For ultrafine calcium carbonate, particle size, surface area, crystal form, and oil absorption are key technical indicators. These factors directly affect product performance. Other indicators are also important but generally easier to control in industrial production. However, for specialized applications, different uses demand different priorities. So, indicators should not be treated the same for all cases.
Particle Size and Specific Surface Area
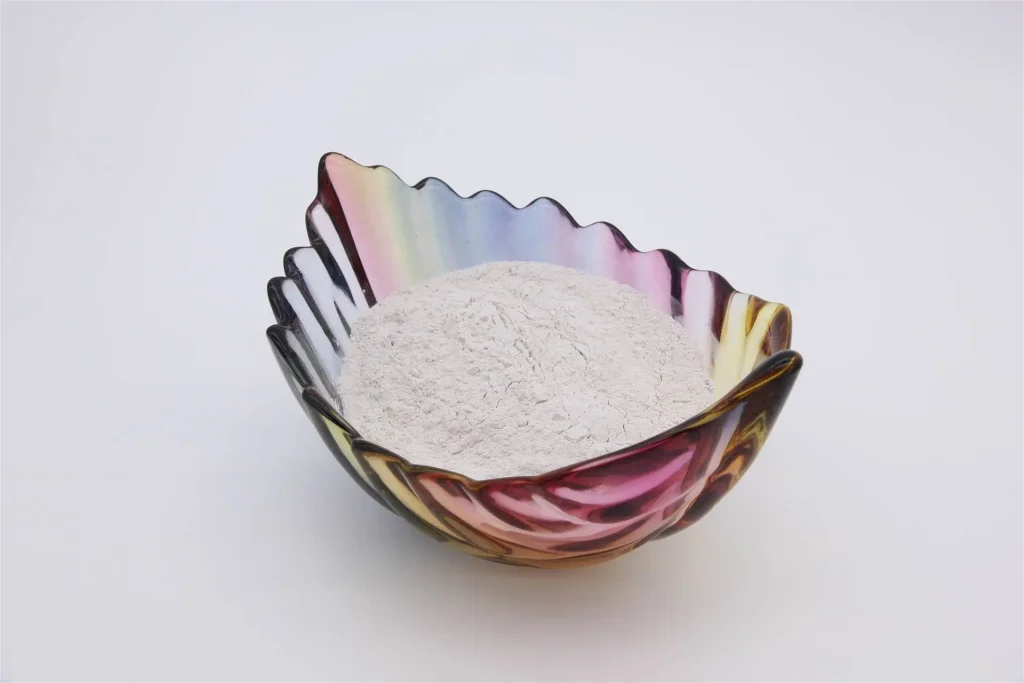
Achieving a primary particle size of 0.02–0.1 μm is a basic requirement for ultrafine calcium carbonate. Without this, it cannot be called “ultrafine.”
However, this is only half the task in making quality ultrafine calcium carbonate. If surface treatment and dispersion techniques are lacking, particles will agglomerate into larger secondary particles.
These agglomerates can reach hundreds of nanometers in size. Images from Transmission Electron Microscopy (TEM) only show primary particles.
Due to sample preparation, they do not reflect actual agglomerated particle sizes. Highly agglomerated products usually have lower BET surface area.
Therefore, combining TEM and BET surface area testing gives a more complete view of particle size, shape, and dispersion. There is a natural relationship between average particle size and surface area.
Some researchers use settling volume to estimate particle size. But settling volume is influenced by more than just size.
Factors like limestone quality, calcination, digestion, and carbonation conditions all affect the final size. Also, calcium carbonate has various crystal forms. Even within one form, shapes differ and are often irregular. So, crystal shape complicates settling volume results.
Even within one form, shapes differ and are often irregular. So, crystal shape complicates settling volume results. Using settling volume alone to judge particle size is not scientific, and often inaccurate. To reduce agglomeration, ultrafine calcium carbonate usually undergoes surface modification.
This not only enhances surface activity but also helps prevent particle clustering. For specialized products, the crystal form, particle size, surface treatment agent, and even processing techniques vary. Experience and technical know-how matter a lot during treatment. So, using a single standard to evaluate all types of ultrafine calcium carbonate is very difficult.
Crystal Form
Crystal form is also a crucial technical indicator for ultrafine calcium carbonate. Standard light calcium carbonate has a spindle shape.
Used in PVC, it creates stress and causes whitening in plastic films. Ultrafine calcium carbonate should vary in crystal form based on specific applications. For plastics, a simple structure, low packing volume, and low oil absorption are preferred. Cubic or spherical shapes are ideal.
Ultrafine calcium carbonate with 0.072μm particle size can enhance PVC plastic performance. It improves surface smoothness, gloss, and electrical insulation.
In soft cable compounds, even with double filler dosage, performance remains within national standards. In plastic films, it reduces whitening and increases low-temperature elongation.
However, in rigid plastics like doors and profiles, it increases impact strength. Notched impact resistance can reach 49.1 kJ/m². For rubber, chain-like shapes offer the best reinforcement.
Chain-shaped calcium carbonate forms by aligning many particles in one direction. This structure has spatial stability and disperses well in rubber.
During mixing, chains break, exposing active surfaces. These surfaces bond tightly with rubber chains, boosting reinforcement.
In rubber, reinforcement strength by shape is: chain > needle > sphere > cube. For ink, cubic shapes are best due to ink properties. In resin-based inks, ultrafine calcium carbonate should give gloss, transparency, and flowability.
Cubic crystals provide the best gloss performance. For paper coatings, precipitated calcium carbonate is typically used. It’s not ultrafine; size ranges from 0.1 to 1μm. Even so, crystal shape matters.
Paper coatings need good opacity, brightness, high viscosity, and ink absorption. Ideal crystal shapes include plate-like and cubic forms. In summary, ultrafine calcium carbonate must not only meet size requirements (0.02–0.1μm)
but also be tailored in crystal form based on usage to create market-ready products.
Oil Absorption Value
The oil absorption value of ultrafine calcium carbonate significantly impacts its application performance. This is especially true in plastics, coatings, and inks.
High oil absorption consumes more plasticizer in plastics.
In coatings and inks, it increases viscosity. Thus, oil absorption must remain low. Many factors affect oil absorption beyond physical properties of the material.
Among them, particle size is a major factor. Therefore, it must first ensure fine particle size and good dispersion.
It should also have a surface area matching its particle size.
Only then should reduction of oil absorption be considered. If dispersion is poor and particles agglomerate severely, the surface area is very low.
Even with low oil absorption, such material has little practical value.
Main Content
The main content of ultrafine calcium carbonate (CaO) should not be too strictly limited within a certain range. In most cases, ultrafine calcium carbonate serves as a functional filler, affecting physical rather than chemical properties.
Within a reasonable range, its CaO content can still meet performance needs. To produce calcium carbonate with various crystal forms, good dispersion, and high surface activity, additives like modifiers, dispersants, and surfactants are often introduced.
These intentionally added “impurities” generally do not harm product performance, and sometimes even improve it. However, they may reduce the measured content of CaO in the final product. Of course, harmful elements like iron and manganese must be tightly controlled.
Whether introduced from raw materials or during processing, they affect color and accelerate resin degradation and aging. These should be strictly avoided. Other impurities such as silicon, aluminum, and magnesium affect product whiteness and can hinder processing efficiency.
Thus, raw materials like limestone must be carefully selected and controlled. So, overly strict CaO content limits may restrict the development of specialized ultrafine calcium carbonate products. A balanced range is more practical. Summary The key direction for ultrafine calcium carbonate is specialization, series development, variety, and functionality.
It’s incorrect to assume that a 0.02–0.1μm particle size alone makes it suitable for all industries like rubber, plastic, ink, coatings, or paper. Applications demand specific requirements for particle size, crystal shape, surface area, oil absorption, and main content. Therefore, one universal standard cannot apply to all specialized ultrafine calcium carbonate products.
About Epic Powder Machinery
Epic Powder Machinery delivers cutting-edge solutions for ultrafine powder processing. We help clients achieve high-performance, customized results across plastics, rubber, coatings, and more.