近年、近代産業の発展に伴い、特に製薬・化学工業において超微粉砕技術がますます注目を集めており、原料の粉砕効果はその後の工程に直接影響を与えます。現在、エアフローミルは構造が簡単で分解が容易で粉砕効果が良いため、特にディスク(スパイラル)エアフローミルが超微粉砕機として主流となっています。多くの製薬企業や化学企業の支持を得ています。高純度・低粗度品の粉砕の代表的な装置としてご好評をいただいております。
気流式粉砕機には、プロセス システムの完全なセットが必要です。その役割を最大限に発揮し、損失をいかに減らすかということも重要な課題です。
気流粉砕機のろ過され乾燥した圧縮空気は、動物材料を互いにこすり合わせて粉砕効果を達成します。ディスク式気流粉砕機で消費される電気エネルギーのうち80%は、作業工程における圧縮空気の空気部分で消費されます。圧縮空気を最大限に活用することで、最大限の省エネを実現します。エアグラインダーを科学的に調整して理想的な作業条件で稼働させ、エアグラインダーの効率を向上させる方法は、多くのユーザーとメーカーが懸念している問題です。
送り速度の調整
送り速度は、粉砕室内での材料の衝突と粉砕時間を決定します。供給速度が遅いと、材料が粉砕室内に長く留まり、粒子の循環が多くなり、粉砕の程度がより適切になるため、粉砕の細かさが小さくなります。それでも遅すぎると、粉砕室内の粒子の数が少なすぎて衝突が少なくなり、望ましい効果が得られません。送りが速すぎると、粉砕室内の材料が多すぎるため、粉砕の細かさがより効果的になります。
実験により、均一で安定した供給により、粉砕室内のサイクロン流場の安定性が確保できることが証明されました。粉砕室内の気固比が理想的な状態になるように供給速度を調整し、原料粒子の有効衝突回数を最大限に高め、粉砕機の効率を向上させます。
グレーディング リングまたはグレーディング ホイールの速度の変更
ディスク型エアフローミルのグレーディングリングにはグレーディング装置が装備されています。調整は流動床(段階的)エアミルほど不便で簡単ではありません。材料が異なれば特性も異なり、粉砕効果の作動条件も異なります。まだ合意に達しておらず、それを実現するには多くの実験経験が必要です。
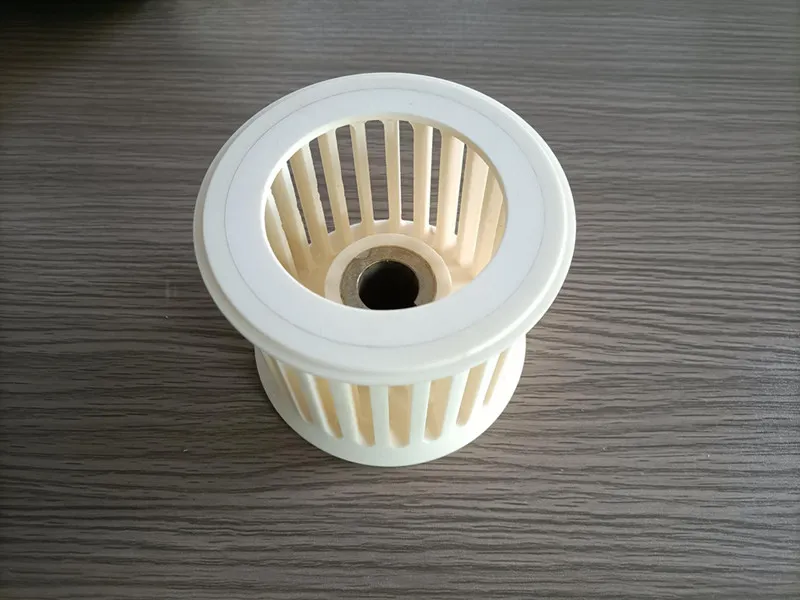
グレーディングホイールの回転により、粉砕室内のサイクロン流場が安定して材料が完全に粉砕され、粗い材料はグレーディングホイールを通過することができず、粉砕チャンバーに戻って粉砕を続けるだけです。粉砕。高速気流の作用により優れた破砕効率が得られるため、流動層気流破砕機にはいくつかの利点もあります。
適切なノズル設計
ノズルでのエネルギー損失を減らすには、ノズルの形状が鍵となります。異なる形状のノズルを通過する圧縮空気は、異なる速度の空気流を生成します。ノズルの設計と加工が不適切であると、粉砕空気流の速度低下やノズルの摩耗がさらに深刻になる可能性があります。ノズルが摩耗すると空気の流れがそらされ、空気の流れの一部が効果的に機能できなくなり、粉砕効率に影響を与える可能性があります。
その他の要因
他の要因も考慮する必要があります。たとえば、研削される材料の硬度が硬すぎると、グラインダーの研削チャンバーの摩耗がさらに激しくなります。このとき、セラミックコランダムなどの超硬質ライニングを交換する必要があります。これにより、粉砕チャンバー上の微細な材料の磨耗が大幅に軽減され、収集された材料の純度が向上します。
また、製薬・化学業界では、吸湿性や静電気など壁に付着しやすい素材にさらされることがよくあります。粉砕室や吐出口、受け器などに材料が付着し、工程全体の進行に影響を及ぼします。次に、破砕チャンバー内の特殊な固着防止ライニングを交換し、レシーバーに固着防止コーティングとライニングをスプレーまたはライニングする必要があります。配管の長さと材料の接触面積を最小限に抑え、材料の回収率を向上させます。静電気を含む材料を取り扱う場合には、効果的な静電気防止装置も必要です。
慎重な調整とメンテナンスの後、気流破砕機の可能性を探り、機械をより効率的に使用して粒子サイズ指数を確保することが、エネルギーの節約と消費量の削減にとって重要です。