ਵਿਸ਼ੇਸ਼ ਸਿਰੇਮਿਕਸ ਬਣਾਉਣ ਦੇ ਬਹੁਤ ਸਾਰੇ ਤਰੀਕੇ ਹਨ, ਜਿਵੇਂ ਕਿ ਸੁੱਕਾ ਦਬਾਉਣਾ, ਸਲਿੱਪ ਕਾਸਟਿੰਗ, ਇੰਜੈਕਸ਼ਨ ਮੋਲਡਿੰਗ, ਅਤੇ ਜੈੱਲ ਕਾਸਟਿੰਗ। ਡ੍ਰਾਈ ਪ੍ਰੈਸਿੰਗ ਘੱਟ ਬਾਈਂਡਰ ਸਮੱਗਰੀ, ਸੁੱਕੇ ਬਿਨਾਂ ਸਿੱਧੀ ਸਿੰਟਰਿੰਗ ਵਰਗੇ ਫਾਇਦੇ ਪੇਸ਼ ਕਰਦੀ ਹੈ। ਇੱਕ ਸਧਾਰਨ ਉਤਪਾਦਨ ਪ੍ਰਕਿਰਿਆ, ਉੱਚ ਕੁਸ਼ਲਤਾ, ਛੋਟਾ ਹਰਾ ਸਰੀਰ ਸੁੰਗੜਨਾ, ਅਤੇ ਸਵੈਚਾਲਿਤ ਉਤਪਾਦਨ। ਇਹ ਵਿਸ਼ੇਸ਼ ਸਿਰੇਮਿਕਸ ਦੇ ਉਤਪਾਦਨ ਵਿੱਚ ਸਭ ਤੋਂ ਵੱਧ ਵਰਤਿਆ ਜਾਣ ਵਾਲਾ ਤਰੀਕਾ ਹੈ।
ਉੱਚ ਘਣਤਾ ਅਤੇ ਇਕਸਾਰ ਘਣਤਾ ਗਰੇਡੀਐਂਟ ਵਾਲਾ ਹਰਾ ਸਰੀਰ ਕਿਵੇਂ ਤਿਆਰ ਕਰਨਾ ਹੈ, ਇਹ ਖੋਜ ਦਾ ਕੇਂਦਰ ਬਿੰਦੂ ਹੈ। ਆਮ ਤੌਰ 'ਤੇ, ਸੁੱਕੇ ਦਬਾਉਣ ਦੌਰਾਨ ਹਰੇ ਸਰੀਰ ਦੀ ਘਣਤਾ ਨੂੰ ਪ੍ਰਭਾਵਿਤ ਕਰਨ ਵਾਲੇ ਕਾਰਕ ਸੁੱਕੇ ਦਬਾਉਣ ਦੀ ਪ੍ਰਕਿਰਿਆ ਅਤੇ ਪਾਊਡਰ ਗੁਣ ਹਨ।
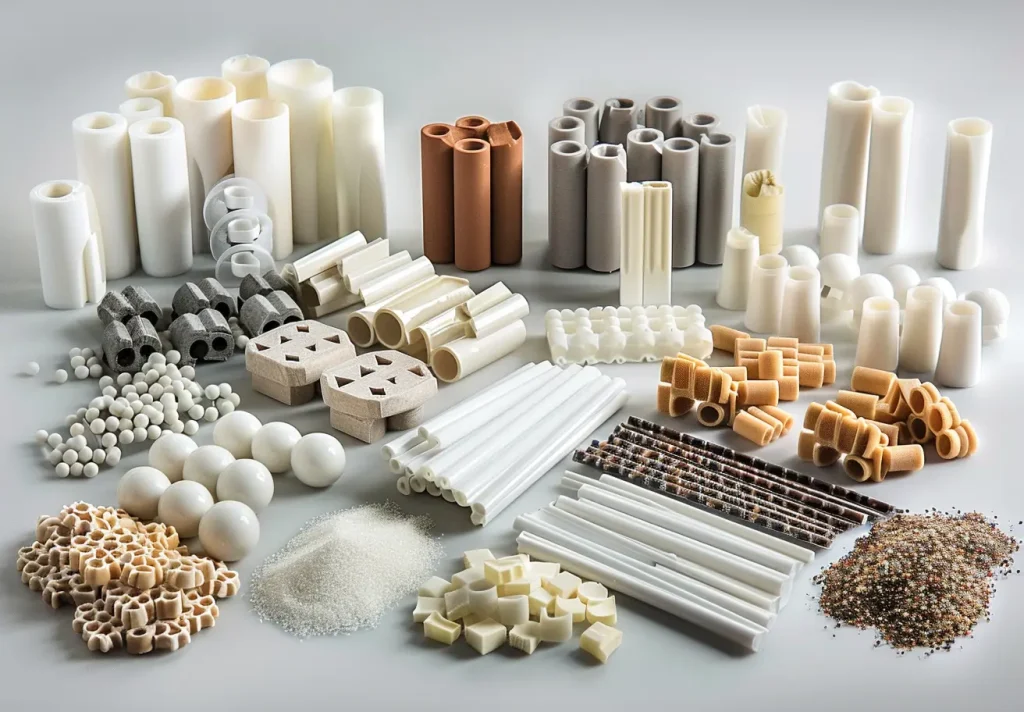
ਸੁੱਕੀ ਦਬਾਉਣ ਦੀ ਪ੍ਰਕਿਰਿਆ ਦਾ ਪ੍ਰਭਾਵ
ਸੁੱਕੀ ਦਬਾਉਣ ਦੀ ਪ੍ਰਕਿਰਿਆ ਮੁੱਖ ਤੌਰ 'ਤੇ ਦਬਾਅ ਵਿਧੀ, ਦਬਾਅ ਦਬਾਅ, ਦਬਾਅ ਦੀ ਗਤੀ ਅਤੇ ਹੋਲਡਿੰਗ ਸਮੇਂ ਨੂੰ ਦਰਸਾਉਂਦੀ ਹੈ।
ਦਬਾਅ ਵਿਧੀ
ਸੁੱਕੀ ਦਬਾਉਣ ਵਾਲੀ ਮੋਲਡਿੰਗ ਵਿੱਚ, ਦਬਾਅ ਬਣਾਉਣ ਦੇ ਤਰੀਕਿਆਂ ਵਿੱਚ ਇੱਕ-ਦਿਸ਼ਾਵੀ ਦਬਾਅ ਬਣਾਉਣ ਅਤੇ ਦੋ-ਦਿਸ਼ਾਵੀ ਦਬਾਅ ਬਣਾਉਣ ਸ਼ਾਮਲ ਹਨ। ਵੱਖ-ਵੱਖ ਦਬਾਅ ਬਣਾਉਣ ਦੇ ਤਰੀਕਿਆਂ ਦੇ ਨਤੀਜੇ ਵਜੋਂ ਮੋਲਡ ਵਿੱਚ ਦਬਾਅ ਦਾ ਵੱਖਰਾ ਸੰਚਾਰ ਅਤੇ ਵੰਡ ਹੋਵੇਗਾ।
ਦਬਾਉਣ ਦਾ ਦਬਾਅ
ਆਮ ਤੌਰ 'ਤੇ, ਦਬਾਅ ਵਧਣ ਨਾਲ ਹਰੇ ਸਰੀਰ ਦੀ ਘਣਤਾ ਵਧਦੀ ਹੈ। ਵਿਸ਼ੇਸ਼ ਸਿਰੇਮਿਕਸ ਦਬਾਉਣ ਦੀ ਪ੍ਰਕਿਰਿਆ ਦੌਰਾਨ, ਹਰੇ ਸਰੀਰ ਦੀ ਘਣਤਾ, ਤਾਕਤ ਅਤੇ ਪੋਰੋਸਿਟੀ 'ਤੇ ਦਬਾਅ ਦਾ ਪ੍ਰਭਾਵ ਹੋਰ ਕਾਰਕਾਂ ਨਾਲੋਂ ਵਧੇਰੇ ਮਹੱਤਵਪੂਰਨ ਹੁੰਦਾ ਹੈ। ਸਿੰਟਰਿੰਗ ਤੋਂ ਬਾਅਦ ਹਰੇ ਸਰੀਰ ਦੀ ਕਾਰਗੁਜ਼ਾਰੀ 'ਤੇ ਵੀ ਇਸਦਾ ਕਾਫ਼ੀ ਪ੍ਰਭਾਵ ਪੈਂਦਾ ਹੈ।
ਜੇਕਰ ਦਬਾਅ ਬਹੁਤ ਘੱਟ ਹੈ, ਤਾਂ ਗ੍ਰੀਨ ਬਾਡੀ ਵੱਧ ਤੋਂ ਵੱਧ ਘਣਤਾ ਪ੍ਰਾਪਤ ਨਹੀਂ ਕਰ ਸਕਦੀ, ਜੋ ਸਿੰਟਰਿੰਗ ਪ੍ਰਕਿਰਿਆ ਨੂੰ ਪ੍ਰਭਾਵਿਤ ਕਰਦੀ ਹੈ। ਦੂਜੇ ਪਾਸੇ, ਜੇਕਰ ਦਬਾਅ ਬਹੁਤ ਜ਼ਿਆਦਾ ਹੈ, ਤਾਂ ਪਰਤ ਦੇ ਕ੍ਰੈਕਿੰਗ ਵਰਗੇ ਨੁਕਸ ਦਿਖਾਈ ਦੇ ਸਕਦੇ ਹਨ। ਜਦੋਂ ਦਬਾਅ ਇੱਕ ਅਨੁਕੂਲ ਪੱਧਰ 'ਤੇ ਹੁੰਦਾ ਹੈ ਤਾਂ ਹੀ ਆਦਰਸ਼ ਗ੍ਰੀਨ ਬਾਡੀ ਪ੍ਰਾਪਤ ਕੀਤੀ ਜਾ ਸਕਦੀ ਹੈ।
ਦਬਾਅ ਦੀ ਗਤੀ ਅਤੇ ਹੋਲਡਿੰਗ ਸਮਾਂ
ਦਬਾਅ ਦੀ ਗਤੀ ਅਤੇ ਹੋਲਡਿੰਗ ਸਮਾਂ ਖਾਲੀ ਥਾਂ ਦੀ ਕਾਰਗੁਜ਼ਾਰੀ ਨੂੰ ਮਹੱਤਵਪੂਰਨ ਤੌਰ 'ਤੇ ਪ੍ਰਭਾਵਿਤ ਕਰਦੇ ਹਨ, ਕਿਉਂਕਿ ਇਹ ਦਬਾਅ ਦੇ ਸੰਚਾਰ ਅਤੇ ਗੈਸ ਦੇ ਡਿਸਚਾਰਜ ਨਾਲ ਨੇੜਿਓਂ ਸਬੰਧਤ ਹਨ। ਜੇਕਰ ਦਬਾਅ ਬਹੁਤ ਤੇਜ਼ ਹੈ ਅਤੇ ਹੋਲਡਿੰਗ ਸਮਾਂ ਬਹੁਤ ਛੋਟਾ ਹੈ, ਤਾਂ ਗੈਸ ਆਸਾਨੀ ਨਾਲ ਡਿਸਚਾਰਜ ਨਹੀਂ ਹੋਵੇਗੀ। ਇਸੇ ਤਰ੍ਹਾਂ, ਜਦੋਂ ਦਬਾਅ ਲੋੜੀਂਦੀ ਡੂੰਘਾਈ ਤੱਕ ਸੰਚਾਰਿਤ ਨਹੀਂ ਹੁੰਦਾ ਹੈ, ਤਾਂ ਬਾਹਰੀ ਬਲ ਨੂੰ ਸਹੀ ਘਣਤਾ ਤੋਂ ਪਹਿਲਾਂ ਹਟਾ ਦਿੱਤਾ ਜਾਵੇਗਾ, ਜਿਸ ਨਾਲ ਲੋੜੀਂਦੀ ਖਾਲੀ ਗੁਣਵੱਤਾ ਪ੍ਰਾਪਤ ਕਰਨਾ ਮੁਸ਼ਕਲ ਹੋ ਜਾਵੇਗਾ। ਹਾਲਾਂਕਿ, ਜੇਕਰ ਦਬਾਅ ਦੀ ਗਤੀ ਬਹੁਤ ਹੌਲੀ ਹੈ ਅਤੇ ਹੋਲਡਿੰਗ ਸਮਾਂ ਬਹੁਤ ਲੰਬਾ ਹੈ, ਤਾਂ ਉਤਪਾਦਨ ਕੁਸ਼ਲਤਾ ਘੱਟ ਜਾਵੇਗੀ। ਇਸ ਲਈ, ਦਬਾਅ ਦੀ ਗਤੀ ਅਤੇ ਹੋਲਡਿੰਗ ਸਮਾਂ ਖਾਲੀ ਥਾਂ ਦੇ ਆਕਾਰ, ਆਕਾਰ ਅਤੇ ਮੋਟਾਈ ਦੇ ਅਨੁਸਾਰ ਐਡਜਸਟ ਕੀਤਾ ਜਾਣਾ ਚਾਹੀਦਾ ਹੈ।
ਖੋਜ ਦਾ ਮੁੱਖ ਕੇਂਦਰ ਇਹ ਹੈ ਕਿ ਉੱਚ ਘਣਤਾ ਅਤੇ ਇੱਕ ਸਮਾਨ ਘਣਤਾ ਗਰੇਡੀਐਂਟ ਵਾਲਾ ਹਰਾ ਸਰੀਰ ਕਿਵੇਂ ਤਿਆਰ ਕੀਤਾ ਜਾਵੇ। ਆਮ ਤੌਰ 'ਤੇ, ਸੁੱਕੇ ਦਬਾਉਣ ਦੌਰਾਨ ਹਰੇ ਸਰੀਰ ਦੀ ਘਣਤਾ ਨੂੰ ਪ੍ਰਭਾਵਿਤ ਕਰਨ ਵਾਲੇ ਕਾਰਕਾਂ ਵਿੱਚ ਸੁੱਕੇ ਦਬਾਉਣ ਦੀ ਪ੍ਰਕਿਰਿਆ ਅਤੇ ਪਾਊਡਰ ਦੇ ਗੁਣ ਸ਼ਾਮਲ ਹਨ।
ਸੁੱਕੀ ਦਬਾਉਣ ਦੀ ਪ੍ਰਕਿਰਿਆ ਦਾ ਪ੍ਰਭਾਵ
ਸੁੱਕੀ ਦਬਾਉਣ ਦੀ ਪ੍ਰਕਿਰਿਆ ਮੁੱਖ ਤੌਰ 'ਤੇ ਦਬਾਅ ਵਿਧੀ, ਦਬਾਅ ਦਬਾਅ, ਦਬਾਅ ਦੀ ਗਤੀ, ਅਤੇ ਹੋਲਡਿੰਗ ਸਮੇਂ ਨੂੰ ਦਰਸਾਉਂਦੀ ਹੈ।
ਸੁੱਕੇ ਦਬਾਉਣ ਵਾਲੇ ਮੋਲਡਿੰਗ ਵਿੱਚ, ਦਬਾਅ ਬਣਾਉਣ ਦੇ ਤਰੀਕਿਆਂ ਵਿੱਚ ਇੱਕ-ਦਿਸ਼ਾਵੀ ਅਤੇ ਦੋ-ਦਿਸ਼ਾਵੀ ਦਬਾਅ ਬਣਾਉਣ ਸ਼ਾਮਲ ਹਨ। ਵੱਖ-ਵੱਖ ਦਬਾਅ ਬਣਾਉਣ ਦੇ ਤਰੀਕਿਆਂ ਦੇ ਨਤੀਜੇ ਵਜੋਂ ਮੋਲਡ ਵਿੱਚ ਦਬਾਅ ਦਾ ਵੱਖਰਾ ਸੰਚਾਰ ਅਤੇ ਵੰਡ ਹੁੰਦਾ ਹੈ।
ਪਾਊਡਰ ਦੇ ਗੁਣ ਮੁੱਖ ਤੌਰ 'ਤੇ ਕਣਾਂ ਦੇ ਆਕਾਰ, ਕਣਾਂ ਦੀ ਗਰੇਡਿੰਗ, ਬਾਈਂਡਰ ਅਤੇ ਪਾਣੀ ਦੀ ਮਾਤਰਾ, ਅਤੇ ਪਾਊਡਰ ਦੀ ਤਰਲਤਾ ਨੂੰ ਦਰਸਾਉਂਦੇ ਹਨ।
ਕਣ ਦਾ ਆਕਾਰ ਅਤੇ ਕਣ ਗਰੇਡਿੰਗ
ਉਸੇ ਦਬਾਅ ਹੇਠ, ਵੱਡੇ ਕਣ ਆਕਾਰ ਵਾਲੇ ਪਾਊਡਰ ਦੀ ਹਰੇ ਸੰਖੇਪ ਘਣਤਾ ਵੱਧ ਹੁੰਦੀ ਹੈ, ਜਦੋਂ ਕਿ ਛੋਟੇ ਕਣ ਆਕਾਰ ਵਾਲੇ ਪਾਊਡਰ ਦੀ ਸਿੰਟਰਿੰਗ ਘਣਤਾ ਵੱਧ ਹੁੰਦੀ ਹੈ। ਇੱਕੋ ਕਣ ਆਕਾਰ ਵਾਲੇ ਪਾਊਡਰ ਲਈ, ਹਰੇ ਸੰਖੇਪ ਘਣਤਾ ਅਤੇ ਸਿੰਟਰਿੰਗ ਘਣਤਾ ਦੋਵੇਂ ਉੱਚ ਦਬਾਅ ਨਾਲ ਵਧਦੇ ਹਨ। ਇਸ ਲਈ, ਕਣ ਦਾ ਆਕਾਰ ਵਧਾਉਣਾ ਹਰੇ ਸਰੀਰ ਦੀ ਘਣਤਾ ਨੂੰ ਬਿਹਤਰ ਬਣਾਉਣ ਲਈ ਲਾਭਦਾਇਕ ਹੈ।
ਬਾਈਂਡਰ ਅਤੇ ਪਾਣੀ ਦੀ ਮਾਤਰਾ ਦਾ ਪ੍ਰਭਾਵ
ਜਦੋਂ ਵਿਸ਼ੇਸ਼ ਵਸਰਾਵਿਕ ਪਦਾਰਥਾਂ ਨੂੰ ਸੁੱਕਾ ਦਬਾਇਆ ਜਾਂਦਾ ਹੈ, ਤਾਂ ਸਿਰੇਮਿਕ ਪਾਊਡਰ ਨੂੰ ਪਹਿਲਾਂ ਲੋੜਾਂ ਪੂਰੀਆਂ ਕਰਨ ਲਈ ਦਾਣੇਦਾਰ ਬਣਾਇਆ ਜਾਣਾ ਚਾਹੀਦਾ ਹੈ, ਅਤੇ ਫਿਰ ਦਾਣੇਦਾਰ ਪਾਊਡਰ ਨੂੰ ਹਰਾ ਸਰੀਰ ਬਣਾਉਣ ਲਈ ਦਬਾਇਆ ਜਾਂਦਾ ਹੈ। ਦਾਣੇਦਾਰ ਪਾਊਡਰ ਦੀਆਂ ਵਿਸ਼ੇਸ਼ਤਾਵਾਂ - ਜਿਵੇਂ ਕਿ ਸੂਡੋ-ਕਣਾਂ ਦੀ ਸ਼ਕਲ, ਆਕਾਰ, ਆਕਾਰ ਵੰਡ ਅਤੇ ਤਰਲਤਾ - ਅੰਤ ਵਿੱਚ ਸਿਰੇਮਿਕ ਹਰੇ ਸਰੀਰ ਦੀ ਘਣਤਾ ਨੂੰ ਪ੍ਰਭਾਵਤ ਕਰਨਗੀਆਂ। ਦਾਣੇਦਾਰ ਪਾਊਡਰ ਦੀ ਕਾਰਗੁਜ਼ਾਰੀ ਵਿੱਚ ਬਾਈਂਡਰ ਸਮੱਗਰੀ ਵੀ ਇੱਕ ਮਹੱਤਵਪੂਰਨ ਭੂਮਿਕਾ ਨਿਭਾਉਂਦੀ ਹੈ। ਵਿਸ਼ੇਸ਼ ਸਿਰੇਮਿਕ ਸੁੱਕਾ ਦਬਾਉਣ ਦੌਰਾਨ, ਬਾਈਂਡਰ ਮੁੱਖ ਤੌਰ 'ਤੇ ਇੱਕ ਬੰਧਨ ਏਜੰਟ ਵਜੋਂ ਕੰਮ ਕਰਦਾ ਹੈ, ਸੂਡੋ-ਕਣਾਂ ਦੇ ਕਣ ਦਾ ਆਕਾਰ ਵਧਾਉਂਦਾ ਹੈ ਅਤੇ ਕਣ ਦੀ ਤਾਕਤ ਨੂੰ ਵਧਾਉਂਦਾ ਹੈ।
ਜੇਕਰ ਦਾਣੇਦਾਰ ਪ੍ਰਕਿਰਿਆ ਦੌਰਾਨ ਬਾਈਂਡਰ ਸਮੱਗਰੀ ਬਹੁਤ ਜ਼ਿਆਦਾ ਹੁੰਦੀ ਹੈ, ਤਾਂ ਸਲਰੀ ਦਾ ਲੇਸਦਾਰ ਗੁਣਾਂਕ ਵਧ ਜਾਂਦਾ ਹੈ, ਜਿਸਦੇ ਨਤੀਜੇ ਵਜੋਂ ਸਪਰੇਅ ਐਟੋਮਾਈਜ਼ੇਸ਼ਨ ਐਂਗਲ ਛੋਟਾ ਹੁੰਦਾ ਹੈ। ਇਸ ਨਾਲ ਸੁੱਕਣ ਅਤੇ ਦਾਣੇਦਾਰ ਹੋਣ ਤੋਂ ਬਾਅਦ ਬੂੰਦਾਂ ਇਕੱਠੀਆਂ ਹੋ ਜਾਂਦੀਆਂ ਹਨ, ਜਿਸ ਨਾਲ ਇੱਕ ਵਿਸ਼ਾਲ ਕਣ ਆਕਾਰ ਦੀ ਵੰਡ ਅਤੇ ਮਾੜੀ ਤਰਲਤਾ ਵਾਲਾ ਪਾਊਡਰ ਬਣ ਜਾਂਦਾ ਹੈ। ਨਤੀਜੇ ਵਜੋਂ, ਸੁੱਕੇ ਦਬਾਉਣ ਦੌਰਾਨ ਉੱਚ-ਘਣਤਾ ਵਾਲਾ ਹਰਾ ਸਰੀਰ ਪ੍ਰਾਪਤ ਕਰਨਾ ਮੁਸ਼ਕਲ ਹੋ ਜਾਂਦਾ ਹੈ। ਇਸਦੇ ਉਲਟ, ਜੇਕਰ ਬਾਈਂਡਰ ਸਮੱਗਰੀ ਬਹੁਤ ਘੱਟ ਹੈ, ਤਾਂ ਹਰੇ ਸਰੀਰ ਦੀ ਤਾਕਤ ਪ੍ਰੋਸੈਸਿੰਗ ਜ਼ਰੂਰਤਾਂ ਨੂੰ ਪੂਰਾ ਕਰਨ ਵਿੱਚ ਅਸਫਲ ਰਹੇਗੀ।
ਪਾਣੀ ਦੀ ਮਾਤਰਾ ਹਰੇ ਸਰੀਰ ਦੀ ਘਣਤਾ ਨੂੰ ਵੀ ਕਾਫ਼ੀ ਪ੍ਰਭਾਵਿਤ ਕਰਦੀ ਹੈ। ਜੇਕਰ ਪਾਣੀ ਦੀ ਮਾਤਰਾ ਬਹੁਤ ਜ਼ਿਆਦਾ ਹੈ, ਤਾਂ ਸੁਕਾਉਣ ਦਾ ਸੁੰਗੜਨ ਕਾਫ਼ੀ ਹੋਵੇਗਾ, ਜਿਸ ਨਾਲ ਹਰੇ ਸਰੀਰ ਦੇ ਆਕਾਰ ਨੂੰ ਨਿਯੰਤਰਿਤ ਕਰਨਾ ਚੁਣੌਤੀਪੂਰਨ ਹੋ ਜਾਵੇਗਾ। ਇਸ ਤੋਂ ਇਲਾਵਾ, ਪਾਊਡਰ ਮੋਲਡਿੰਗ ਦੌਰਾਨ ਉੱਲੀ ਨਾਲ ਚਿਪਕ ਸਕਦਾ ਹੈ, ਜਿਸ ਨਾਲ ਹਰੇ ਸਰੀਰ ਦੀ ਘਣਤਾ 'ਤੇ ਨਕਾਰਾਤਮਕ ਪ੍ਰਭਾਵ ਪੈ ਸਕਦਾ ਹੈ। ਦੂਜੇ ਪਾਸੇ, ਜੇਕਰ ਪਾਣੀ ਦੀ ਮਾਤਰਾ ਬਹੁਤ ਘੱਟ ਹੈ, ਤਾਂ ਇਹ ਗ੍ਰੇਨੂਲੇਸ਼ਨ ਪਾਊਡਰ ਦੇ ਪਿੜਾਈ ਪ੍ਰਦਰਸ਼ਨ ਵਿੱਚ ਰੁਕਾਵਟ ਪਾਵੇਗਾ, ਜਿਸ ਨਾਲ ਉੱਚ-ਘਣਤਾ ਵਾਲਾ ਹਰਾ ਸਰੀਰ ਪ੍ਰਾਪਤ ਕਰਨਾ ਔਖਾ ਹੋ ਜਾਵੇਗਾ।
ਪਾਊਡਰ ਤਰਲਤਾ
ਚੰਗੀ ਤਰਲਤਾ ਇਹ ਯਕੀਨੀ ਬਣਾਉਂਦੀ ਹੈ ਕਿ ਵਿਸ਼ੇਸ਼ ਸਿਰੇਮਿਕਸ ਡ੍ਰਾਈ ਪ੍ਰੈਸਿੰਗ ਦੌਰਾਨ ਕਣਾਂ ਵਿਚਕਾਰ ਅੰਦਰੂਨੀ ਰਗੜ ਘੱਟ ਤੋਂ ਘੱਟ ਹੋਵੇ, ਜਿਸ ਨਾਲ ਪਾਊਡਰ ਮੋਲਡ ਦੇ ਹਰ ਕੋਨੇ ਨੂੰ ਸੁਚਾਰੂ ਢੰਗ ਨਾਲ ਭਰ ਸਕਦਾ ਹੈ। ਇਹ ਪਾਊਡਰ ਦੀ ਭਰਾਈ ਘਣਤਾ ਨੂੰ ਵਧਾਉਣ ਵਿੱਚ ਵੀ ਮਦਦ ਕਰਦਾ ਹੈ, ਜਿਸ ਨਾਲ ਘੱਟ ਦਬਾਅ ਹੇਠ ਇੱਕ ਸੰਘਣੀ ਅਤੇ ਇਕਸਾਰ ਸਿਰੇਮਿਕ ਬਾਡੀ ਬਣ ਜਾਂਦੀ ਹੈ।
ਚੁਣੋ ਐਪਿਕ ਪਾਊਡਰ ਕੁਸ਼ਲ, ਊਰਜਾ-ਬਚਤ, ਅਤੇ ਵਾਤਾਵਰਣ ਅਨੁਕੂਲ ਕਾਓਲਿਨ ਪ੍ਰੋਸੈਸਿੰਗ ਹੱਲਾਂ ਲਈ ਏਅਰ ਕਲਾਸੀਫਾਇਰ!
ਸਾਡੇ ਨਾਲ ਸੰਪਰਕ ਕਰੋ ਸਾਡੇ ਉਤਪਾਦਾਂ ਬਾਰੇ ਹੋਰ ਜਾਣਨ ਲਈ!