An increase in powder adhesiveness significantly reduces its flowability. The underlying mechanisms involve disruption of the balance of interparticle forces, microstructural reorganization, and changes in macroscopic mechanical responses. Based on data from multidisciplinary studies, the impact of adhesiveness on flowability can be summarized as follows:
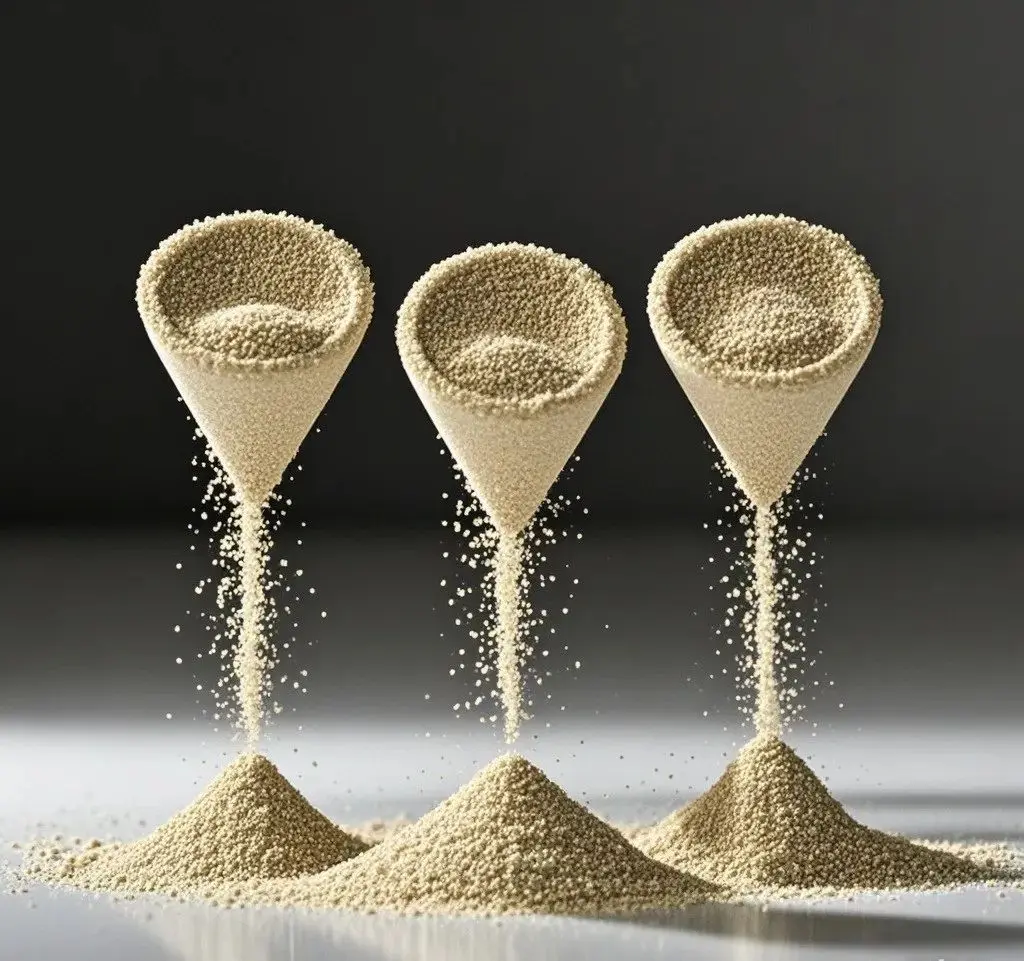
I. Destructive Mechanisms of Increased Adhesiveness
1. Imbalance of Interparticle Forces
Enhanced adhesiveness increases van der Waals forces, electrostatic forces, and liquid bridge forces between particles, leading to stable agglomerate formation.
For example, when the adhesion force of nano zirconia powder increases by 30%, the angle of repose rises from 35° to 45°, and the flow time increases by 50%.
For every 1 mN/m increase in adhesion, compressibility rises by 8–12%.
In a PVC-CPE system, when the calcium carbonate content increases by 5%, interparticle porosity drops by 20%, and flow time increases by 40%.
Microstructural Locking Effect
Higher adhesiveness causes particles to form network or chain-like structures that hinder particle slippage.
For example, after enhancing the adhesiveness of magnesium oxide powder, its cohesion increases from 0.8 kPa to 1.5 kPa, and the flow function (FF) drops from 4.5 to 2.8.
II. Observable Effects of Increased Adhesiveness
III. Case Studies: Adhesiveness vs. Flowability in Typical Materials
1. Nano Zirconia Powder
When particle size <50 nm, specific surface area >30 m²/g, and adhesion force >1.2 mN/m, the flow index (FI) is <30. Adding 0.5% micronized silica reduces adhesion by 40%, increasing FI to 45.
2. Pharmaceutical Powder (Paracetamol)
Original adhesiveness results in a repose angle of 52°; adding 1% magnesium stearate lowers it to 38°, improving flowability from “very poor” to “good.
3. PVC Dry Blend
When CaCO₃ content exceeds 15%, interparticle porosity drops below 0.35, and hopper arching probability exceeds 60%.
Industrial Strategies to Address Increased Adhesiveness
1. Surface Modification Technologies
Mechanical polishing: Using a honeycomb mill to polish the surface of cross-linked polyethylene (XLPE) powder reduces surface roughness (Ra) from 1.2 μm to 0.8 μm and lowers adhesion by 30%.
Chemical coating: After magnesium oxide powder is treated with stearic acid, the contact angle increases from 30° to 110°, and cohesion decreases by 45%.
2. Additive Control
3. Process Parameter Optimization
Two-stage granulation: Pre-press fine adhesive powders into 1–2 mm granules, then re-granulate into 3–5 mm particles, reducing contact points by 80%.
Gradient drying: For moisture-sensitive powders, adopt staged drying at 40°C → 60°C → 80°C. Moisture content drops from 3% to 0.5%, and adhesion decreases by 70%.
V. Monitoring and Early Warning Methods for Adhesiveness
1. Online Detection Technologies
Laser particle size–adhesion analyzer: Monitors particle size distribution and adhesion changes in real time, dynamically adjusting flow aid dosage.
Thermogravimetric–FTIR (TG-FTIR): Analyzes whether increased adhesiveness is due to surface-adsorbed impurities (e.g., CPE pyrolysis products in PVC systems).
2. Flowability Alert Indicators
Critical Adhesion Threshold: Alarm triggered when adhesion force >1.5 mN/m (for nano powders).
Dynamic Bulk Density (Dρb): Flowability risk identified when Dρb < 1.6 g/cm³.
Conclusion
Increased adhesiveness significantly reduces powder flowability by altering interparticle force balance and microstructure. In industrial practice, it’s essential to address this through surface modification, additive regulation, and process optimization, while leveraging online monitoring technologies for dynamic adhesiveness management.