Vooruitgang in calciumcarbonaatverwerkingstechnologieën heeft het mogelijk gemaakt om het te laten evolueren van een traditionele vulstof naar een modificator. Deze evolutie zorgt voor kostenverlagingen in producten en verbetert tegelijkertijd hun eigenschappen. Sommige daarvan zijn uniek voor calciumcarbonaat. Nieuwe microschuimtechnologie en holle calciumcarbonaat kunnen het gewicht verminderen. Ze maken lichtere calciumcarbonaatcomposieten. Ze zijn klaar voor industriële productie.
We kunnen met zekerheid voorspellen dat in de toekomst plastic calciumcarbonaat samengesteld materialen zullen het traditionele raamwerk van "twee reducties en één verbetering" opnieuw definiëren, namelijk het verlagen van kosten en dichtheid terwijl de prestaties worden verbeterd. Calciumcarbonaat zal van een simpele vulstof veranderen in een revolutionaire modificator.
Traditionele kunststof calciumcarbonaat composietmaterialen resulteren niet alleen in een vermindering van alle materiaaleigenschappen. In plaats daarvan kunnen ze ook verschillende eigenschappen verbeteren terwijl ze enkele prestatieverslechteringen veroorzaken. Dit artikel zal specifiek de positieve en negatieve effecten van calciumcarbonaat als modificator onderzoeken. Het begeleidt ons bij het leren van de ontwikkeling in calciumcarbonaatmodificatie van toekomstig onderzoek.
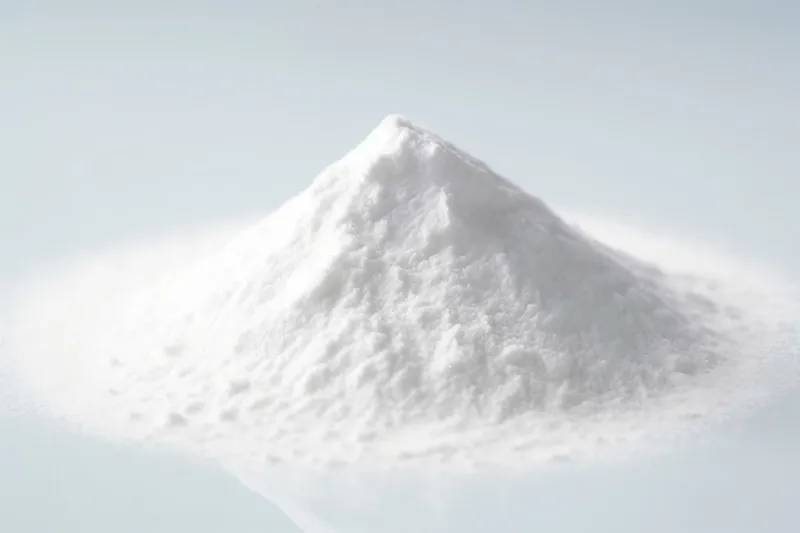
Positieve modificerende effecten van calciumcarbonaat
1 Milieuvoordelen van calciumcarbonaat
1.1 Behoud van aardoliebronnen
Berekende impact van calciumcarbonaat in plastic verpakkingen
Door 30% calciumcarbonaat in PE te gebruiken, kunnen 3 miljoen ton plastic zakken 900.000 ton op aardolie gebaseerde hars en 2,7 miljoen ton olie besparen.
1.2 Milieuvriendelijke prestaties
Het toevoegen van calciumcarbonaat aan plastic vuilniszakken die bestemd zijn voor verbranding kan de verbrandingsefficiëntie verbeteren en de verbrandingstijd aanzienlijk verkorten. Bij verbranding zet calciumcarbonaat uit in de plastic folie, waardoor er talloze kleine gaatjes ontstaan die het oppervlak dat beschikbaar is voor verbranding vergroten. Dit fenomeen versnelt het verbrandingsproces. Zo wordt de verbrandingstijd voor polyethyleen plastic folie met 30% calciumcarbonaat teruggebracht van 12 seconden (voor puur plastic) tot slechts 4 seconden.
Bovendien bevorderen calciumcarbonaat gevulde plastic films een completere verbranding. Dit minimaliseert zwarte rook van het lonteffect van calciumcarbonaat. De alkaliteit van calciumcarbonaat helpt zure gassen te absorberen. Dit vermindert giftige rook en het risico op zure regen.
In Japan bepalen de regels dat plastic vuilniszakken voor verbranding ten minste 30% calciumcarbonaat moeten bevatten. Naast de verbeterde verbrandingssnelheid genereren zakken gevuld met calciumcarbonaat minder hitte, produceren ze geen druppels of zwarte rook, verminderen ze secundaire vervuiling en zijn ze niet schadelijk voor verbrandingsovens.
2. Veelvoorkomende modificatie-effecten van calciumcarbonaat
2.1 Verbeterde stijfheid van composietmaterialen
Calciumcarbonaat verbetert de buigsterkte, buigmodulus, hardheid en slijtvastheid van composietmaterialen. In plastic films verbetert de verhoogde stijfheid de stijfheid aanzienlijk, wat zorgt voor platte krullen en algehele structurele integriteit.
2.2 Verbeterde dimensionale stabiliteit van composietmaterialen
Calciumcarbonaat draagt bij aan verbeterde dimensionale stabiliteit door krimp en kromtrekken te verminderen, de lineaire uitzettingscoëfficiënt te verlagen, kruip te minimaliseren en isotropie te bevorderen. De toevoeging van calciumcarbonaat aan composieten verbetert de dimensionale stabiliteit aanzienlijk.
2.3 Verbetering van de hittebestendigheid in composietmaterialen
Calciumcarbonaat verbetert de thermische stabiliteit van composietmaterialen door stoffen te absorberen die ontleding bevorderen. PBAT/calciumcarbonaatcomposieten vertonen bijvoorbeeld een aanzienlijk hogere thermische stabiliteit vergeleken met zuivere PBAT. Bovendien absorbeert het opnemen van licht calciumcarbonaat in PVC-producten effectief waterstofchloride dat tijdens de ontleding wordt geproduceerd, wat de thermische verwerkingsstabiliteit van PVC aanzienlijk verbetert.
2.4 Verbeterde scheurweerstand van films
Typische plastic films hebben vaak een hoge longitudinale sterkte maar een lage transversale sterkte, met name in materialen zoals PBS, PLA en PHA alifatische polyester films. De toevoeging van calciumcarbonaat kan de isotropie van deze composietmaterialen verbeteren, wat leidt tot een aanzienlijk verbeterde scheurweerstand.
3. Speciale aangepaste eigenschappen van calciumcarbonaat
3.1 Effecten op trek- en impacteigenschappen
De invloed van calciumcarbonaat op de treksterkte en slagvastheid van kunststoffolies is niet universeel; deze wordt beïnvloed door factoren zoals deeltjesgrootte en oppervlaktebehandeling.
Effect van deeltjesgrootte: Verschillende deeltjesgroottes van calciumcarbonaat leveren verschillende modificatie-effecten op plastics op, zoals geïllustreerd in Tabel 1. Over het algemeen worden deeltjesgroottes kleiner dan 1000 mesh gebruikt voor incrementele modificatie. Deeltjesgroottes tussen 1000 en 3000 mesh, met een toevoegingshoeveelheid kleiner dan 10%, kunnen enkele modificatie-effecten bereiken. Daarentegen vertoont calciumcarbonaat met deeltjesgroottes groter dan 5000 mesh, geclassificeerd als functioneel calciumcarbonaat, significante modificatie-effecten en kan het zowel de treksterkte als de slagvastheid verbeteren. Hoewel calciumcarbonaat op nanoschaal een fijnere deeltjesgrootte heeft, beperkt de huidige moeilijkheid bij dispersie de effectiviteit ervan, waardoor het beperkt blijft tot vergelijkbare modificatieresultaten als calciumcarbonaat van 8000 mesh.
Tabel 1: Effect van zwaar calciumcarbonaat met verschillende deeltjesgroottes op de prestaties van PP-composietmaterialen
Met koppelingsmiddel behandeld zwaar calciumcarbonaat (30%) maaswijdte | 2000 | 1250 | 800 | 500 |
Smeltstroomindex (g/10min) | 4.0 | 5.0 | 5.6 | 5.5 |
Treksterkte (MPa) | 19.3 | 18.4 | 18.7 | 18.1 |
Rek bij breuk (%) | 422 | 420 | 341 | 367 |
Buigsterkte (MPa) | 28 | 28.6 | 28.2 | 28.4 |
Buigmodulus (MPa) | 1287 | 1291 | 1303 | 1294 |
Izod-slagvastheid (J/m) | 113 | 89 | 86 | 78 |
Zoals weergegeven in Tabel 1, leiden fijnere deeltjesgroottes van calciumcarbonaat tot een verhoogde slagvastheid, treksterkte en rek bij breuk, terwijl de buigsterkte en buigmodulus relatief onveranderd blijven. De vloeibaarheid van het composietmateriaal neemt echter af met fijnere deeltjesgroottes.
Effect van oppervlaktebehandeling: Een juiste oppervlaktebehandeling van calciumcarbonaat met geschikte deeltjesgroottes kan de trek- en slagsterkte van composietmaterialen aanzienlijk verbeteren. Recente ontwikkelingen in de theorie van organische/anorganische composieten hebben calciumcarbonaat getransformeerd van een eenvoudige vulstof tot een nieuw functioneel vulmateriaal. Zo kan de gekerfde slagsterkte van een homopolymeer polypropyleen (PP)/calciumcarbonaat composiet meer dan verdubbelen in vergelijking met de basiskunststof.
3.2 Rookonderdrukking tijdens verbranding
Calciumcarbonaat vertoont uitstekende rookonderdrukkingscapaciteiten. Dit komt door zijn vermogen om te reageren met waterstofhalogeniden in rook, waarbij stabiel calciumchloride (CaCl₂) wordt gevormd. Daarom kan het worden gebruikt als rookonderdrukker in elk polymeer dat waterstofhalogeniden produceert tijdens verbranding, waaronder vinylchloride, chloorsulfonaatpolyethyleen en chloropreenrubber.
Omdat verbranding een heterogene vaste-gasreactie is die plaatsvindt op het oppervlak van vaste deeltjes, speelt de deeltjesgrootte van calciumcarbonaat een cruciale rol in de effectiviteit van rookonderdrukking. Fijnere deeltjes bezitten een aanzienlijk groter specifiek oppervlak, wat het rookonderdrukkingseffect versterkt.
3.3 Anti-aanhechtingsmiddel
Geblazen buisvormige films die calciumcarbonaat bevatten, vertonen uitstekende openingseigenschappen en zijn bestand tegen adhesie tijdens het krullen. In deze context functioneert calciumcarbonaat effectief als een anti-adhesiemiddel.
3.4 Verhoog de thermische geleidbaarheid
Door calciumcarbonaat toe te voegen wordt de thermische geleidbaarheid van de film verhoogd. De geblazen filmbel koelt sneller af. Dit verhoogt de productie en verhoogt de output van de extruder. Met 25% licht calciumcarbonaat in PVC-folie als voorbeeld, duurt het slechts 3,5 seconden om het tot 200°C te verwarmen. Zuiver PVC-folie duurt 10,8 seconden. De thermische geleidbaarheid nam 3 keer toe.
3.5 Verbeter de vloeibaarheid
Calciumcarbonaat kan de vloeibaarheid van het composietsysteem verbeteren, de smeltviscositeit en het extruderkoppel verlagen, de extruderoutput verhogen en de productie-efficiëntie verbeteren. Verschillende soorten calciumcarbonaat hebben verschillende effecten op de stroming. De volgorde van de vloeibaarheid van het specifieke composietmateriaal is groot calciet calciumcarbonaat > marmer calciumcarbonaat, dolomiet calciumcarbonaat > klein calciet calciumcarbonaat > licht calciumcarbonaat.
3.6 Kleuraanpassingsprestaties
Vervanging van sommige witte pigmenten: Calciumcarbonaat met een hoge witheid kan sommige witte pigmenten vervangen, zoals titaandioxide, waardoor het gehalte aan duur titaandioxide wordt bespaard. Grote calcietcalciumcarbonaat is de eerste keuze vanwege zijn hoge witheid en hoge dekkracht. De reden waarom calciumcarbonaat kan worden gebruikt als een wit pigment is voornamelijk omdat het een bepaalde dekkracht heeft. De dekkracht van een coating verwijst naar de minimale hoeveelheid verf die nodig is om de verf gelijkmatig op het oppervlak van een object aan te brengen, zodat de basiskleur niet meer zichtbaar is. Het wordt uitgedrukt in g/㎡.
De dekkracht van verschillende kleurstoffen in coatings wordt weergegeven in Tabel 2:
Tabel 2: Dekkingsvermogen van enkele anorganische en organische pigmenten
Pigmentnaam | Dekkingsvermogen (g/cm) |
Para rood (lichte tint) | 18.1-16.3 |
Para rood (donkere tint) | 17.1-15.0 |
Rood meer c | 23.8-18.8 |
Lithol rood (Ba meer) | 33.7-21.7 |
Lithol rood (Ca meer) | 49.0-33.7 |
Lithol robijn | 33.9 |
Yanke scharlaken meer | 88.5 |
Rhodamine Y (wolframaat neerslag) | 25.1 |
Rhodamine B (fosfowolframaat neerslag) | 16.1 |
Toluidine kastanje rood | 34.8-37.7 |
Lichtechte rode BL | 12.4 |
Titaandioxide | 18.4 |
(rutieltype, anataastype) | 19.5 |
Zinkoxide | 24.8 |
Bariumsulfaat | 30.6 |
Calciumcarbonaat | 31.4 |
Hansa geel G | 54.9 |
Hansa geel 10G | 58.8 |
Permanent oranje | 29.6 |
Malachietgroen | 5.4 |
Pigmentgroen B | 2.7 |
Malachietblauw (fosfowolframaatneerslag) | 7.7 |
Malachietblauw | 68.5 |
Methylviolet (fosfowolframaat neerslag) | 7.6 |
Methylviolet (tannine-precipitant) | 4.9 |
Zonnelicht snel violet | 10.2 |
Ftalocyanineblauw | 4.5 |
Zink-bariummortel (loodpoeder) | 23.6 |
Loodmortel (basisch loodsulfaat) | 26.9 |
Antimoontrioxide | 22.7 |
Talk | 32.2 |
De dekkracht van een materiaal is nauw verwant aan de brekingsindex. Over het algemeen resulteert een hogere brekingsindex in een grotere dekkracht en een intensere witte tint. De brekingsindex van verschillende witte materialen wordt gedetailleerd in Tabel 3.
Tabel 3: Brekingsindex van verschillende witte materialen
Witte materialen | Kleurstofindexnummer | Brekingsindex |
Titaandioxide (rutieltype) | Pigmentmortel 6 | 2.70 |
Titaniumpoeder (anataastype) | Pigmentmortel 6 | 2.55 |
Zirkoniumoxide | Pigmentmortel 12 | 2.40 |
Zinksulfide | 2.37 | |
Antimoontrioxide | Pigmentmortel 11 | 2.19 |
Zinkoxide | Pigmentmortel 4 | 2.00 |
Lithopone (zink-bariumpoeder) | Kleurmortel 21 | 2.10 |
Bariumsulfaat | Pigmentmortel 18 | 1.64 |
Calciumcarbonaat | Pigmentmortel 27 | 1.58 |
Talk | Kleurstofindexnummer | 1.54 |
Impact op kleuren De natuurlijke witte kleur van calciumcarbonaat beïnvloedt de mogelijkheid om felle kleuren te matchen, waardoor het lastig is om felle kleurencombinaties te bereiken. Bovendien kan het de match van speciale zwarttinten compliceren.
Impact op gekleurd licht Naast de natuurlijke witte kleur kan calciumcarbonaat verschillende kleuren licht vertonen, wat de zuiverheid van de kleur beïnvloedt. Kleurlicht verwijst naar de extra tinten die een object naast zijn hoofdkleur vertoont. Complementaire kleuren bevinden zich bijvoorbeeld aan de tegenovergestelde uiteinden van het kleurenspectrum; blauw wordt bijvoorbeeld aangevuld met geel. Door deze te mengen kan wit licht ontstaan, een effectieve methode om gekleurd licht te neutraliseren.
De basiskleur die calciumcarbonaat afgeeft, verschilt per oorsprong. Bijvoorbeeld:
- Calciumcarbonaat uit Sichuan heeft een blauwe basiskleur.
- Calciumcarbonaat uit Guangxi heeft een rode basiskleur.
- Calciumcarbonaat uit Jiangxi heeft ook een blauwe basiskleur.
Bij het matchen van kleuren moet het kleurlicht van calciumcarbonaat overeenkomen met de primaire kleurtoon. Bijvoorbeeld, calciumcarbonaat met een blauwe tint kan de kleurkracht van gele pigmenten tegengaan. Het wordt ook vaak gebruikt om geel kleurlicht in producten te neutraliseren.
Verbetering van astigmatisme in kunststofproducten: Hoewel de toevoeging van calciumcarbonaat de glans van kunststofproducten niet verbetert, vermindert het de glans effectief en zorgt het voor een matterend effect.
3.7 Verbetering van de ademende werking
Met calciumcarbonaat gevulde plastic films creëren kleine poriën tijdens het rekken, waardoor waterdamp erdoorheen kan stromen terwijl het infiltratie van vloeibaar water wordt voorkomen. Deze eigenschap maakt ze geschikt voor het produceren van ademende plastic producten. Voor optimale resultaten mag alleen calciumcarbonaat met een deeltjesgrootte van 3000 mesh of fijner worden gebruikt, met een smalle deeltjesgrootteverdeling.
3.8 Bevorderen van de degradatieprestaties van producten
Wanneer polyethyleen plastic zakken met calciumcarbonaat worden begraven, kan het calciumcarbonaat reageren met koolstofdioxide en water om in water oplosbaar calciumbicarbonaat (Ca(HCO₃)₂) te vormen, dat de film kan verlaten. Dit proces creëert kleine gaatjes in de film, waardoor het oppervlak dat in contact komt met lucht en micro-organismen toeneemt, waardoor de afbraak van het product wordt vergemakkelijkt.
3.9 Kernvormingsrol van calciumcarbonaat
Nanocalciumcarbonaat (CaCO₃) speelt een cruciale rol bij de kristallisatie van polypropyleen, doordat het de hoeveelheid β-kristallen verhoogt en daarmee de slagvastheid van polypropyleen verbetert.
3.10 Vermindering van waterabsorptie in PA-kunststoffen
De waterabsorptie van polyamide (PA)/calciumcarbonaatcomposieten is aanzienlijk lager dan die van pure PA-hars. Bijvoorbeeld, het opnemen van 25% calciumcarbonaat in PA6 kan de waterabsorptiesnelheid van het composietmateriaal met 56% verlagen.
3.11 Verbetering van oppervlakte-eigenschappen
Calciumcarbonaat kan de oppervlaktespanning van composietmaterialen verbeteren. Het heeft geweldige adsorptie-eigenschappen. Dit verbetert hun galvaniseer-, coating- en printkwaliteiten.
3.12 Effecten van calciumcarbonaat op schuimvorming
De invloed van calciumcarbonaat op de schuimprestaties van kunststoffen is complex en hangt af van zowel de deeltjesgrootte als de gebruikte hoeveelheid:
Calciumcarbonaat Grootte: Wanneer de deeltjesgrootte van calciumcarbonaat overeenkomt met het schuimmiddel, kan het fungeren als een nucleatiemiddel. Dit proces heeft een positieve invloed op schuimvorming. De ideale deeltjesgrootte is kleiner dan 5 μm en moet agglomeratie voorkomen. Als de deeltjesgrootte groter is dan 10 μm of te fijn is en agglomereert, kan dit een negatieve invloed hebben op schuimvorming. Het wordt aanbevolen om calciumcarbonaat van 3000 mesh (ongeveer 4 μm) te gebruiken om een grootte onder de 5 μm te garanderen zonder agglomeratie.
De mechanismen waarmee calciumcarbonaat schuimvorming bevordert, zijn onder meer:
Werkt als een nucleatiemiddel door schuimgas te absorberen en zo belkernen te creëren. Zo wordt het aantal poriën gecontroleerd en hun grootte verkleind.
Biedt stijfheid die de vervorming en mobiliteit van de smelt vertraagt, wat helpt om snelle poriënuitbreiding te voorkomen en fijnere poriëngroottes mogelijk maakt. Nano-calciumcarbonaat kan zelfs microporeuze schuimplastics genereren vanwege de kleine omvang van het nucleëringsmiddel.
Hoeveelheid toegevoegd calciumcarbonaat: De optimale vulhoeveelheid voor calciumcarbonaat om de schuimkwaliteit te verbeteren, varieert doorgaans van 10% tot 30%. Als er te weinig wordt toegevoegd, zijn er niet genoeg nucleatiepunten, wat leidt tot een lage schuimverhouding. Omgekeerd, als er te veel wordt gebruikt, terwijl er meer nucleatiepunten worden gecreëerd, kan de smeltsterkte buitensporig afnemen. Dit resulteert in talrijke gebroken bellen en een verminderde schuimverhouding.
Dispergeerbaarheid van calciumcarbonaat: Gelijkmatige dispersie van calciumcarbonaat is essentieel voor het bevorderen van de schuimkwaliteit. Gelijkmatig verdeeld calciumcarbonaat zorgt ervoor dat er geen agglomeratie optreedt. Als de deeltjesgrootte binnen 5 μm ligt, zal het effectief functioneren als een nucleatiemiddel zonder de schuimvorming negatief te beïnvloeden.
Watergehalte van calciumcarbonaat: Als het watergehalte van het anorganische poeder lager is dan 0,5%, heeft dit minimale invloed op de schuimvorming.
Overige eigenschappen: Calciumcarbonaat draagt ook bij aan een betere slijtvastheid en hardheid van composietmaterialen.
Negatieve modificaties van vulstoffen
1. Verhoogde dichtheid van composietmaterialen
De toevoeging van calciumcarbonaat aan hars resulteert in een snelle toename van de dichtheid van het composietmateriaal. Voor producten die worden verkocht op basis van gewicht, lengte of oppervlakte, kan deze toegenomen dichtheid enkele kostenvoordelen tenietdoen. De mate van gewichtstoename varieert tussen verschillende soorten calciumcarbonaat, met de volgende specifieke dichtheidsvolgorde:
Licht calciumcarbonaat < Groot calciet calciumcarbonaat < Marmer calciumcarbonaat < Dolomiet calciumcarbonaat < Klein calciet calciumcarbonaat.
Hoe de dichtheid van calciumcarbonaatcomposietkunststoffen te verminderen:
1.1 Productstretching voor gewichtsvermindering:
Uitrekken creëert vervormingsgaten tussen het plastic en calciumcarbonaat, waardoor de algehele dichtheid enigszins afneemt. Bijvoorbeeld, een uitgerekte polyethyleenfolie gevuld met 30% calciumcarbonaat heeft een dichtheid van 1,1 g/cm³, vergeleken met 1,2 g/cm³ voor de niet-uitgerekte versie. Deze techniek is toepasbaar op verschillende plastic producten zoals plat draad, geblazen folie, strapping tape en traanfolie.
1.2 Productmicro-schuim voor gewichtsvermindering:
Door het vocht dat door de filler wordt geabsorbeerd te gebruiken voor micro-foaming, kan de dichtheid aanzienlijk worden verlaagd zonder dat dit ten koste gaat van de prestaties. Zo kan ons 50% lichtgewicht calciumcarbonaatcomposietmateriaal een minimale dichtheid van 0,7 g/cm³ bereiken bij gebruik voor het produceren van films, wat een 45%-reductie vertegenwoordigt.
1.3 Holle vulling voor gewichtsvermindering:
Door gebruik te maken van eenvoudige en kosteneffectieve anorganische poederhollingtechnologie is de productie van holle calciumcarbonaatproducten mogelijk, wat de dichtheid aanzienlijk vermindert. De dichtheid van deze holle producten kan worden verlaagd tot ongeveer 0,7 g/cm³.
2. Vermindering van glans in composietmaterialen
De verwerkingsmethode en het type calciumcarbonaat beïnvloeden de oppervlakteglans van composietproducten. De volgorde van glans voor verschillende composietmaterialen is als volgt:
- Nat proces > Droog proces
- Licht calciumcarbonaat > Groot calciet calciumcarbonaat > Marmer calciumcarbonaat > Klein calciet calciumcarbonaat > Dolomiet calciumcarbonaat.
3. Vermindering van transparantie in composietmaterialen
Calciumcarbonaat heeft een brekingsindex die aanzienlijk verschilt van die van gangbare harsen zoals polyethyleen en polypropyleen. Als gevolg hiervan kunnen calciumcarbonaatvullers van conventionele grootte een negatieve invloed hebben op de transparantie van films. Alleen nano-calciumcarbonaat, met een grootte onder de 200 nanometer, kan de transparantie van het composiet behouden. Lichtgolven kunnen dergelijke kleine deeltjes effectief omzeilen.
4. Vermindering van rek bij breuk in composietmaterialen
De hoge stijfheid van calciumcarbonaat kan de oorspronkelijke ductiliteit van het composietmateriaal verminderen. Deze verhoogde stijfheid vermindert de mobiliteit van de macromoleculaire ketens, wat resulteert in een verminderde breukrek voor het eindproduct.
5. Afname van treksterkte en slagvastheid
In veel gevallen kan de toevoeging van calciumcarbonaat leiden tot een verminderde treksterkte en slagvastheid in het composietmateriaal. Dit geldt met name als de calciumcarbonaatdeeltjes te groot zijn of als de oppervlaktebehandeling van het calciumcarbonaat onvoldoende is. De meest opvallende afname is vaak te zien in de treksterkte.
6. Toegenomen stressverblekingsfenomeen
Wanneer u veel calciumcarbonaat aan de hars toevoegt, kan dit gaten en zilverstrepen veroorzaken wanneer het product wordt uitgerekt. Dit verergert de stress-whitening van de hars.
7. Versnelling van productveroudering
Alle anorganische poedermaterialen, waaronder calciumcarbonaat, kunnen de veroudering van composietmaterialen versnellen, wat leidt tot een vermindering van de levensduur en prestaties van de producten.
8. Verminderde hechtsterkte tussen materialen
Het gebruik van calciumcarbonaat kan de hechtsterkte van films verlagen, bijvoorbeeld door de warmteafdichtingssterkte te verminderen. Ook kan het de lassterkte van buizen verminderen.