Pour le carbonate de calcium ultrafin, la granulométrie, la surface spécifique, la forme cristalline et l'absorption d'huile sont des indicateurs techniques clés. Ces facteurs influencent directement les performances du produit. D'autres indicateurs sont également importants, mais généralement plus faciles à contrôler en production industrielle. Cependant, pour des applications spécialisées, les priorités varient selon les utilisations. Par conséquent, les indicateurs ne doivent pas être traités de la même manière dans tous les cas.
Taille des particules et surface spécifique
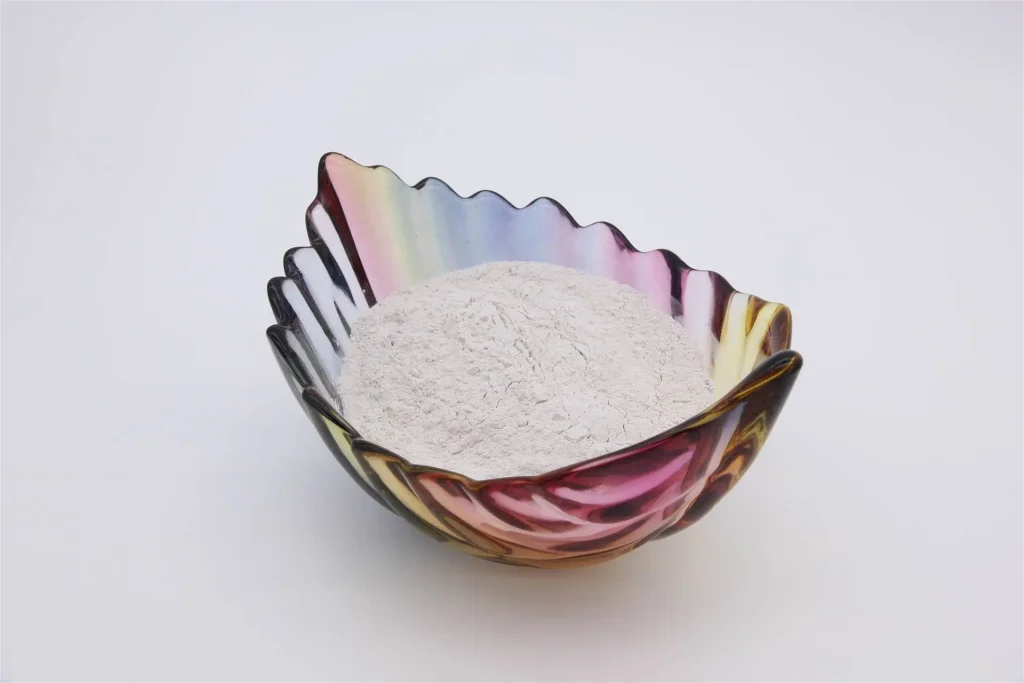
Obtenir une granulométrie primaire de 0,02 à 0,1 μm est une condition essentielle pour obtenir du carbonate de calcium ultrafin. Sans cela, il ne peut être qualifié d'« ultrafin ».
Cependant, la production de carbonate de calcium ultrafin de qualité ne représente que la moitié du travail. En l'absence de techniques de traitement de surface et de dispersion, les particules s'agglomérent en particules secondaires plus grosses.
Ces agglomérats peuvent atteindre des centaines de nanomètres. Les images obtenues par microscopie électronique à transmission (MET) ne montrent que les particules primaires.
En raison de la préparation des échantillons, ces valeurs ne reflètent pas la taille réelle des particules agglomérées. Les produits fortement agglomérés présentent généralement une surface BET plus faible.
Par conséquent, la combinaison des tests de surface TEM et BET offre une vision plus complète de la taille, de la forme et de la dispersion des particules. Il existe une relation naturelle entre la taille moyenne des particules et leur surface.
Certains chercheurs utilisent le volume de sédimentation pour estimer la taille des particules. Cependant, le volume de sédimentation n'est pas influencé uniquement par la taille.
Des facteurs tels que la qualité du calcaire, les conditions de calcination, de digestion et de carbonatation influencent tous la taille finale. De plus, le carbonate de calcium présente différentes formes cristallines. Même au sein d'une même forme, les formes diffèrent et sont souvent irrégulières. La forme des cristaux complique donc les résultats du volume de sédimentation.
Même au sein d'une même forme, les formes diffèrent et sont souvent irrégulières. La forme cristalline complique donc les résultats du volume de sédimentation. Utiliser le seul volume de sédimentation pour évaluer la taille des particules n'est pas scientifique et souvent inexact. Pour réduire l'agglomération, le carbonate de calcium ultrafin subit généralement une modification de surface.
Cela améliore non seulement l'activité de surface, mais contribue également à prévenir l'agrégation des particules. Pour les produits spécialisés, la forme cristalline, la taille des particules, l'agent de traitement de surface et même les techniques de traitement varient. L'expérience et le savoir-faire technique sont essentiels lors du traitement. Il est donc très difficile d'utiliser une norme unique pour évaluer tous les types de carbonate de calcium ultrafin.
Forme cristalline
La forme cristalline est également un indicateur technique crucial pour le carbonate de calcium ultrafin. Le carbonate de calcium léger standard a une forme fusiforme.
Utilisé dans le PVC, il crée des contraintes et provoque le blanchiment des films plastiques. La forme cristalline du carbonate de calcium ultrafin varie selon les applications. Pour les plastiques, une structure simple, un faible volume de remplissage et une faible absorption d'huile sont privilégiés. Les formes cubiques ou sphériques sont idéales.
Le carbonate de calcium ultrafin, avec des particules de 0,072 μm, améliore les performances du PVC. Il améliore la douceur, la brillance et l'isolation électrique de la surface.
Dans les composés de câbles souples, même avec un double dosage de charge, les performances restent conformes aux normes nationales. Dans les films plastiques, il réduit le blanchiment et augmente l'allongement à basse température.
Cependant, dans les plastiques rigides comme les portes et les profilés, il augmente la résistance aux chocs. La résistance aux chocs entaillés peut atteindre 49,1 kJ/m². Pour le caoutchouc, les formes en chaîne offrent le meilleur renforcement.
Le carbonate de calcium en chaîne se forme par l'alignement de nombreuses particules dans une même direction. Cette structure présente une stabilité spatiale et se disperse bien dans le caoutchouc.
Lors du mélange, les chaînes se brisent, exposant les surfaces actives. Ces surfaces se lient étroitement aux chaînes en caoutchouc, renforçant ainsi leur renforcement.
Dans le caoutchouc, la résistance du renfort selon la forme est la suivante : chaîne > aiguille > sphère > cube. Pour l'encre, les formes cubiques sont optimales en raison de leurs propriétés. Dans les encres à base de résine, le carbonate de calcium ultrafin devrait assurer brillance, transparence et fluidité.
Les cristaux cubiques offrent les meilleures performances de brillance. Pour le couchage du papier, on utilise généralement du carbonate de calcium précipité. Il n'est pas ultrafin ; sa taille varie de 0,1 à 1 µm. Néanmoins, la forme des cristaux est importante.
Les revêtements de papier doivent présenter une bonne opacité, une bonne brillance, une viscosité élevée et une bonne absorption de l'encre. Les formes cristallines idéales sont lamellaires et cubiques. En résumé, le carbonate de calcium ultrafin ne doit pas seulement répondre aux exigences de taille (0,02–0,1 μm).
mais peuvent également être adaptés sous forme de cristal en fonction de l'utilisation pour créer des produits prêts à être commercialisés.
Valeur d'absorption d'huile
La capacité d'absorption d'huile du carbonate de calcium ultrafin a un impact significatif sur ses performances d'application. Cela est particulièrement vrai pour les plastiques, les revêtements et les encres.
Une absorption d’huile élevée consomme plus de plastifiant dans les plastiques.
Dans les revêtements et les encres, il augmente la viscosité. L'absorption d'huile doit donc rester faible. De nombreux facteurs, au-delà des propriétés physiques du matériau, influencent l'absorption d'huile.
Parmi eux, la taille des particules est un facteur majeur. Il est donc essentiel de garantir une granulométrie fine et une bonne dispersion.
Il doit également avoir une surface correspondant à la taille de ses particules.
Ce n'est qu'à ce moment-là qu'il faut envisager de réduire l'absorption d'huile. Si la dispersion est mauvaise et que les particules s'agglomèrent fortement, la surface spécifique est très faible.
Même avec une faible absorption d’huile, un tel matériau a peu de valeur pratique.
Contenu principal
La teneur en carbonate de calcium ultrafin (CaO) ne doit pas être trop limitée. Dans la plupart des cas, le carbonate de calcium ultrafin sert de charge fonctionnelle, affectant les propriétés physiques plutôt que chimiques.
Dans une plage raisonnable, sa teneur en CaO peut encore répondre aux exigences de performance. Pour produire du carbonate de calcium présentant diverses formes cristallines, une bonne dispersion et une activité de surface élevée, des additifs tels que des modificateurs, des dispersants et des tensioactifs sont souvent ajoutés.
Ces « impuretés » ajoutées intentionnellement ne nuisent généralement pas aux performances du produit, et parfois même les améliorent. Cependant, elles peuvent réduire la teneur mesurée en CaO dans le produit final. Bien entendu, les éléments nocifs comme le fer et le manganèse doivent être rigoureusement contrôlés.
Qu'ils proviennent des matières premières ou du traitement, ils affectent la couleur et accélèrent la dégradation et le vieillissement de la résine. Il est donc impératif de les éviter. D'autres impuretés, comme le silicium, l'aluminium et le magnésium, affectent la blancheur du produit et peuvent nuire à l'efficacité du traitement.
Ainsi, les matières premières comme le calcaire doivent être soigneusement sélectionnées et contrôlées. Ainsi, des limites de teneur en CaO trop strictes peuvent restreindre le développement de produits spécialisés à base de carbonate de calcium ultrafin. Une gamme équilibrée est plus pratique. Résumé L'orientation clé du carbonate de calcium ultrafin est la spécialisation, le développement en série, la variété et la fonctionnalité.
Il est erroné de supposer qu'une granulométrie de 0,02 à 0,1 μm suffit à toutes les industries, comme celles du caoutchouc, du plastique, de l'encre, des revêtements ou du papier. Les applications exigent des exigences spécifiques en matière de granulométrie, de forme cristalline, de surface spécifique, d'absorption d'huile et de composition principale. Par conséquent, une norme universelle ne peut s'appliquer à tous les produits spécialisés de carbonate de calcium ultrafin.
À propos d'Epic Powder Machinery
Poudre épique Nos machines offrent des solutions de pointe pour le traitement des poudres ultrafines. Nous aidons nos clients à obtenir des résultats performants et personnalisés pour les plastiques, le caoutchouc, les revêtements, etc.