The rubber industry, a cornerstone of modern manufacturing, is essential across various sectors including automobiles, construction, and electronics. Wax materials, as crucial additives in rubber production, play an irreplaceable role in enhancing the performance of rubber products. These waxes improve processing efficiency, surface smoothness, weather resistance, and anti-aging properties. This article introduces six common waxes used in the rubber industry. They’re microcrystalline wax, paraffin wax, protective wax, polyethylene wax, montan wax, and Fischer-Tropsch wax. Here is an analysis of their characteristics and applications to reveal the secret to high-performance rubber products.
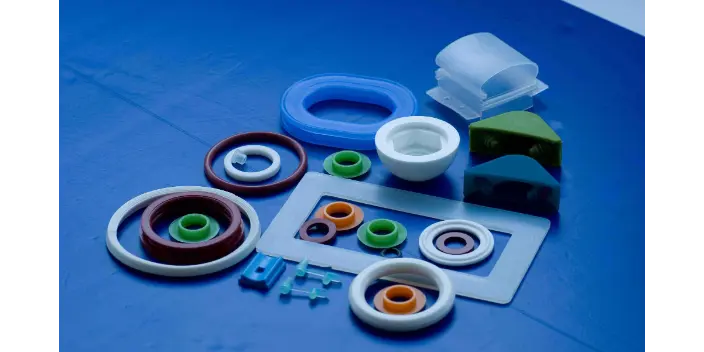
Microcrystalline Wax
- CAS No.: 63231-60-7
Microcrystalline wax is a type of paraffin wax with a fine crystalline structure. This wax is highly valued in the rubber industry for its unique properties. It features small crystal particles, a high melting point, and excellent flexibility and ductility. These attributes enhance processing performance, improve surface smoothness, and boost weather resistance in rubber formulations.
In rubber production, microcrystalline wax enhances the fluidity of the rubber, reducing surface defects during manufacturing. Additionally, it forms a protective film on the rubber surface to prevent oxidation and ozone damage, extending the product’s lifespan. Common applications include tires, seals, rubber pipes, and cables. For instance, in tire manufacturing, microcrystalline wax improves wear resistance, anti-aging properties, and surface smoothness, reducing friction and fuel consumption, thereby enhancing vehicle fuel efficiency.
Paraffin Wax
- CAS No.: 8002-74-2
Paraffin wax, a prevalent petroleum wax, is widely used in the rubber industry due to its moisture resistance and electrical insulation properties. It is primarily used to improve processing properties and act as a dispersant in rubber production. Its low cost and availability make it a popular choice.
Paraffin wax enhances rubber formulations by reducing viscosity, which improves processing fluidity, and by filling micropores in the rubber, reducing air entry and bubble formation, thus improving surface quality. However, it has poor anti-aging properties, so it is often combined with other anti-aging agents to ensure long-term stability. Paraffin wax is commonly used in products such as cable jackets, rubber seals, and construction rubber materials, maintaining a significant role in the industry despite its limitations.
Protective Wax
- Stearic Acid Wax
- CAS No.: 57-11-4
- Composite Wax
- CAS No.: This type of wax is usually a mixture and does not have a unified CAS number.
Protective wax, also known as anti-aging wax, is used in the rubber industry to prevent the degradation of rubber products caused by oxidation, ozone, and ultraviolet rays. Over time, these factors can lead to performance degradation, hardening, and cracking of rubber. Protective wax forms a protective film on the rubber surface, significantly extending its service life by mitigating these external factors.
There are various types of protective wax, including stearic acid wax, composite wax, and derivatives of microcrystalline wax. Each type offers different protective benefits and should be chosen based on specific application needs. For example, stearic acid wax is commonly used in tires, seals, and industrial rubber products. This is due to its effective protective properties and relatively low cost. Composite wax, created by blending multiple waxes, forms a superior protective film and is ideal for high-demand applications like aviation tires and high-performance seals.
The primary function of protective wax is to create a dense wax film on the rubber surface, blocking oxygen, ozone, and ultraviolet rays, thereby reducing the aging of rubber molecules. This addition not only extends the service life of rubber products but also enhances their wear and crack resistance, reducing overall loss during use.
Polyethylene Wax
CAS No.: 9002-88-4
Polyethylene wax is a synthetic wax produced through ethylene polymerization. It is known for its excellent lubricity and wear resistance and is widely utilized in the rubber industry. The primary role of polyethylene wax in rubber formulations is to enhance surface smoothness and reduce friction during processing, thus improving processing efficiency and product quality.
Polyethylene wax is used in applications such as tires, rubber pipes, seals, and industrial rubber products. Its lubricating properties significantly decrease friction between rubber and molds, lowering processing energy consumption and improving product surface quality. Additionally, polyethylene wax offers excellent weather resistance, ensuring stable performance of rubber products under harsh environmental conditions.
In practical applications, polyethylene wax is often combined with other waxes or additives to achieve optimal results. For example, in tire manufacturing, polyethylene wax is mixed with protective wax to enhance both surface smoothness and anti-aging performance. This combination not only extends the tire’s service life but also improves vehicle safety and fuel efficiency.
Montan Wax
- CAS No.: 8002-53-7
Montan wax is a natural wax derived from lignite ore through a complex refining process. It is characterized by a high melting point and excellent wear resistance, making it a valuable additive in the rubber industry for enhancing the wear resistance and anti-aging properties of rubber products.
Montan wax excels in thermal stability and oxidation resistance, enabling it to maintain rubber performance under high temperatures. It is particularly suitable for products that endure high temperatures and friction, such as automobile tires and industrial belts.
In the rubber industry, montan wax is typically used in formulations for high-performance products to improve wear resistance and extend service life. For instance, in automobile tire manufacturing, montan wax significantly enhances tire wear resistance, prolongs service life, and reduces heat buildup during high-speed driving, thereby improving vehicle safety. Montan wax is also employed in the production of seals and industrial rubber materials. It enhances wear resistance, anti-aging properties, and reduces performance degradation due to environmental factors.
Fischer-Tropsch Wax
- CAS No.: 68649-42-3
Fischer-Tropsch wax is a synthetic wax produced through the Fischer-Tropsch synthesis process, using coal or natural gas as primary raw materials. It has a high melting point and hardness, making it suitable as a processing aid and protective material in the rubber industry.
In the rubber industry, Fischer-Tropsch wax serves two main purposes: first, as a processing aid, it reduces the viscosity of rubber and improves its processing fluidity; second, as a protective material, it forms a dense wax film that enhances the anti-aging properties of rubber products.
The high hardness and melting point of Fischer-Tropsch wax make it particularly effective for high-performance rubber products. For example, aviation tires and high-wear-resistant seals. It improves wear resistance, enhances anti-aging properties, and extends the service life of these products.
Comprehensive Comparison of Different Waxes
The waxes used in the rubber industry each have unique properties and applications. Microcrystalline wax and protective wax are primarily used to enhance the anti-aging properties of rubber products. While paraffin wax is commonly used in ordinary rubber products due to its low cost and availability. Polyethylene wax and montan wax are favored in the manufacture of high-performance rubber products because of their excellent lubricity and wear resistance. Fischer-Tropsch wax is used in products that must withstand high temperatures and friction. That is due to its high hardness and melting point.
In practical production, rubber products often have multifaceted performance requirements, so different wax materials are typically combined to achieve optimal results. For example, in tire manufacturing, a blend of microcrystalline wax, protective wax, and polyethylene wax can improve both wear resistance and anti-aging properties, while also enhancing surface smoothness, leading to better fuel efficiency for vehicles.
In summary, the application of wax materials in the rubber industry not only improves product quality but also extends their service life and reduces production costs. Looking ahead, waxes will continue to play an irreplaceable role, supporting innovation and advancement in the rubber industry.