Ada banyak metode untuk membentuk keramik khusus, seperti pengepresan kering, pengecoran selip, cetak injeksi, dan pengecoran gel. Pengepresan kering menawarkan keuntungan seperti kandungan pengikat rendah, sintering langsung tanpa pengeringan. Proses produksi sederhana, efisiensi tinggi, penyusutan green body kecil, dan produksi otomatis. Ini adalah metode yang paling umum digunakan dalam produksi keramik khusus.
Fokus penelitian ini adalah bagaimana menyiapkan green body dengan kepadatan tinggi dan gradien kepadatan yang seragam. Secara umum, faktor yang memengaruhi kepadatan green body selama pengepresan kering adalah proses pengepresan kering dan sifat bubuk.
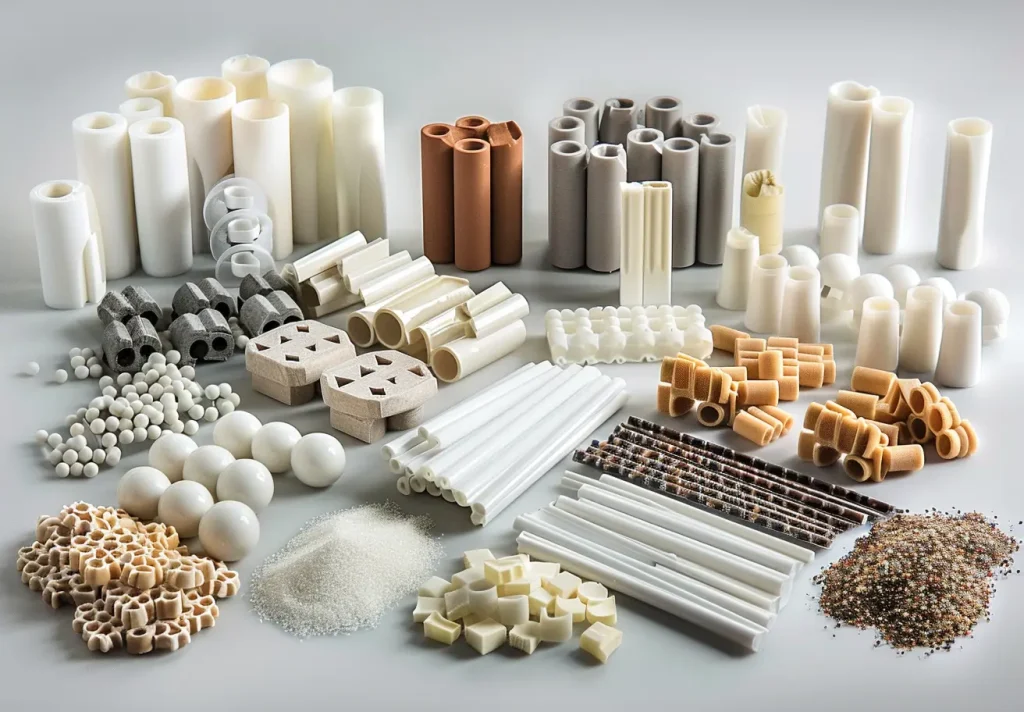
Pengaruh proses pengepresan kering
Proses pengepresan kering terutama mengacu pada metode penekanan, tekanan penekanan, kecepatan penekanan dan waktu penahanan.
Metode penekanan
Dalam pencetakan dengan pengepresan kering, metode pemberian tekanan meliputi pemberian tekanan searah dan pemberian tekanan dua arah. Metode pemberian tekanan yang berbeda akan menghasilkan transmisi dan distribusi tekanan yang berbeda dalam cetakan.
Menekan Tekanan
Secara umum, kepadatan green body meningkat seiring dengan peningkatan tekanan. Selama proses pengepresan keramik khusus, pengaruh tekanan terhadap kepadatan, kekuatan, dan porositas green body lebih signifikan daripada faktor lainnya. Tekanan juga memiliki dampak substansial terhadap kinerja green body setelah sintering.
Jika tekanan terlalu rendah, green body tidak dapat mencapai kepadatan maksimum, yang akan memengaruhi proses sintering. Sebaliknya, jika tekanan terlalu tinggi, cacat yang mirip dengan retaknya lapisan dapat muncul. Green body yang ideal hanya dapat dicapai jika tekanan berada pada tingkat optimal.
Kecepatan Tekanan dan Waktu Penahanan
Kecepatan penekanan dan waktu penahanan sangat memengaruhi kinerja benda kerja, karena keduanya terkait erat dengan penyaluran tekanan dan pengeluaran gas. Jika penekanan terlalu cepat dan waktu penahanan terlalu singkat, gas tidak akan mudah dikeluarkan. Demikian pula, jika tekanan tidak disalurkan ke kedalaman yang dibutuhkan, gaya eksternal akan dihilangkan sebelum pemadatan yang tepat, sehingga sulit untuk mencapai kualitas benda kerja yang diinginkan. Namun, jika kecepatan penekanan terlalu lambat dan waktu penahanan terlalu lama, efisiensi produksi akan menurun. Oleh karena itu, kecepatan penekanan dan waktu penahanan harus disesuaikan dengan ukuran, bentuk, dan ketebalan benda kerja.
Fokus utama penelitian adalah bagaimana menyiapkan green body dengan kepadatan tinggi dan gradien kepadatan yang seragam. Secara umum, faktor-faktor yang memengaruhi kepadatan green body selama pengepresan kering meliputi proses pengepresan kering dan sifat-sifat serbuk.
Pengaruh Proses Pengepresan Kering
Proses pengepresan kering terutama mengacu pada metode penekanan, tekanan penekanan, kecepatan penekanan, dan waktu penahanan.
Dalam pencetakan dengan pengepresan kering, metode pemberian tekanan meliputi pemberian tekanan searah dan dua arah. Metode pemberian tekanan yang berbeda menghasilkan transmisi dan distribusi tekanan yang berbeda dalam cetakan.
Sifat-sifat serbuk terutama mengacu pada ukuran partikel, gradasi partikel, kandungan pengikat dan air, serta fluiditas serbuk.
Ukuran Partikel dan Gradasi Partikel
Di bawah tekanan yang sama, kerapatan kompak hijau bubuk dengan ukuran partikel besar lebih tinggi, sedangkan kerapatan sintering bubuk dengan ukuran partikel lebih kecil lebih besar. Untuk bubuk dengan ukuran partikel yang sama, kerapatan kompak hijau dan kerapatan sintering meningkat dengan tekanan yang lebih tinggi. Oleh karena itu, meningkatkan ukuran partikel bermanfaat untuk meningkatkan kerapatan benda hijau.
Pengaruh Bahan Pengikat dan Kadar Air
Bila keramik khusus ditekan kering, bubuk keramik harus digranulasi terlebih dahulu untuk memenuhi persyaratan, kemudian bubuk yang digranulasi ditekan untuk membentuk green body. Sifat bubuk yang digranulasi—seperti bentuk, ukuran, distribusi ukuran, dan fluiditas pseudo-partikel—pada akhirnya akan memengaruhi kepadatan green body keramik. Kandungan pengikat juga memainkan peran penting dalam kinerja bubuk yang digranulasi. Selama pengepresan kering keramik khusus, pengikat terutama berfungsi sebagai agen pengikat, yang meningkatkan ukuran partikel pseudo-partikel dan meningkatkan kekuatan partikel.
Jika kandungan bahan pengikat terlalu tinggi selama proses granulasi, koefisien viskositas bubur meningkat, sehingga menghasilkan sudut atomisasi semprotan yang lebih kecil. Hal ini menyebabkan tetesan menggumpal setelah pengeringan dan granulasi, sehingga menghasilkan bubuk dengan distribusi ukuran partikel yang lebar dan fluiditas yang buruk. Akibatnya, menjadi sulit untuk mendapatkan badan hijau dengan kepadatan tinggi selama pengepresan kering. Sebaliknya, jika kandungan bahan pengikat terlalu rendah, kekuatan badan hijau akan gagal memenuhi persyaratan pemrosesan.
Kadar air juga berdampak signifikan pada kepadatan green body. Jika kadar air terlalu tinggi, penyusutan saat pengeringan akan cukup besar, sehingga sulit untuk mengendalikan ukuran green body. Selain itu, bubuk dapat menempel pada cetakan selama pencetakan, sehingga berdampak negatif pada kepadatan green body. Di sisi lain, jika kadar air terlalu rendah, hal itu akan menghambat kinerja penghancuran bubuk granulasi, sehingga lebih sulit untuk mendapatkan green body dengan kepadatan tinggi.
Fluiditas Serbuk
Fluiditas yang baik memastikan bahwa gesekan internal antar partikel minimal selama pengepresan kering keramik khusus, yang memungkinkan serbuk mengisi setiap sudut cetakan dengan lancar. Hal ini juga membantu meningkatkan kepadatan pengisian serbuk, yang memungkinkan pembentukan badan keramik yang padat dan seragam di bawah tekanan yang lebih rendah.
Memilih Bubuk Epik pengklasifikasi udara untuk solusi pemrosesan kaolin yang efisien, hemat energi, dan ramah lingkungan!
Hubungi kami untuk mempelajari lebih lanjut tentang produk kami!