Les progrès des technologies de traitement du carbonate de calcium lui ont permis de passer d'une charge traditionnelle à un modificateur. Cette évolution permet de réduire les coûts des produits tout en améliorant leurs propriétés. Certaines d'entre elles sont propres au carbonate de calcium. La nouvelle technologie de micro-moussage et le carbonate de calcium creux peuvent réduire le poids. Ils permettent d'obtenir des composites de carbonate de calcium plus légers. Ils sont prêts pour la production industrielle.
Nous pouvons prédire avec confiance qu'à l'avenir, le carbonate de calcium plastique composite Les matériaux redéfiniront le cadre traditionnel des « deux réductions et une amélioration », à savoir la réduction des coûts et de la densité tout en améliorant les performances. Le carbonate de calcium passera d'un simple agent de remplissage à un modificateur révolutionnaire.
Les matériaux composites traditionnels à base de carbonate de calcium plastique n'entraînent pas seulement une réduction de toutes les propriétés du matériau. Au contraire, ils peuvent également améliorer divers attributs tout en provoquant certaines dégradations des performances. Cet article explorera spécifiquement les effets positifs et négatifs du carbonate de calcium en tant que modificateur. Il nous guide dans l'apprentissage du développement de la modification du carbonate de calcium dans le cadre de recherches futures.
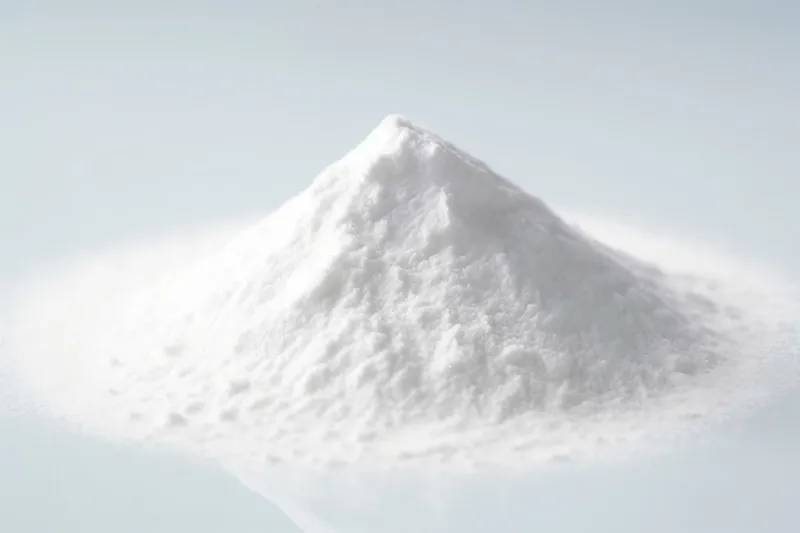
Effets positifs de modification du carbonate de calcium
1 Avantages environnementaux du carbonate de calcium
1.1 Conservation des ressources pétrolières
Impact calculé du carbonate de calcium dans les emballages en plastique
En utilisant du carbonate de calcium 30% dans le PE, 3 millions de tonnes de sacs en plastique pourraient économiser 900 000 tonnes de résine à base de pétrole et 2,7 millions de tonnes de pétrole.
1.2 Performances respectueuses de l'environnement
L’incorporation de carbonate de calcium dans les sacs poubelles en plastique destinés à l’incinération peut améliorer l’efficacité de la combustion et réduire considérablement le temps d’incinération. Lors de la combustion, le carbonate de calcium se dilate dans le film plastique, créant de nombreux petits trous qui augmentent la surface disponible pour la combustion. Ce phénomène accélère le processus de combustion. Par exemple, le temps d’incinération d’un film plastique en polyéthylène contenant du carbonate de calcium 30% est réduit de 12 secondes (pour du plastique pur) à seulement 4 secondes.
De plus, les films plastiques remplis de carbonate de calcium favorisent une combustion plus complète. Cela minimise la fumée noire due à l'effet mèche du carbonate de calcium. L'alcalinité du carbonate de calcium aide à absorber les gaz acides. Cela réduit la fumée toxique et le risque de pluies acides.
Au Japon, la réglementation stipule que les sacs poubelles en plastique destinés à l'incinération doivent contenir au moins 30% de carbonate de calcium. En plus de la vitesse de combustion améliorée, les sacs remplis de carbonate de calcium génèrent moins de chaleur, ne produisent pas de gouttes ou de fumée noire, atténuent la pollution secondaire et ne sont pas nocifs pour les incinérateurs.
2. Effets de modification courants du carbonate de calcium
2.1 Amélioration de la rigidité des matériaux composites
Le carbonate de calcium améliore la résistance à la flexion, le module de flexion, la dureté et la résistance à l'usure des matériaux composites. Dans les films plastiques, la rigidité accrue améliore considérablement la rigidité, facilitant le gondolage à plat et l'intégrité structurelle globale.
2.2 Stabilité dimensionnelle améliorée des matériaux composites
Le carbonate de calcium contribue à améliorer la stabilité dimensionnelle en réduisant le retrait et le gauchissement, en abaissant le coefficient de dilatation linéaire, en minimisant le fluage et en favorisant l'isotropie. L'inclusion de carbonate de calcium dans les composites améliore considérablement la stabilité dimensionnelle.
2.3 Amélioration de la résistance à la chaleur des matériaux composites
Le carbonate de calcium améliore la stabilité thermique des matériaux composites en absorbant les substances qui favorisent la décomposition. Par exemple, les composites PBAT/carbonate de calcium présentent une stabilité thermique nettement supérieure à celle du PBAT pur. De plus, l'incorporation de carbonate de calcium léger dans les produits en PVC absorbe efficacement le chlorure d'hydrogène produit pendant la décomposition, améliorant ainsi considérablement la stabilité thermique du PVC lors du traitement.
2.4 Résistance accrue des films à la déchirure
Les films plastiques classiques ont souvent une résistance longitudinale élevée mais une faible résistance transversale, en particulier dans les matériaux tels que les films polyester aliphatique PBS, PLA et PHA. L'ajout de carbonate de calcium peut améliorer l'isotropie de ces matériaux composites, ce qui conduit à une résistance à la déchirure considérablement améliorée.
3. Propriétés spéciales modifiées du carbonate de calcium
3.1 Effets sur les propriétés de traction et d'impact
L’impact du carbonate de calcium sur la résistance à la traction et la résistance aux chocs des films plastiques n’est pas universel ; il est influencé par des facteurs tels que la taille des particules et le traitement de surface.
Effet de la taille des particules : Français Différentes tailles de particules de carbonate de calcium produisent des effets de modification variables sur les plastiques, comme illustré dans le tableau 1. En général, des tailles de particules inférieures à 1000 mesh sont utilisées pour une modification incrémentielle. Des tailles de particules comprises entre 1000 et 3000 mesh, avec une quantité ajoutée inférieure à 10%, peuvent produire certains effets de modification. En revanche, le carbonate de calcium avec des tailles de particules supérieures à 5000 mesh, classé comme carbonate de calcium fonctionnel, présente des effets de modification significatifs et peut améliorer à la fois la résistance à la traction et la résistance aux chocs. Bien que le carbonate de calcium à l'échelle nanométrique ait une taille de particule plus fine, sa difficulté actuelle de dispersion limite son efficacité, le limitant à des résultats de modification similaires à ceux du carbonate de calcium à 8000 mesh.
Tableau 1 : Effet du carbonate de calcium lourd avec différentes tailles de particules sur les performances des matériaux composites PP
Agent de couplage traité carbonate de calcium lourd (30%) taille de maille | 2000 | 1250 | 800 | 500 |
Indice de fluidité à chaud (g/10min) | 4.0 | 5.0 | 5.6 | 5.5 |
Résistance à la traction (MPa) | 19.3 | 18.4 | 18.7 | 18.1 |
Allongement à la rupture (%) | 422 | 420 | 341 | 367 |
Résistance à la flexion (MPa) | 28 | 28.6 | 28.2 | 28.4 |
Module de flexion (MPa) | 1287 | 1291 | 1303 | 1294 |
Résistance aux chocs Izod (J/m) | 113 | 89 | 86 | 78 |
Comme le montre le tableau 1, des particules plus fines de carbonate de calcium entraînent une augmentation de la résistance aux chocs, de la résistance à la traction et de l'allongement à la rupture, tandis que la résistance à la flexion et le module de flexion restent relativement inchangés. Cependant, la fluidité du matériau composite diminue avec des particules plus fines.
Effet du traitement de surface : Un traitement de surface approprié du carbonate de calcium avec des tailles de particules adaptées peut améliorer considérablement la résistance à la traction et aux chocs des matériaux composites. Récemment, les progrès de la théorie des composites organiques/inorganiques ont transformé le carbonate de calcium d'une simple charge en un nouveau matériau de charge fonctionnel. Par exemple, la résistance aux chocs entaillés d'un composite homopolymère polypropylène (PP)/carbonate de calcium peut plus que doubler par rapport au plastique de base.
3.2 Suppression de la fumée pendant la combustion
Le carbonate de calcium présente d'excellentes capacités de suppression de fumée. Cela est dû à sa capacité à réagir avec les halogénures d'hydrogène dans la fumée, formant du chlorure de calcium stable (CaCl₂). Par conséquent, il peut être utilisé comme suppresseur de fumée dans tout polymère produisant des halogénures d'hydrogène pendant la combustion, y compris le chlorure de vinyle, le polyéthylène chlorosulfoné et le caoutchouc chloroprène.
La combustion étant une réaction hétérogène solide-gaz qui se produit à la surface des particules solides, la taille des particules de carbonate de calcium joue un rôle crucial dans son efficacité de suppression de fumée. Les particules plus fines possèdent une surface spécifique nettement plus grande, ce qui renforce l'effet de suppression de fumée.
3.3 Agent anti-adhérent
Les films tubulaires soufflés contenant du carbonate de calcium présentent d'excellentes propriétés d'ouverture et résistent à l'adhérence lors du bouclage. Dans ce contexte, le carbonate de calcium fonctionne efficacement comme agent anti-adhérent.
3.4 Augmenter la conductivité thermique
L'ajout de carbonate de calcium augmente la conductivité thermique du film. La bulle du film soufflé refroidit plus rapidement. Cela augmente la production et le rendement de l'extrudeuse. En prenant comme exemple le carbonate de calcium léger 25% dans une feuille de PVC, il ne faut que 3,5 secondes pour le chauffer à 200 °C. Une feuille de PVC pur prend 10,8 secondes. La conductivité thermique a été multipliée par 3.
3.5 Améliorer la fluidité
Le carbonate de calcium peut améliorer la fluidité du système composite, réduire la viscosité de la masse fondue et le couple de l'extrudeuse, augmenter le rendement de l'extrudeuse et améliorer l'efficacité de la production. Différents types de carbonate de calcium ont des effets différents sur l'écoulement. L'ordre de fluidité du matériau composite spécifique est le suivant : carbonate de calcium de grande calcite > carbonate de calcium de marbre, carbonate de calcium de dolomite > carbonate de calcium de petite calcite > carbonate de calcium léger.
3.6 Performances de correspondance des couleurs
Remplacement de certains pigments blancs : Le carbonate de calcium à haute blancheur peut remplacer certains pigments blancs tels que le dioxyde de titane, ce qui permet d'économiser la teneur en dioxyde de titane coûteux. Le carbonate de calcium à grande calcite est le premier choix en raison de sa blancheur élevée et de son pouvoir couvrant élevé. La raison pour laquelle le carbonate de calcium peut être utilisé comme pigment blanc est principalement parce qu'il possède un certain pouvoir couvrant. Le pouvoir couvrant d'un revêtement fait référence à la quantité minimale de peinture nécessaire pour appliquer uniformément la peinture sur la surface d'un objet de sorte que la couleur de base n'apparaisse plus. Il est exprimé en g/㎡.
Le pouvoir couvrant de divers colorants dans les revêtements est indiqué dans le tableau 2 :
Tableau 2 : Pouvoir masquant de certains pigments inorganiques et organiques
Nom du pigment | Pouvoir couvrant (g/cm) |
Para rouge (teinte claire) | 18.1-16.3 |
Para rouge (teinte foncée) | 17.1-15.0 |
Lac rouge c | 23.8-18.8 |
Rouge lithol (lac Ba) | 33.7-21.7 |
Rouge lithol (lac Ca) | 49.0-33.7 |
Rubis lithol | 33.9 |
Lac écarlate des Yankees | 88.5 |
Rhodamine Y (précipité de tungstate) | 25.1 |
Rhodamine B (précipité de phosphotungstate) | 16.1 |
Rouge châtain toluidine | 34.8-37.7 |
Rouge résistant à la lumière BL | 12.4 |
Dioxyde de titane | 18.4 |
(type rutile, type anatase) | 19.5 |
Oxyde de zinc | 24.8 |
Sulfate de baryum | 30.6 |
Carbonate de calcium | 31.4 |
Hansa jaune G | 54.9 |
Hansa jaune 10G | 58.8 |
Orange permanent | 29.6 |
Vert malachite | 5.4 |
Pigment vert B | 2.7 |
Bleu malachite (précipité de phosphotungstate) | 7.7 |
Malachite bleue | 68.5 |
Violet de méthyle (précipité de phosphotungstate) | 7.6 |
Violet de méthyle (précipitant de tanin) | 4.9 |
Violet résistant au soleil | 10.2 |
Bleu de phtalocyanine | 4.5 |
Mortier de zinc baryum (poudre de plomb) | 23.6 |
Mortier de plomb (sulfate de plomb basique) | 26.9 |
Trioxyde d'antimoine | 22.7 |
Talc | 32.2 |
Le pouvoir masquant d'un matériau est étroitement lié à son indice de réfraction. En général, un indice de réfraction plus élevé se traduit par un pouvoir masquant plus important et une teinte blanche plus intense. L'indice de réfraction de divers matériaux blancs est détaillé dans le tableau 3.
Tableau 3 : Indice de réfraction de divers matériaux blancs
Matériaux blancs | Numéro d'index du colorant | Indice de réfraction |
Dioxyde de titane (type rutile) | Mortier pigmentaire 6 | 2.70 |
Poudre de titane (type anatase) | Mortier pigmentaire 6 | 2.55 |
Oxyde de zirconium | Mortier pigmentaire 12 | 2.40 |
Sulfure de zinc | 2.37 | |
Trioxyde d'antimoine | Mortier pigmentaire 11 | 2.19 |
Oxyde de zinc | Mortier pigmentaire 4 | 2.00 |
Lithopone (poudre de zinc-baryum) | Mortier de couleur 21 | 2.10 |
Sulfate de baryum | Mortier pigmentaire 18 | 1.64 |
Carbonate de calcium | Mortier pigmentaire 27 | 1.58 |
Talc | Numéro d'index du colorant | 1.54 |
Impact sur la coloration La couleur blanche naturelle du carbonate de calcium influence sa capacité à s'harmoniser avec les couleurs vives, ce qui rend difficile l'obtention de combinaisons de couleurs vives. De plus, cela peut compliquer l'association de noirs spéciaux.
Impact sur la lumière colorée Au-delà de sa couleur blanche naturelle, le carbonate de calcium peut présenter différentes lumières colorées, affectant la pureté des couleurs. La lumière colorée fait référence aux teintes supplémentaires qu'un objet affiche en plus de sa couleur principale. Par exemple, les couleurs complémentaires se trouvent aux extrémités opposées du spectre des couleurs ; le bleu, par exemple, est complété par le jaune. Le mélange de ces couleurs peut produire une lumière blanche, une méthode efficace pour neutraliser la lumière colorée.
La couleur de base émise par le carbonate de calcium varie selon l'origine. Par exemple :
- Le carbonate de calcium du Sichuan a une couleur de base bleue.
- Le carbonate de calcium du Guangxi a une couleur de base rouge.
- Le carbonate de calcium du Jiangxi a également une couleur de base bleue.
Lors de l'association des couleurs, la lumière de couleur du carbonate de calcium doit correspondre à la teinte de la coloration primaire. Par exemple, le carbonate de calcium avec une teinte bleue peut contrecarrer le pouvoir colorant des pigments jaunes. Il est également couramment utilisé pour neutraliser la lumière de couleur jaune dans les produits.
Amélioration de l’astigmatisme dans les produits en plastique : Bien que l’ajout de carbonate de calcium n’améliore pas la brillance des produits en plastique, il réduit efficacement la brillance, offrant un effet mat.
3.7 Augmentation de la respirabilité
Les films plastiques remplis de carbonate de calcium créent de minuscules pores lors de l'étirement, ce qui permet à la vapeur d'eau de passer à travers tout en empêchant l'infiltration d'eau liquide. Cette caractéristique les rend adaptés à la production de produits plastiques respirants. Pour des résultats optimaux, seul du carbonate de calcium avec une granulométrie de 3000 mesh ou plus fine doit être utilisé, avec une distribution granulométrique étroite.
3.8 Promouvoir la performance de dégradation des produits
Lorsque des sacs en polyéthylène contenant du carbonate de calcium sont enterrés, le carbonate de calcium peut réagir avec le dioxyde de carbone et l'eau pour former du bicarbonate de calcium hydrosoluble (Ca(HCO₃)₂), qui peut quitter le film. Ce processus crée de minuscules trous dans le film, augmentant la surface en contact avec l'air et les micro-organismes, facilitant ainsi la dégradation du produit.
3.9 Rôle de nucléation du carbonate de calcium
Le carbonate de nano-calcium (CaCO₃) joue un rôle crucial dans la nucléation de cristallisation du polypropylène, augmentant la teneur en cristaux β et améliorant ainsi la résistance aux chocs du polypropylène.
3.10 Réduction de l'absorption d'eau dans les plastiques PA
L'absorption d'eau des composites polyamide (PA)/carbonate de calcium est nettement inférieure à celle de la résine PA pure. Par exemple, l'incorporation de carbonate de calcium 25% dans le PA6 peut réduire le taux d'absorption d'eau du matériau composite de 56%.
3.11 Amélioration des propriétés de surface
Le carbonate de calcium peut améliorer la tension superficielle des matériaux composites. Il possède d'excellentes propriétés d'adsorption. Cela améliore leurs qualités de galvanoplastie, de revêtement et d'impression.
3.12 Effets du carbonate de calcium sur la formation de mousse
L'influence du carbonate de calcium sur les performances de moussage des matières plastiques est complexe et dépend à la fois de la taille des particules et de la quantité utilisée :
Carbonate de calcium Taille : Lorsque la taille des particules de carbonate de calcium correspond à celle de l'agent moussant, il peut agir comme agent de nucléation. Ce processus influence positivement la formation de mousse. La taille idéale des particules est inférieure à 5 μm et doit éviter l'agglomération. Si la taille des particules dépasse 10 μm ou est trop fine et s'agglomère, cela peut avoir un impact négatif sur la formation de mousse. Il est recommandé d'utiliser du carbonate de calcium de 3000 mesh (environ 4 μm) pour garantir une taille inférieure à 5 μm sans agglomération.
Les mécanismes par lesquels le carbonate de calcium favorise la formation de mousse comprennent :
Agissant comme agent de nucléation en absorbant le gaz moussant pour créer des noyaux de bulles, contrôlant ainsi le nombre de pores et affinant leur taille.
Assure une rigidité qui ralentit la déformation et la mobilité de la masse fondue, ce qui contribue à inhiber l'expansion rapide des pores et permet des tailles de pores plus fines. Le carbonate de calcium nanométrique peut même générer des plastiques en mousse microporeux en raison de la petite taille de l'agent de nucléation.
Quantité de carbonate de calcium ajoutée : La quantité optimale de carbonate de calcium pour améliorer la qualité de la mousse varie généralement entre 10% et 30%. Si la quantité est trop faible, le nombre de points de nucléation sera insuffisant, ce qui entraînera un faible taux de moussage. À l'inverse, si la quantité est trop importante, alors que davantage de points de nucléation sont créés, la résistance à la fusion peut diminuer de manière excessive. Cela entraîne de nombreuses bulles cassées et un taux de moussage réduit.
Dispersibilité du carbonate de calcium : Une dispersion uniforme du carbonate de calcium est essentielle pour favoriser la qualité de la mousse. Le carbonate de calcium uniformément réparti garantit l'absence d'agglomération. Si la taille des particules est inférieure à 5 μm, il fonctionnera efficacement comme agent de nucléation sans affecter négativement la formation de mousse.
Teneur en eau du carbonate de calcium : Si la teneur en eau de la poudre inorganique est inférieure à 0,5%, elle aura un impact minimal sur le moussage.
Autres propriétés: Le carbonate de calcium contribue également à améliorer la résistance à l’usure et la dureté des matériaux composites.
Modifications négatives des charges
1. Augmentation de la densité des matériaux composites
L'ajout de carbonate de calcium à la résine entraîne une augmentation rapide de la densité du matériau composite. Pour les produits vendus au poids, à la longueur ou à la surface, cette densité accrue peut compenser certains avantages en termes de coût. L'ampleur du gain de poids varie selon les différents types de carbonate de calcium, l'ordre de densité spécifique étant le suivant :
Carbonate de calcium léger < Carbonate de calcium de grande calcite < Carbonate de calcium de marbre < Carbonate de calcium de dolomite < Carbonate de calcium de petite calcite.
Comment réduire la densité des plastiques composites à base de carbonate de calcium :
1.1 Étirement du produit pour la réduction de poids :
L'étirement crée des espaces de déformation entre le plastique et le carbonate de calcium, réduisant légèrement la densité globale. Par exemple, un film de polyéthylène étiré rempli de carbonate de calcium 30% a une densité de 1,1 g/cm³, contre 1,2 g/cm³ pour la version non étirée. Cette technique est applicable à divers produits en plastique tels que le fil plat, le film soufflé, le ruban de cerclage et le film lacrymal.
1.2 Produit micro-moussant pour la perte de poids :
L'utilisation de l'humidité absorbée par la charge pour le micro-moussage peut réduire considérablement la densité sans compromettre les performances. Par exemple, notre matériau composite léger à base de carbonate de calcium 50% peut atteindre une densité minimale de 0,7 g/cm³ lorsqu'il est utilisé pour produire des films, ce qui représente une réduction de 45%.
1.3 Remplissage creux pour réduction de poids :
L'utilisation d'une technologie simple et économique de creusement de poudre inorganique permet de produire des produits creux en carbonate de calcium, ce qui réduit considérablement la densité. La densité de ces produits creux peut être réduite à environ 0,7 g/cm³.
2. Réduction de la brillance des matériaux composites
La méthode de traitement et le type de carbonate de calcium affectent la brillance de la surface des produits composites. L'ordre de brillance des différents matériaux composites est le suivant :
- Procédé humide > Procédé sec
- Carbonate de calcium léger > Carbonate de calcium à grande calcite > Carbonate de calcium à marbre > Carbonate de calcium à petite calcite > Carbonate de calcium à dolomite.
3. Réduction de la transparence dans les matériaux composites
Le carbonate de calcium a un indice de réfraction qui diffère considérablement de celui des résines courantes comme le polyéthylène et le polypropylène. Par conséquent, les charges de carbonate de calcium de taille conventionnelle peuvent avoir un impact négatif sur la transparence des films. Seul le carbonate de calcium nano, d'une taille inférieure à 200 nanomètres, peut conserver la transparence du composite. Les ondes lumineuses peuvent contourner efficacement ces petites particules.
4. Réduction de l'allongement à la rupture dans les matériaux composites
La rigidité élevée du carbonate de calcium peut diminuer la ductilité initiale du matériau composite. Cette rigidité accrue réduit la mobilité des chaînes macromoléculaires, ce qui entraîne une diminution de l'allongement à la rupture du produit final.
5. Diminution de la résistance à la traction et à l'impact
Dans de nombreux cas, l'ajout de carbonate de calcium peut entraîner une diminution de la résistance à la traction et de la résistance aux chocs du matériau composite. Cela est particulièrement vrai si les particules de carbonate de calcium sont trop grosses ou si le traitement de surface du carbonate de calcium est inadéquat. La baisse la plus notable est souvent observée au niveau de la résistance à la traction.
6. Augmentation du phénomène de blanchiment dû au stress
Si vous ajoutez beaucoup de carbonate de calcium à la résine, cela peut provoquer des fissures et des traces argentées lorsque le produit est étiré. Cela aggrave le blanchiment sous contrainte de la résine.
7. Accélération du vieillissement des produits
Tous les matériaux en poudre inorganiques, y compris le carbonate de calcium, peuvent accélérer le vieillissement des matériaux composites, entraînant une réduction de la longévité et des performances des produits.
8. Résistance de liaison réduite entre les matériaux
L'utilisation de carbonate de calcium peut diminuer la force de liaison des films, par exemple en réduisant la résistance du thermoscellage, et peut également diminuer la résistance de soudage des tuyaux.