There are many methods for forming special ceramics, such as dry pressing, slip casting, injection molding, and gel casting. Dry pressing offers advantages such as low binder content, direct sintering without drying. I a simple production process, high efficiency, small green body shrinkage, and automated production. It is the most commonly used method in the production of special ceramics.
How to prepare a green body with high density and uniform density gradient is the focus of the research. Generally speaking, the factors affecting the density of the green body during dry pressing are the dry pressing process and powder properties.
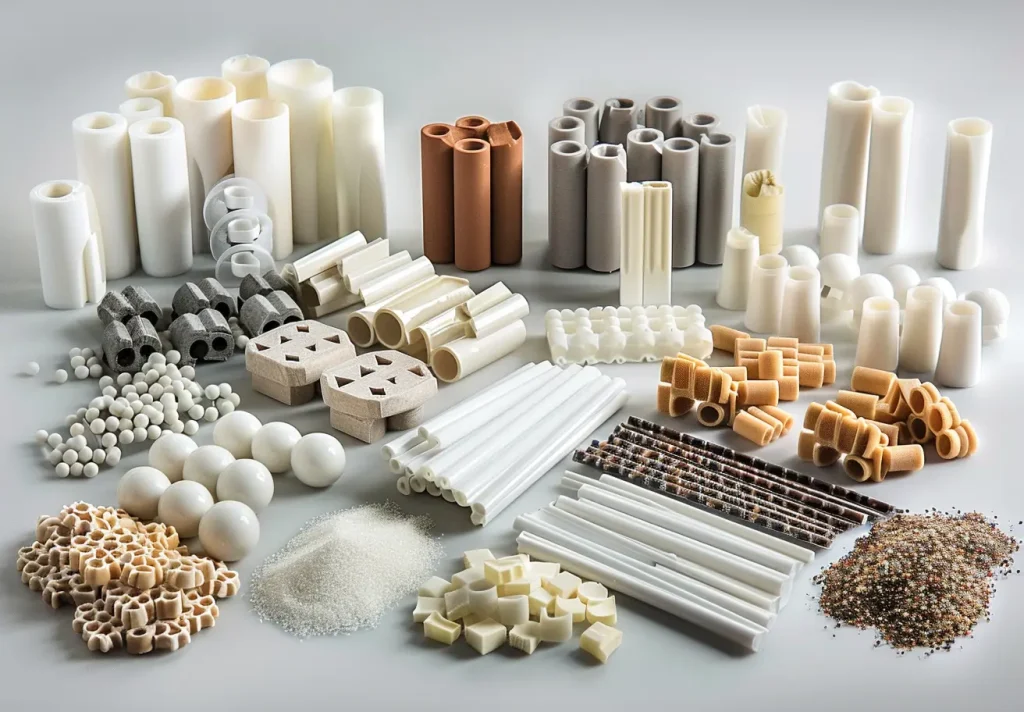
Influence of dry pressing process
Dry pressing process mainly refers to the pressurization method, pressurization pressure, pressurization speed and holding time.
Pressurization method
In dry pressing molding, the pressurization methods include unidirectional pressurization and bidirectional pressurization. Different pressurization methods will result in different transmission and distribution of pressure in the mold.
Pressing Pressure
Generally speaking, the density of the green body increases with the increase in pressure. During the special ceramics pressing process, the influence of pressure on the density, strength, and porosity of the green body is more significant than that of other factors. It also has a substantial impact on the performance of the green body after sintering.
If the pressure is too low, the green body cannot achieve maximum densification, which affects the sintering process. On the other hand, if the pressure is too high, defects similar to layer cracking may appear. Only when the pressure is at an optimal level can the ideal green body be achieved.
Pressurization Speed and Holding Time
The pressurization speed and holding time significantly influence the performance of the blank, as they are closely related to the transmission of pressure and the discharge of gas. If the pressurization is too fast and the holding time too short, the gas will not be easily discharged. Similarly, when the pressure is not transmitted to the required depth, the external force will be removed before proper densification, making it difficult to achieve the desired blank quality. However, if the pressurization speed is too slow and the holding time too long, production efficiency will decrease. Therefore, the pressurization speed and holding time should be adjusted according to the size, shape, and thickness of the blank.
The primary focus of research is how to prepare a green body with high density and a uniform density gradient. Generally speaking, the factors affecting the density of the green body during dry pressing include the dry pressing process and powder properties.
Influence of the Dry Pressing Process
The dry pressing process primarily refers to the pressurization method, pressurization pressure, pressurization speed, and holding time.
In dry pressing molding, the pressurization methods include unidirectional and bidirectional pressurization. Different pressurization methods result in different transmission and distribution of pressure in the mold.
The properties of the powder mainly refer to particle size, particle grading, binder and water content, and powder fluidity.
Particle Size and Particle Grading
Under the same pressure, the green compact density of powder with a large particle size is higher, while the sintering density of powder with a smaller particle size is greater. For powders with the same particle size, both the green compact density and the sintering density increase with higher pressure. Therefore, increasing the particle size is beneficial for improving the green body density.
Influence of Binder and Water Content
When special ceramics are dry pressed, the ceramic powder must first be granulated to meet the requirements, and then the granulated powder is pressed to form the green body. The properties of the granulated powder—such as the shape, size, size distribution, and fluidity of pseudo-particles—will ultimately affect the density of the ceramic green body. The binder content also plays a crucial role in the performance of the granulated powder. During special ceramic dry pressing, the binder primarily serves as a bonding agent, increasing the particle size of pseudo-particles and enhancing particle strength.
If the binder content is too high during the granulation process, the viscosity coefficient of the slurry increases, resulting in a smaller spray atomization angle. This causes the droplets to agglomerate after drying and granulation, leading to a powder with a wide particle size distribution and poor fluidity. As a result, it becomes difficult to obtain a high-density green body during dry pressing. Conversely, if the binder content is too low, the strength of the green body will fail to meet processing requirements.
Water content also significantly impacts the density of the green body. If the water content is too high, drying shrinkage will be substantial, making it challenging to control the size of the green body. Additionally, the powder may adhere to the mold during molding, negatively affecting the green body’s density. On the other hand, if the water content is too low, it will hinder the crushing performance of the granulation powder, making it harder to obtain a high-density green body.
Powder Fluidity
Good fluidity ensures that the internal friction between particles is minimal during special ceramics dry pressing, allowing the powder to smoothly fill every corner of the mold. This also helps to increase the filling density of the powder, enabling the formation of a dense and uniform ceramic body under lower pressure.
Choose Epic Powder air classifier for efficient, energy-saving, and environmentally friendly kaolin processing solutions!
Contact us to learn more about our products!