The grain and feed dust collector manages the dust generated in the crushing section of feed mills. It usually uses a bag pulse dust collector. After crushing, we collect the material using sedimentation and pulse dust removal. A bucket elevator transports the material to back-end equipment or silos. An auger conveys it horizontally.
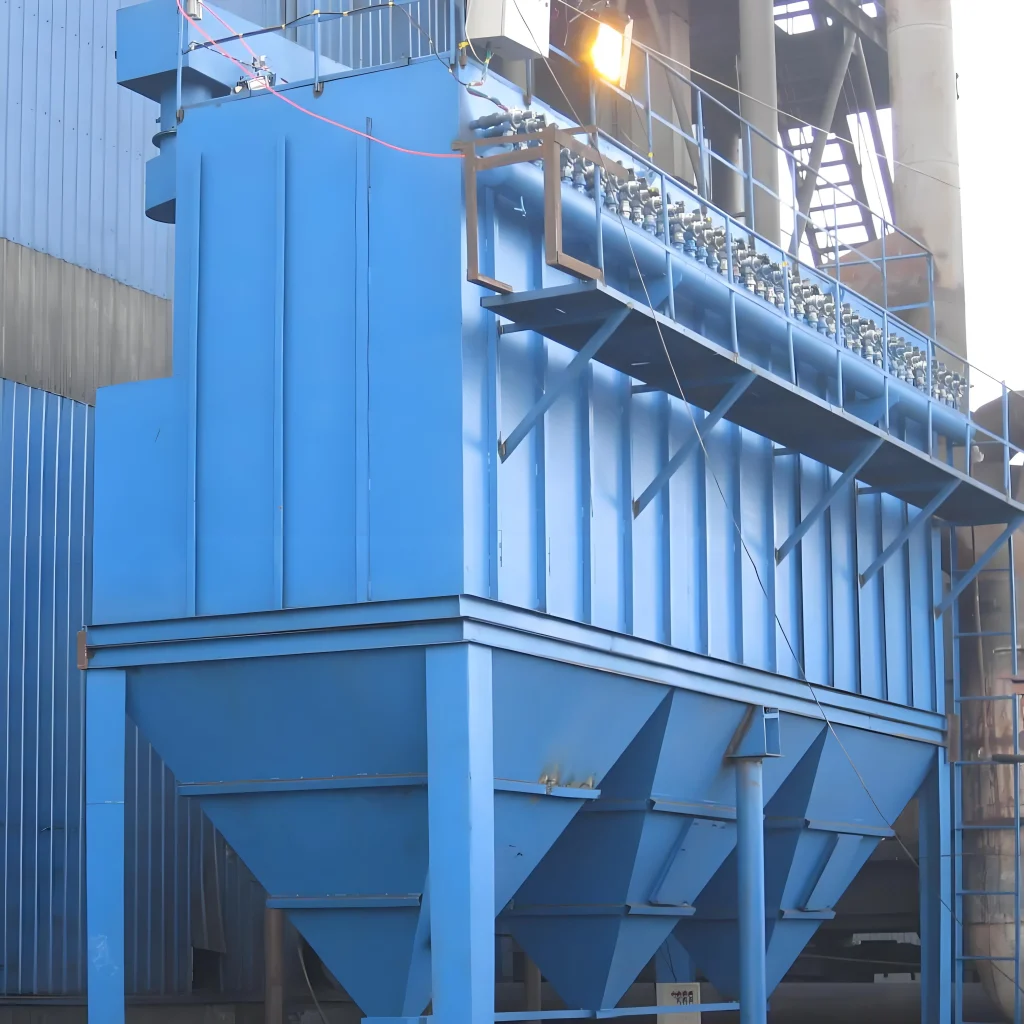
The grain processing industry uses pulse bag dust collectors, which have the following features:
1. It has a common blowing device and uses a cabinet-type disassembled dust collector bag structure, which is easy to repair.
2. The grain factory dust collector has a compact structure, flexible technical layout, small footprint, large filtration area (a single bag filtration area is up to 1 square meter), and high dust removal efficiency (≥99%).
3. The fan and pulse are now one. This simplifies the tech process, shortens the wind network, and reduces resistance.
4. The right-angle electromagnetic pulse valve is selected. It requires low air source pressure, has a large single air spray volume and low air consumption.
5. The filter bag can be checked or replaced from the top of the dust collector. Its design features ensure the versatility and simplicity of operation of the dust collector.
The most important and core component of the bag dust collector in grain and feed factories is the dust filter bag, which primarily captures dust-containing gas to achieve purification.
Grain feed dust collectors classify materials in the crushing section of feed mills, typically using a bag pulse dust collector. The crushing process is mainly designed for ordinary aquatic feed.
The working principle of a grain pulse bag dust collector is as follows:
Dust-containing gas enters the filter chamber from the ash hopper (or the lower open flange). The coarser particles fall directly into the ash hopper or ash silo. The filter bag filters the dust-containing gas, and the dust is retained on the bag surface. The clean gas goes to the clean air chamber through the bag mouth. Then the fan discharges it into the atmosphere.
When the dust on the surface of the filter bag continues to increase, causing the equipment resistance to rise to the set value, the time relay (or micro differential pressure controller) outputs a signal. The program controller starts to work and opens the pulse valves one by one, allowing compressed air to blow and clean the filter bags through the nozzles, causing the filter bags to suddenly expand.
Under the action of the reverse airflow, the dust attached to the bag surface quickly breaks away from the filter bag and falls into the ash hopper (or ash bin). The ash discharge valve discharges the dust. After all the filter bags are blown and cleaned, the dust collector resumes normal operation.