Industrial technology has led to micro-nano powders. They have unique volume and surface effects. These materials have very different properties. They are different from normal materials. They differ in optical, magnetic, acoustic, electrical, and mechanical ways. They play a crucial role in developing new materials. This technology has achieved unprecedented growth. It’s based on basic raw materials and is for making micro-nano powders. Jet mills use fast airflow. It makes materials to collide, hit, and shear. It hits them with impact components. They can produce fine particles with a narrow range of size. They also have clean, smooth, and regular shapes. They disperse well and are highly active. The powder is a nanometer in size. The crushing system operates in a closed way to cut dust pollution. It also keeps the crushed materials clean.
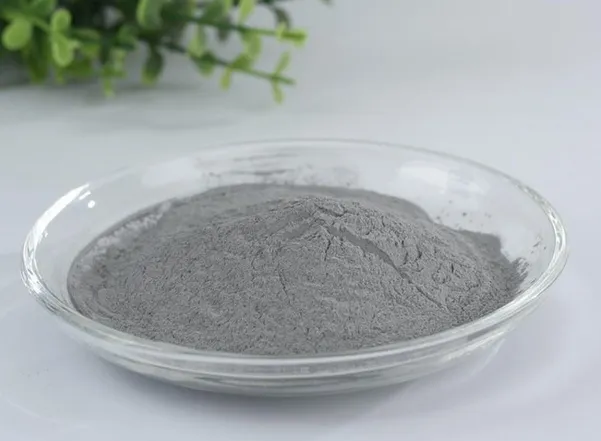
However, there are many types of airflow pulverizers. They have different working principles and crushing effects for materials. So, you must choose a suitable airflow pulverizer for each material. Now, jet mills have different structures and working methods. They can usually be divided into: collision, flat, fluidized bed, circulating tube, and target types. They can also be classified by material. It adopts methods such as low-temperature cryogenic airflow crushing and inert gas protection. These methods further optimize the crushing effect of the airflow grinder.
How to choose a jet mill with appropriate structure?
Collision airflow crusher
Opposing jet mills are also called opposing jet mills and reverse jet mills. The Majac type was developed by Donaldson Company in the United States. The Trost type was developed by Plastoiner Company. They are typical representatives. The equipment works. Two fast materials and fast airflow collide at a point on the line. This collision completes the crushing process. The crushed fine particles enter the external classifier with the airflow. They do so under the action of the classification rotor and pass through it. solid separation and become a product. The coarse particles stay at the edge of the classification chamber. They return to the crushing chamber for more crushing. This continues until they meet the size requirements and enter the external classifier.
The mill crushes by high-speed collisions between particles. The speed is the sum of the two airflows’ speeds. So, it achieves twice the result with half the effort. It has strong force, high speed, and uses energy well. It is highly efficient and makes fine particles. It has great advantages. It can crush materials that are hard, brittle, or sticky. At the same time, it uses particles to collide. This avoids wear on fixed impact parts from high-speed jets. It can also make purer micro-nano powders.
Flat jet pulverizer
The mill is flat. It is also known as a horizontal disc jet mill. Fluid Energy Company in the United States first developed it in 1934. It is the earliest and most widely used jet mill in industry. The main part of a flat airflow mill is a disc crushing chamber. Around it are 6 to 24 high-pressure nozzles for the working fluid. There are also Venturi tube feeders and product collectors. They are at a certain angle. The material to be crushed enters the venturi tube driven by the gas. The venturi tube has a special structure. It accelerates the material to supersonic speed. Then, the material enters the crushing chamber. The materials move in a circle in the crushing chamber. They are driven by a high-speed swirling flow. The particles and the inner wall of the machine collide and rub. They do so to be crushed. Centrifugal force throws coarse particles to the chamber’s wall. They circulate and crush there. Fine particles enter the cyclone separator. Centrifugal airflow collects them.
This equipment has the advantages of simple structure and convenient operation. It is easy to disassemble, clean and repair. It can also classify itself and is suitable for crushing brittle and soft materials. But, when the inner wall crushes harder materials, it will be damaged by violent collisions and friction. This also pollutes the product. So, it is not good for crushing hard particles. In addition, most of the energy of the flat jet mill is wasted work. Energy use during crushing will double. This happens as the product particles shrink. The materials are generally only processed to about D50=1μm.
Fluidized bed jet pulverizer
Fluidized bed airflow mill is currently the leading model of airflow pulverizer. It mainly combines the principle of counter-jet. It does this with the expanding gas jet flow in the fluidized bed. It is common in making chemicals, medicines, cosmetics, and advanced ceramics. It is also used for magnetic powder and other materials. . The equipment sprays air into the crushing area. It does this through several reverse nozzles when it’s working. The high-pressure airflow is in the crushing chamber. It speeds up the materials to be crushed. This makes them form a fluidized state. Then the fast materials collide and rub at the nozzle intersection. They are crushed. The airflow carries the crushed fine materials upward. It takes them to the ultra-fine classifier for classification. The cyclone separator collects the fine materials that meet the requirements. The coarse materials settle back to the crushing area under gravity. Then, crushing continues.
This pulverizer is special. Unlike others, it pulverizes materials as they expand in gas. The cavity’s temperature is kept at normal. It will not rise. It has good adaptability to heat-sensitive materials. It also combines the advantages of the collision-type airflow crusher. It uses the airflow to drive itself to collide and crush at high speed. It has little collision with the wall. It has many advantages. These include a narrow particle size. They also have high crushing efficiency and low energy use. They also have low product pollution and low accessories wear. , suitable for crushing materials with Mohs hardness level nine or above. However, it is a new type of crushing equipment. But, its cost is still high. Also, the material must be fluidized before the air jet can crush it. So, the mill usually requires the material to be crushed to be very fine. The requirements for materials with high density are more obvious.
How to choose crushing media?
Inert gas protection
Many powders in modern industry are flammable, explosive, and easily oxidizable. They must be ultrafine. To keep the crushing process safe, you must use inert gas. It is the airflow grinding medium to make ultrafine dry materials. Crush. When the system starts working, gas is filled in to drive away the air. This happens until the whole system reaches the oxygen detector’s limit. Then, the feeding device starts to crush the material.
Low temperature cryogenic air flow crushing process
Airflow crushing is common. It uses high-speed airflow (300~500m/s) or superheated steam (300~400℃) as the crushing medium. But, it is not good for some low melting point or heat-sensitive materials. The crushing uses refrigerant to cool the material. It cools the material to a brittle state. The brittle material undergoes many impacts through the crushing mechanism. It is in the crushing chamber and finally becomes fine particles. The crushed material is fine The density can reach micron level (600~2000 mesh).
The refrigerant usually needs to be selected based on the properties of the material. Liquid nitrogen is the most used refrigerant. Its lowest cooling temperature can reach minus 196 degrees. It is the preferred coolant for some materials that require rapid cooling and have a low embrittlement temperature. For materials that do not need high cooling and embrittlement temperatures, use compressed air. Or, use pre-cooled air from an air conditioner. Use them to exchange heat with the materials.
Now, the cold airflow crushing process is widely used. It crushes low-melting point, heat-sensitive materials. It is used to crush materials into an ultra-fine powder. It is used in industries such as polymers, chemicals, rare earths, biology, food, medicine, and health care products. It can also be used for flammable, explosive, and easily oxidized materials. Ultra-fine grinding of materials, but compared with inert gas, the cost is higher.