de chorro para producir polvos finos esenciales para aplicaciones farmacéuticas. Estos dispositivos se destacan en la molienda de ingredientes farmacéuticos activos (API) a tamaños precisos, generalmente en el rango de 1 a 5 micrones. Este nivel de micronización mejora la tasa de disolución de los API, lo que es fundamental para mejorar la solubilidad del fármaco. El diseño cerrado de los molinos de chorro garantiza un procesamiento sin contaminación, lo que los hace ideales para formulaciones de fármacos sensibles.
Garantizar un tamaño de partícula uniforme para una mejor biodisponibilidad
El tamaño uniforme de las partículas desempeña un papel fundamental en la eficacia de los productos farmacéuticos. Al utilizar un micronizador de molino de chorro, se pueden lograr distribuciones uniformes del tamaño de las partículas, que afectan directamente a las tasas de absorción de los principios activos. Esta uniformidad garantiza que cada dosis proporcione el efecto terapéutico deseado. También simplifica los flujos de trabajo de producción, lo que da como resultado medicamentos de mayor calidad con biodisponibilidad predecible.
Industria alimentaria
Moler especias y aromas hasta convertirlos en polvos finos
Los micronizadores de molino de chorro se utilizan ampliamente en la industria alimentaria para Moler ingredientes como especias, azúcar y harina. en polvos ultrafinos. Este proceso crea una distribución estrecha del tamaño de las partículas, lo cual es esencial para aplicaciones que requieren uniformidad. Por ejemplo, las especias finamente molidas mejoran la liberación del aroma y garantizan una distribución uniforme del sabor en los productos alimenticios.
Procesamiento de aditivos alimentarios para mejorar la textura y la consistencia
La reducción del tamaño de las partículas mejora la textura y la consistencia de los productos alimenticios. Las partículas más pequeñas se distribuyen de manera más uniforme, lo que mejora el sabor y las características sensoriales. Esta uniformidad también contribuye a extender la vida útil al mejorar la evaporación de la humedad y la oxidación de las grasas. Ya sea que esté procesando aditivos alimentarios o nutracéuticos, los micronizadores de molino de chorro lo ayudan a lograr resultados consistentes en todos los lotes.
Industria química
Producción de productos químicos finos, pigmentos y catalizadores.
En la industria química, controlar el tamaño de las partículas es crucial para aplicaciones como pigmentos y catalizadores. Los micronizadores de molino de chorro permiten producir polvos finos con distribuciones de tamaño precisas. Por ejemplo, los pigmentos de dióxido de titanio alcanzan una reflectividad óptima cuando el tamaño de sus partículas coincide con la longitud de onda de la luz visible. De manera similar, los catalizadores se benefician de tamaños de partículas más pequeños, lo que mejora su actividad y selectividad.
Aplicaciones en polímeros y materiales avanzados
Los micronizadores de molino de chorro son indispensables para producir materiales avanzados y polímeros de alto rendimiento. Estos dispositivos minimizan la generación de calor durante la molienda, lo que evita la degradación térmica de materiales sensibles. También reducen la contaminación, lo que garantiza la calidad y el rendimiento del producto final. El control preciso del tamaño de las partículas le permite crear materiales con propiedades mejoradas, como una mayor resistencia o conductividad.
Otras industrias
Aplicaciones en cosmética para polvos finos
Los micronizadores de molino de chorro desempeñan un papel fundamental en la industria cosmética, ya que producen polvos ultrafinos. Puede utilizar esta tecnología para moler materiales hasta obtener partículas de tamaño tan pequeño como 1 a 10 micrones. Este nivel de precisión es esencial para crear productos cosméticos suaves y de alta calidad. Por ejemplo, los minerales micronizados como el dióxido de titanio y el óxido de zinc mejoran el acabado y la sensación del maquillaje, como las bases y los polvos faciales. Estos minerales también mejoran la capacidad del producto para mezclarse perfectamente con la piel, lo que proporciona un aspecto natural e impecable.
Desde la década de 1930, los fabricantes han recurrido a pulverizadores para satisfacer las demandas de los consumidores de polvos finos. En 1935, Coty introdujo los polvos faciales "AirSpun", que utilizaban molinos de aire para lograr su textura característica. En la década de 1940, los molinos de chorro surgieron como una opción superior, ofreciendo tamaños de partículas aún más finos. Hoy en día, los molinos de chorro siguen siendo la opción preferida por los fabricantes de cosméticos debido a su capacidad para producir polvos con baja contaminación y una distribución estrecha del tamaño de las partículas. Esto garantiza una calidad y seguridad constantes, especialmente para productos para pieles sensibles.
Las principales ventajas de los molinos de chorro en el sector cosmético incluyen:
- Mejora de la calidad del producto:Los polvos micronizados crean una textura más suave y una mejor cobertura.
- Baja contaminación:La ausencia de medios de molienda garantiza la pureza.
- Facilidad de uso:Los molinos de chorro son robustos y adecuados para la producción a gran escala.
Uso en electrónica para producir materiales con tamaños de partículas precisos.
En la industria electrónica, la precisión lo es todo. Los micronizadores de molino de chorro le ayudan a crear materiales con tamaños de partículas exactos, lo que es fundamental para la fabricación de componentes de alto rendimiento. Por ejemplo, los polvos finos son esenciales para producir pastas conductoras, condensadores cerámicos y semiconductores avanzados. Estos materiales requieren distribuciones de tamaño de partículas ajustadas para garantizar una conductividad eléctrica y una fiabilidad óptimas.
Los molinos de chorro son excelentes para procesar materiales como silicio, óxido de aluminio y otras cerámicas avanzadas. La naturaleza no térmica del proceso evita daños por calor, lo que preserva las propiedades del material. Esto es especialmente importante para la electrónica, donde incluso las impurezas o inconsistencias menores pueden comprometer el rendimiento.
También apreciará la escalabilidad de los molinos de chorro. Ya sea que trabaje en una investigación a pequeña escala o en una producción a gran escala, estos dispositivos se adaptan a sus necesidades. Su capacidad para producir polvos uniformes garantiza que sus componentes electrónicos cumplan con los estrictos estándares de la industria.
Las aplicaciones clave en electrónica incluyen:
- Materiales conductores:Producción de polvos finos para tintas y pastas conductoras.
- Componentes cerámicos:Creación de polvos uniformes para condensadores y aislantes.
- Semiconductores:Lograr tamaños de partículas precisos para microchips avanzados.
Los micronizadores de molino de chorro brindan la precisión y confiabilidad que necesita para mantenerse competitivo en el mercado de la electrónica en rápida evolución.
Los micronizadores de molino de chorro funcionan mediante el uso de chorros de gas de alta velocidad para acelerar las partículas dentro de una cámara de molienda. Las colisiones entre las partículas y las paredes de la cámara las rompen en fragmentos más pequeños. Este proceso, impulsado por la dinámica de fluidos, garantiza una reducción de tamaño eficiente al tiempo que evita la aglutinación de partículas. Usted se beneficia de la capacidad de esta tecnología para producir polvos finos con una distribución de tamaño uniforme.
Las principales ventajas incluyen un control preciso del tamaño de las partículas, una baja contaminación y la idoneidad para materiales sensibles al calor. Estas características hacen que los micronizadores de molino de chorro Esencial para industrias como la farmacéutica., donde mejoran la solubilidad de los fármacos, o el procesamiento de alimentos, donde mejoran el sabor y la textura. Su versatilidad garantiza resultados consistentes en diversas aplicaciones.
Preguntas frecuentes
¿Cuál es el propósito principal de un micronizador de chorro?
Un micronizador de chorro reduce el tamaño de las partículas al rango de micrones o submicrones. Utiliza chorros de gas de alta velocidad para crear colisiones de partículas, rompiéndolas en fragmentos más pequeños. Este proceso garantiza un control preciso del tamaño para aplicaciones que requieren polvos finos.
¿Qué materiales se pueden procesar con un micronizador de chorro?
Puede procesar una amplia gama de materiales, incluidos productos farmacéuticos, ingredientes alimentarios, pigmentos, polímeros y cerámicas avanzadas. Sin embargo, funciona mejor con materiales secos, frágiles o sensibles al calor que puedan soportar colisiones a alta velocidad.
¿Qué hace que los micronizadores de chorro sean diferentes de los molinos tradicionales?
Los micronizadores de molino de chorro utilizan gas de alta velocidad en lugar de medios de molienda. Esto elimina los riesgos de contaminación y minimiza la generación de calor. Los molinos tradicionales dependen de la molienda mecánica, que puede introducir impurezas y calor, lo que los hace inadecuados para materiales sensibles.
¿Qué industrias se benefician más de los micronizadores de chorro?
Las industrias como la farmacéutica, la alimentaria, la química, la cosmética y la electrónica son las más beneficiadas. Estos sectores requieren un control preciso del tamaño de las partículas, una baja contaminación y la capacidad de procesar materiales sensibles al calor de manera eficiente.
¿Qué factores afectan el rendimiento de un micronizador de molino de chorro?
La presión del gas, el caudal y la velocidad de alimentación afectan directamente el rendimiento. Una presión de gas más alta produce partículas más finas, mientras que una velocidad de alimentación más rápida produce tamaños más gruesos. El equilibrio de estos factores garantiza resultados óptimos para su aplicación específica.