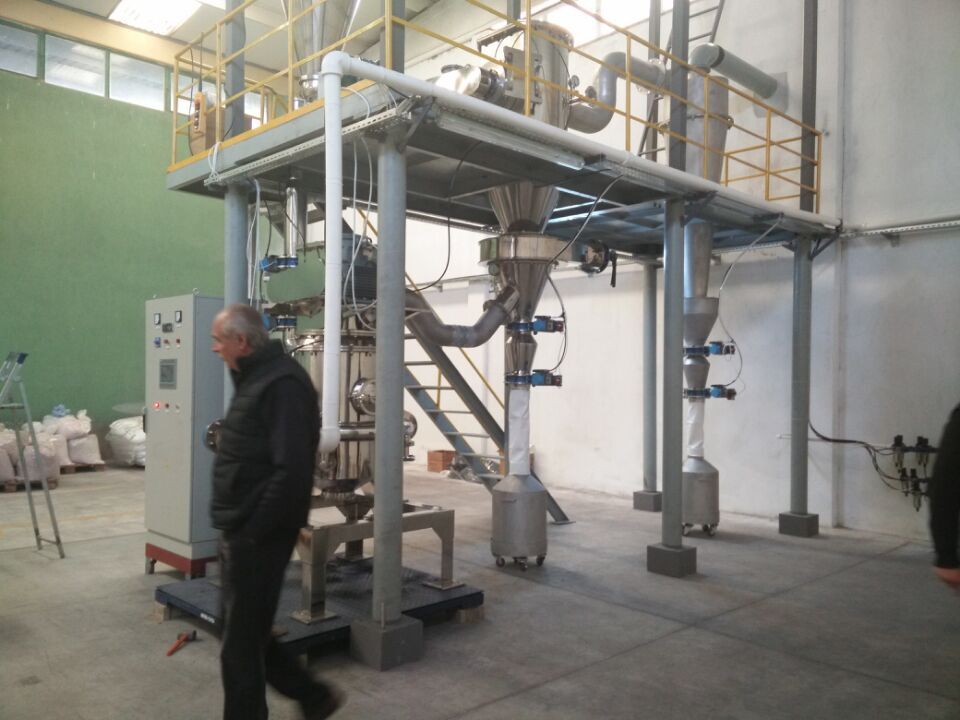
Un micronizzatore a getto è un dispositivo ad alta precisione progettato per ridurre le particelle in dimensioni estremamente fini. Utilizza getti ad alta velocità di aria compressa o gas per creare un vortice all'interno di una camera cilindrica o conica. Questo vortice fa sì che le particelle si scontrino ad alta velocità, rompendole in frammenti più piccoli. A differenza dei metodi di macinazione tradizionali, questo processo genera calore minimo, rendendolo ideale per materiali sensibili al calore. Settori come quello farmaceutico, alimentare e chimico si affidano a questa tecnologia per ottenere dimensioni delle particelle costanti. Un controllo preciso garantisce migliori prestazioni del prodotto, sia che si tratti di migliorare la biodisponibilità dei farmaci o di migliorare la consistenza dei prodotti alimentari.
Punti chiave
- I micronizzatori a getto utilizzano getti di gas rapidi per produrre particelle minuscole.
- Non hanno parti mobili, quindi rimangono pulitissimi.
- Ciò li rende ideali per l'industria farmaceutica e alimentare.
- La variazione della pressione e del flusso del gas determina quanto piccole diventano le particelle.
- Una pressione più elevata crea particelle ancora più piccole.
- I mulini a getto consentono di risparmiare energia e sono adatti a molti settori industriali.
- Vengono utilizzati nella produzione di medicinali, alimenti ed elettronica.
- Queste macchine creano particelle di dimensioni uniformi, migliorando la qualità del prodotto.
Come funziona un micronizzatore a getto?
Il ruolo del gas ad alta velocità
Come il gas accelera le particelle a velocità prossime al supersonico
In un micronizzatore a getto, aria compressa, gas o vapore spingono le particelle a velocità estremamente elevate. Questo processo si basa sul principio della dinamica dei fluidi, in cui i getti di gas creano un vortice all'interno della camera di macinazione. Mentre il gas scorre attraverso gli ugelli, accelera le particelle a velocità quasi supersoniche. L'assenza di parti mobili assicura che le particelle rimangano incontaminate durante il processo. Ciò rende il micronizzatore a getto ideale per applicazioni che richiedono purezza, come prodotti farmaceutici o prodotti chimici fini.
L'importanza della pressione e della portata del gas nel processo di macinazione
La pressione del gas e la portata svolgono un ruolo fondamentale nel determinare le prestazioni di un micronizzatore a getto. Pressioni del gas più elevate, come 7-15 bar per il vapore o 3,5-8,5 bar per l'aria, generano maggiore energia cinetica. Ciò si traduce in dimensioni delle particelle più fini. Al contrario, pressioni più basse producono particelle più grossolane. Anche la regolazione della portata influisce sull'efficienza di macinazione. Velocità di alimentazione più elevate riducono il tempo che le particelle trascorrono nella camera, determinando dimensioni delle particelle maggiori. Per ottenere i risultati migliori, è necessario bilanciare pressione del gas, portata e velocità di alimentazione.
Collisioni di particelle e riduzione delle dimensioni
Il meccanismo delle collisioni particella-particella per la micronizzazione
All'interno della camera di macinazione, le particelle si scontrano tra loro a causa dell' flusso di gas ad alta velocità. Queste collisioni si verificano a causa dei forti gradienti di velocità creati dal vortice. Le forze di impatto, compressione e taglio generate durante queste collisioni rompono le particelle in frammenti più piccoli. Questo metodo elimina la necessità di supporti di macinazione, riducendo i rischi di contaminazione.
Come le collisioni raggiungono dimensioni delle particelle micron o sub-micron senza mezzi di macinazione
Il micronizzatore a getto d'acqua raggiunge dimensioni di particelle ultrafini basandosi esclusivamente sulle collisioni tra particelle. Quando le particelle si scontrano ripetutamente, le loro dimensioni si riducono all'ordine dei micron o dei sub-micron. L'assenza di mezzi di macinazione assicura che il processo rimanga pulito e adatto a materiali sensibili. Questa caratteristica è particolarmente vantaggiosa per settori come quello alimentare e quello dell'elettronica, in cui purezza e precisione sono essenziali.
Separazione e raccolta delle particelle
Il ruolo delle forze centrifughe nella separazione delle particelle fini
Dopo che le particelle raggiungono la dimensione desiderata, entrano in gioco le forze centrifughe. Il vortice all'interno della camera crea una zona di classificazione in cui le particelle fini si separano da quelle più grandi. La forza centrifuga spinge le particelle più grossolane verso l'esterno, consentendo solo alle particelle più fini di muoversi verso il sistema di raccolta.
Come le particelle fini vengono raccolte in modo efficiente dopo la riduzione delle dimensioni
Una volta separate, le particelle fini escono dalla camera attraverso un classificatore o un'uscita. Il sistema di raccolta assicura che le particelle vengano raccolte in modo efficiente senza perdere materiale. Questo preciso processo di separazione consente al micronizzatore a getto di produrre polveri con dimensioni delle particelle uniformi, soddisfacendo i severi requisiti di vari settori industriali.
Tipi di mulini a getto
Mulini a getto a letto fluido
Progettazione e meccanismo di funzionamento dei mulini a getto a letto fluido
I mulini a getto a letto fluido funzionano utilizzando un design unico che incorpora un classificatore ad aria attivo. A differenza di altri mulini a getto, questo classificatore utilizza una ruota rotante con velocità regolabile per controllare la dimensione finale delle particelle. Il materiale di alimentazione entra nella camera di macinazione tramite una valvola rotante o un alimentatore a coclea. Flussi di gas ad alta velocità provenienti da ugelli opposti trascinano il materiale, causando collisioni di particelle che ne riducono le dimensioni. La forza centrifuga separa le particelle fini da quelle più grossolane. Le particelle fini escono tramite un separatore a ciclone e un collettore di polvere, mentre le particelle più grandi ritornano per un'ulteriore macinazione.
Caratteristiche principali, come la fresatura efficiente e l'idoneità per materiali sensibili al calore
Questo tipo di mulino a getto offre diversi vantaggi:
- È in grado di gestire materiali con durezza Mohs fino a 10, il che lo rende versatile.
- Elabora in modo efficiente i materiali sensibili al calore grazie alla minima generazione di calore.
- Riduce il consumo energetico e funziona con bassi livelli di rumorosità.
- Elabora in modo sicuro materiali infiammabili o esplosivi, come la polvere di alluminio, riducendo al minimo l'attrito meccanico.
Mulini a getto circolare
Progettazione e meccanismo di funzionamento dei mulini a getto circolare
I mulini a getto circolare presentano un design semplice della camera che migliora le prestazioni. La camera riduce al minimo l'effetto della forza centrifuga sulle particelle piccole, consentendo loro di muoversi in modo efficiente verso l'uscita centrale. Questo design migliora il processo di riduzione delle dimensioni delle particelle assicurando collisioni coerenti e una classificazione precisa.
Caratteristiche principali, tra cui design compatto e controllo preciso delle dimensioni delle particelle
I mulini a getto circolare sono compatti e facili da manutenere. Il loro design semplice consente una pulizia rapida, riducendo il rischio di contaminazione incrociata. Raggiungono dimensioni delle particelle molto fini con distribuzioni strette, rendendoli ideali per applicazioni che richiedono precisione. L'assenza di parti mobili nella camera di macinazione aumenta l'affidabilità ed elimina i rischi di contaminazione da guasti meccanici.
Applicazioni e vantaggi dei mulini a getto a spirale
I mulini a getto a spirale sono ampiamente utilizzati in vari settori industriali grazie alla loro versatilità ed efficienza.
Applicazione/Beneficio | Descrizione |
---|---|
Industria farmaceutica | Micronizza i principi attivi farmaceutici (API) per migliorarne la biodisponibilità. |
Industria alimentare | Riduce le dimensioni degli ingredienti alimentari migliorandone la consistenza, il sapore e la durata di conservazione. |
Industria chimica | Produce prodotti chimici e pigmenti raffinati con una distribuzione precisa delle dimensioni delle particelle. |
Industria cosmetica | Micronizza gli ingredienti cosmetici per una migliore consistenza e un'applicazione migliore. |
Industria aerospaziale | Produce materiali ad alte prestazioni con tolleranze ristrette. |
Industria elettronica | Crea polveri sottili per componenti elettronici per migliorarne la conduttività e l'affidabilità. |
Alta efficienza | Offre una riduzione superiore delle dimensioni delle particelle con sprechi minimi. |
Bassa contaminazione | Garantisce la purezza evitando l'uso di mezzi di macinazione. |
Efficienza energetica | Consuma meno energia rispetto ad altre tecniche di fresatura. |
Facile da pulire | Semplifica la pulizia e la manutenzione, riducendo i tempi di fermo. |
Versatilità | Gestisce un'ampia gamma di materiali, comprese sostanze dure e abrasive. |
Scalabilità | Si adatta facilmente sia alle operazioni su piccola che su larga scala. |
I mulini a getto a spirale sono particolarmente indicati per le industrie che richiedono dimensioni uniformi delle particelle e contaminazione minima.
Vantaggi e svantaggi dei micronizzatori a getto
Vantaggi
Ottenere dimensioni di particelle ultrafini con elevata precisione
I micronizzatori Jet Mill eccellono nella produzione di polveri ultrafini con dimensioni delle particelle che vanno da 1 a 10 micron. Questa precisione è essenziale per settori come quello farmaceutico, in cui una dimensione uniforme delle particelle migliora le prestazioni dei farmaci. La tecnologia consente inoltre di classificare le particelle entro un intervallo di dimensioni ristretto durante il processo di macinazione. Questa doppia funzionalità garantisce risultati coerenti su misura per le tue esigenze specifiche.
Bassa contaminazione grazie all'assenza di parti in movimento
A differenza dei metodi di macinazione tradizionali, i micronizzatori a getto non hanno parti mobili all'interno della camera di macinazione. Questa progettazione elimina l'usura meccanica e riduce il rischio di contaminazione. Puoi contare su questa caratteristica per mantenere la purezza dei tuoi materiali, il che è particolarmente importante in applicazioni come la lavorazione alimentare e la produzione di componenti elettronici.
Processo non termico adatto a materiali sensibili al calore
I micronizzatori Jet Mill funzionano senza generare calore significativo. Il flusso di gas ad alta velocità guida il processo di macinazione, mantenendo basse le temperature. Ciò rende la tecnologia ideale per la lavorazione di materiali sensibili al calore, come principi attivi farmaceutici o determinati polimeri. È possibile ottenere dimensioni di particelle fini senza compromettere l'integrità dei materiali.
Svantaggi
Elevato consumo energetico rispetto ad altri metodi di macinazione
I micronizzatori a getto richiedono gas compresso, che consuma una notevole quantità di energia. Il processo di compressione di aria o vapore ad alte pressioni richiede attrezzature e risorse avanzate. Ciò rende la tecnologia più adatta per prodotti di alto valore in cui precisione e purezza superano i costi energetici.
Costi operativi più elevati dovuti alla necessità di gas compresso
La dipendenza dal gas compresso non solo aumenta il consumo di energia, ma aumenta anche le spese operative. Potresti scoprire che mantenere la necessaria fornitura di gas e la pressione aumenta il costo complessivo dell'utilizzo di un micronizzatore a getto. Questo fattore può limitarne la praticità per prodotti a basso margine.
Limitato a tipi di materiali specifici e intervalli di dimensioni delle particelle
I micronizzatori a getto funzionano meglio con materiali che possono resistere a collisioni ad alta velocità senza degradarsi. Sono meno efficaci per sostanze appiccicose o altamente elastiche. Inoltre, sebbene eccellano nella produzione di particelle ultrafini, potrebbero non essere la scelta migliore per requisiti di dimensioni più grossolane. Dovresti valutare le proprietà del tuo materiale e i risultati desiderati prima di selezionare questa tecnologia.
Applicazioni industriali dei micronizzatori a getto
Prodotti farmaceutici
Produzione di polveri fini per formulazioni farmaceutiche
Puoi affidarti ai micronizzatori a getto per produrre polveri fini essenziali per applicazioni farmaceutiche. Questi dispositivi eccellono nella macinazione di principi attivi farmaceutici (API) in dimensioni precise, in genere nell'intervallo di 1-5 micron. Questo livello di micronizzazione aumenta la velocità di dissoluzione degli API, il che è fondamentale per migliorare la solubilità del farmaco. Il design chiuso dei mulini a getto assicura una lavorazione senza contaminazione, rendendoli ideali per formulazioni di farmaci sensibili.
Garantire una dimensione uniforme delle particelle per una migliore biodisponibilità
La dimensione uniforme delle particelle svolge un ruolo fondamentale nell'efficacia dei prodotti farmaceutici. Utilizzando un micronizzatore a getto, è possibile ottenere distribuzioni uniformi delle dimensioni delle particelle, che hanno un impatto diretto sui tassi di assorbimento degli API. Questa uniformità garantisce che ogni dose fornisca l'effetto terapeutico previsto. Semplifica inoltre i flussi di lavoro di produzione, con conseguenti farmaci di qualità superiore con biodisponibilità prevedibile.
Industria alimentare
Macinazione di spezie e aromi in polveri fini
I micronizzatori a getto sono ampiamente utilizzati nell'industria alimentare per macinare ingredienti come spezie, zucchero e farina in polveri ultrafini. Questo processo crea una distribuzione granulometrica stretta, essenziale per applicazioni che richiedono uniformità. Ad esempio, le spezie finemente macinate migliorano il rilascio dell'aroma e assicurano una distribuzione uniforme del sapore nei prodotti alimentari.
Additivi alimentari per la lavorazione per migliorare la consistenza e la consistenza
La riduzione delle dimensioni delle particelle migliora la consistenza e la consistenza dei prodotti alimentari. Le particelle più piccole si distribuiscono in modo più uniforme, migliorando il gusto e le caratteristiche sensoriali. Questa uniformità contribuisce anche a prolungare la durata di conservazione migliorando l'evaporazione dell'umidità e l'ossidazione dei grassi. Che tu stia elaborando additivi alimentari o nutraceutici, i micronizzatori a getto ti aiutano a ottenere risultati coerenti in tutti i lotti.
Industria chimica
Produzione di prodotti chimici raffinati, pigmenti e catalizzatori
Nell'industria chimica, il controllo delle dimensioni delle particelle è fondamentale per applicazioni come pigmenti e catalizzatori. I micronizzatori a getto consentono di produrre polveri fini con distribuzioni dimensionali precise. Ad esempio, i pigmenti di biossido di titanio raggiungono una riflettività ottimale quando le dimensioni delle particelle corrispondono alla lunghezza d'onda della luce visibile. Analogamente, i catalizzatori traggono vantaggio da dimensioni delle particelle più piccole, che ne migliorano l'attività e la selettività.
Applicazioni nei polimeri e nei materiali avanzati
I micronizzatori a getto sono indispensabili per produrre materiali avanzati e polimeri ad alte prestazioni. Questi dispositivi riducono al minimo la generazione di calore durante la macinazione, impedendo la degradazione termica dei materiali sensibili. Riducono inoltre la contaminazione, garantendo la qualità e le prestazioni del prodotto finale. Il controllo preciso delle dimensioni delle particelle consente di creare materiali con proprietà migliorate, come resistenza o conduttività migliorate.
Altri settori
Applicazioni in cosmetica per polveri fini
I micronizzatori Jet Mill svolgono un ruolo fondamentale nell'industria cosmetica producendo polveri ultrafini. È possibile utilizzare questa tecnologia per macinare materiali in particelle di dimensioni pari a 1-10 micron. Questo livello di precisione è essenziale per creare prodotti cosmetici lisci e di alta qualità. Ad esempio, minerali micronizzati come biossido di titanio e ossido di zinco migliorano la finitura e la sensazione del trucco, come fondotinta e ciprie. Questi minerali migliorano anche la capacità del prodotto di fondersi perfettamente con la pelle, fornendo un aspetto naturale e impeccabile.
Dagli anni '30, i produttori si sono affidati ai polverizzatori per soddisfare le richieste dei consumatori di polveri fini. Nel 1935, Coty ha introdotto le ciprie 'AirSpun', che utilizzavano mulini ad aria per ottenere la loro texture distintiva. Entro gli anni '40, i mulini a getto sono emersi come un'opzione superiore, offrendo dimensioni delle particelle ancora più fini. Oggi, scoprirai che i mulini a getto rimangono la scelta preferita dai produttori di cosmetici grazie alla loro capacità di produrre polveri con bassa contaminazione e una distribuzione ristretta delle dimensioni delle particelle. Ciò garantisce qualità e sicurezza costanti, in particolare per i prodotti per pelli sensibili.
I principali vantaggi dei mulini a getto nei cosmetici includono:
- Miglioramento della qualità del prodotto: Le polveri micronizzate creano una consistenza più liscia e una migliore coprenza.
- Bassa contaminazione: L'assenza di mezzi macinanti garantisce la purezza.
- Facilità d'uso: I mulini a getto sono robusti e adatti alla produzione su larga scala.
Utilizzo in elettronica per la produzione di materiali con dimensioni precise delle particelle
Nel settore dell'elettronica, la precisione è tutto. I micronizzatori a getto ti aiutano a creare materiali con dimensioni delle particelle esatte, il che è fondamentale per la produzione di componenti ad alte prestazioni. Ad esempio, le polveri fini sono essenziali per produrre paste conduttive, condensatori ceramici e semiconduttori avanzati. Questi materiali richiedono distribuzioni granulometriche strette per garantire una conduttività elettrica e un'affidabilità ottimali.
I mulini a getto eccellono nella lavorazione di materiali come silicio, ossido di alluminio e altre ceramiche avanzate. La natura non termica del processo impedisce danni da calore, preservando le proprietà del materiale. Ciò è particolarmente importante per l'elettronica, dove anche piccole impurità o incongruenze possono compromettere le prestazioni.
Apprezzerai anche la scalabilità dei mulini a getto. Che tu stia lavorando su piccola scala di ricerca o su larga scala di produzione, questi dispositivi si adattano alle tue esigenze. La loro capacità di produrre polveri uniformi assicura che i tuoi componenti elettronici soddisfino rigorosi standard di settore.
Le principali applicazioni nell'elettronica includono:
- Materiali conduttivi: Produzione di polveri fini per inchiostri e paste conduttive.
- Componenti in ceramica: Creazione di polveri uniformi per condensatori e isolanti.
- Semiconduttori: Ottenere dimensioni precise delle particelle per microchip avanzati.
I micronizzatori a getto garantiscono la precisione e l'affidabilità necessarie per rimanere competitivi nel mercato dell'elettronica in rapida evoluzione.
I micronizzatori a getto funzionano utilizzando getti di gas ad alta velocità per accelerare le particelle all'interno di una camera di macinazione. Le collisioni tra le particelle e le pareti della camera le scompongono in frammenti più piccoli. Questo processo, guidato dalla dinamica dei fluidi, assicura un'efficiente riduzione delle dimensioni, impedendo al contempo l'aggregazione delle particelle. Puoi beneficiare della capacità di questa tecnologia di produrre polveri fini con distribuzione uniforme delle dimensioni.
I principali vantaggi includono un controllo preciso delle dimensioni delle particelle, bassa contaminazione e idoneità per materiali sensibili al calore. Queste caratteristiche rendono i micronizzatori a getto essenziale per settori come quello farmaceutico, dove migliorano la solubilità dei farmaci, o la lavorazione degli alimenti, dove migliorano sapore e consistenza. La loro versatilità assicura risultati coerenti in diverse applicazioni.
Domande frequenti
Qual è lo scopo principale di un micronizzatore a getto?
Un micronizzatore a getto riduce le dimensioni delle particelle a un intervallo di micron o sub-micron. Utilizza getti di gas ad alta velocità per creare collisioni di particelle, rompendole in frammenti più piccoli. Questo processo assicura un controllo preciso delle dimensioni per applicazioni che richiedono polveri fini.
Quali materiali è possibile lavorare con un micronizzatore a getto?
È possibile elaborare un'ampia gamma di materiali, tra cui prodotti farmaceutici, ingredienti alimentari, pigmenti, polimeri e ceramiche avanzate. Tuttavia, funziona meglio con materiali asciutti, fragili o sensibili al calore che possono resistere a collisioni ad alta velocità.
Cosa differenzia i micronizzatori a getto dai mulini tradizionali?
I micronizzatori a getto utilizzano gas ad alta velocità anziché mezzi di macinazione. Ciò elimina i rischi di contaminazione e riduce al minimo la generazione di calore. I mulini tradizionali si basano sulla macinazione meccanica, che può introdurre impurità e calore, rendendoli inadatti per materiali sensibili.
Quali settori traggono i maggiori vantaggi dai micronizzatori a getto?
I settori che ne traggono i maggiori benefici sono quelli farmaceutici, alimentari, chimici, cosmetici ed elettronici. Questi settori richiedono un controllo preciso delle dimensioni delle particelle, una bassa contaminazione e la capacità di elaborare in modo efficiente materiali sensibili al calore.
Quali fattori influenzano le prestazioni di un micronizzatore a getto?
La pressione del gas, la portata e la velocità di alimentazione hanno un impatto diretto sulle prestazioni. Una pressione del gas più elevata produce particelle più fini, mentre velocità di alimentazione più elevate producono dimensioni più grossolane. Il bilanciamento di questi fattori garantisce risultati ottimali per la tua applicazione specifica.