Da una prospettiva professionale sui processi di modifica delle particelle di polvere, le differenze fondamentali tra i metodi a umido e a secco possono essere analizzate in sei dimensioni chiave:
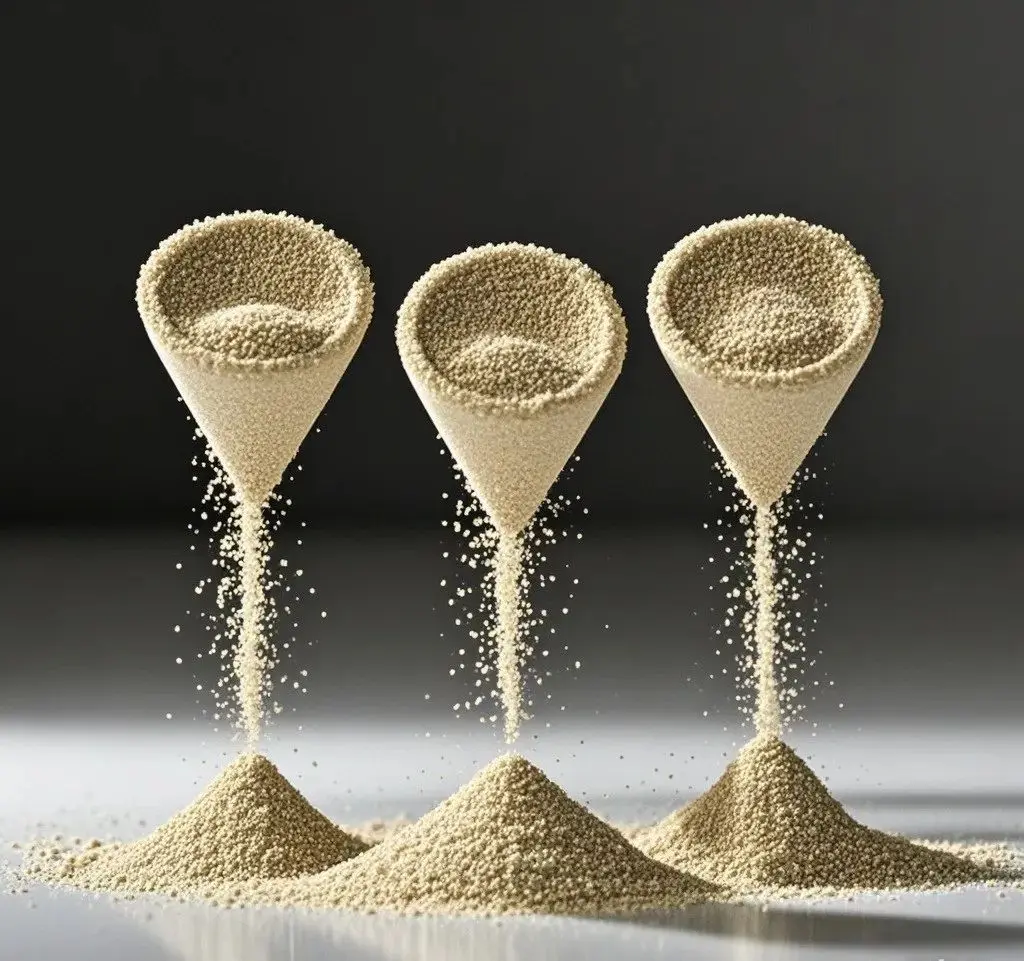
Adattabilità del processo
Metodo bagnato: Adatto per polveri ultrafini con dimensioni delle particelle
≤5μm (ad esempio, nano carbonato di calcio). L'ambiente liquido impedisce l'agglomerazione dura durante l'essiccazione. Ad esempio, nella produzione di pigmenti di mica perlescente che richiedono rivestimento in TiO₂, il metodo a umido garantisce l'uniformità del rivestimento entro ± 5nm.
Metodo a secco: adatto per polveri di dimensioni micrometriche con D50 ≥10μm (ad esempio, carbonato di calcio macinato convenzionale). I miscelatori ad alta velocità (300-1500 giri/min) consentono una rapida modifica, con una capacità di elaborazione di un'unica unità fino a 5 t/h.
Meccanismo di dispersione del modificatore
Metodo umido: utilizza solventi (ad esempio, acqua, etanolo) per formare un doppio strato di diffusione. Si ottiene una sospensione stabile quando il potenziale Zeta è controllato a ±30 mV. Ad esempio, gli agenti di accoppiamento silanici subiscono idrolisi e quindi condensano con gruppi idrossilici su superfici SiO₂, aumentando l'efficienza di legame a oltre 90%.
Metodo a secco: si basa sull'energia meccanica (forza di taglio >10⁴ s⁻¹) per rompere gli agglomerati di modificatori. Tuttavia, le velocità di rivestimento effettive in genere non superano 75%, richiedendo l'aggiunta di 0,5-1% di coadiuvanti disperdenti (ad esempio, acido stearico).
Attrezzature e consumo energetico
Metodo a umido: richiede bollitori di reazione con camicia (coefficiente di trasferimento di calore: 200-500 W/m²·K). Dopo la modifica, i materiali vengono sottoposti a disidratazione centrifuga (consumo energetico: 0,8 kWh/kg) e essiccazione a spruzzo (temperatura dell'aria in ingresso: 180-220℃).
Metodo a secco: utilizza macchine a modifica continua di tipo SLG, con consumo energetico specifico di circa 0,15 kWh/kg. L'investimento in attrezzature è ridotto di 40%, ma la concentrazione di polvere deve essere controllata al di sotto di 10 mg/m³.
Indicatori chiave di qualità
Metodo umido: indice di attivazione ≥98%, con valore di assorbimento dell'olio ridotto di 30% (ad esempio, il caolino modificato diminuisce da 80 g/100 g a 55 g/100 g).
Metodo a secco: deviazione dello spessore del rivestimento ±15 nm, resistività di volume regolabile entro 10¹²-10¹⁵ Ω·cm (ad esempio, idrossido di alluminio modificato per applicazioni su cavi).
Scenari applicativi
Metodo bagnato:
Le materie plastiche tecniche di alta qualità (ad esempio PA6 + fibra di vetro 30%) richiedono riempitivi modificati con D99 ≤3μm.
Rivestimento di Al₂O₃ per materiali catodici di batterie al litio (ad esempio, NCM811).
Metodo a secco:
Carbonato di calcio pesante modificato (1250 mesh) per tubi in PVC, con controllo dei costi a 800 RMB/tonnellata.
Caolino calcinato per rivestimenti architettonici, mantiene un livello di biancore superiore a 92%.
Economia di processo
Metodo umido: il costo complessivo è 25-40% più alto del metodo secco, con il recupero del solvente che rappresenta 18% di costi. Tuttavia, il premio del prodotto può raggiungere 30-50% (ad esempio, pigmenti perlescenti venduti a 80.000-150.000 RMB/tonnellata).
Metodo a secco: il consumo energetico per tonnellata è ridotto di 60%, rendendolo adatto alla modifica delle polveri su larga scala (produzione annuale >50.000 tonnellate), con un periodo di ammortamento dell'investimento ridotto a 2-3 anni.
Gli attuali progressi tecnologici indicano che il metodo umido si sta evolvendo verso un'elaborazione continua del micro-reattore (tempo di residenza <5 minuti), mentre il metodo secco sta facendo progressi nell'attrezzatura di modifica del mulino a vortice integrato (aumentando l'area superficiale specifica di 20%). Quando si seleziona un processo di modifica, le aziende devono valutare in modo completo il posizionamento del prodotto (produzione di fascia alta rispetto a produzione in serie), l'intensità dell'investimento di capitale (differenza CAPEX di 2-3 volte) e le normative ambientali (limiti di emissione di COV: 30 mg/m³).
Conclusione
Polvere epica Machinery è specializzata in soluzioni avanzate di modifica delle particelle di polvere, offrendo tecnologie di lavorazione sia a umido che a secco per soddisfare diverse esigenze industriali. Con competenze di base europee e decenni di esperienza, forniamo apparecchiature di modifica ad alta efficienza che garantiscono un rivestimento ottimale delle particelle, efficienza energetica e convenienza. Sia per materiali di fascia alta come catodi di batterie al litio o lavorazione di polvere in grandi quantità, Polvere epica Machinery fornisce soluzioni su misura per migliorare le prestazioni dei prodotti e soddisfare le mutevoli esigenze del mercato.