I. Definition and Source
If a polyethylene polymer cannot provide certain strength and toughness like resin, and cannot be processed as a single material into a product with specific functions, we can classify it as polyethylene wax.
Polyethylene wax is divided into many categories based on its source. There’re 3 types of them, such as polymerization method, thermal cracking method and by-products.
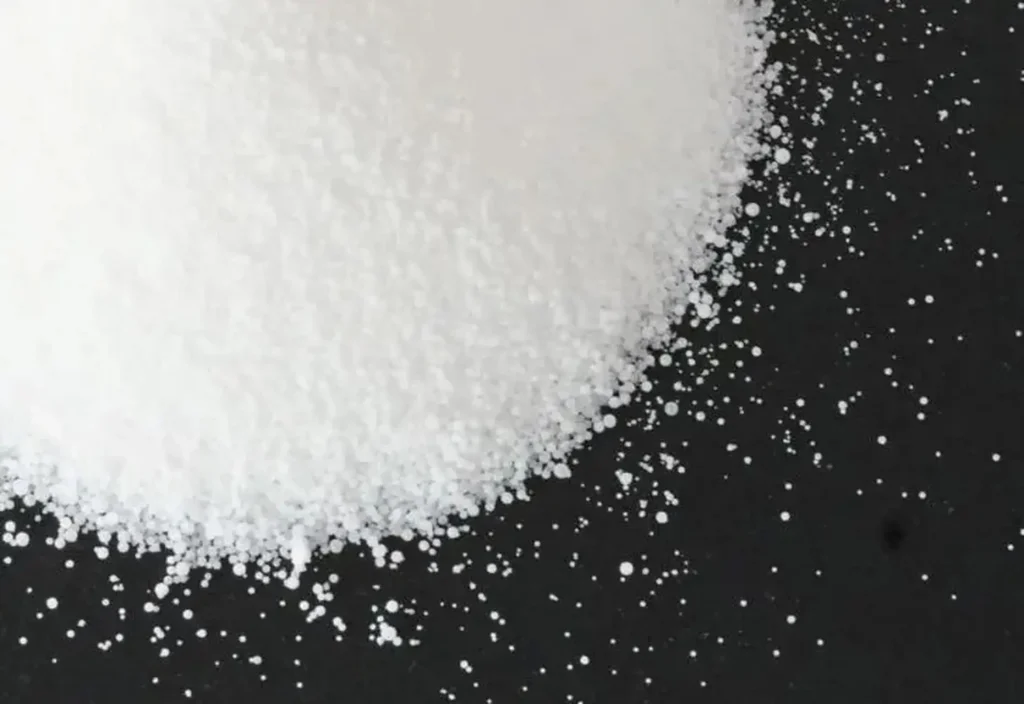
1) Polymerization polyethylene wax refers to polyethylene wax polymerized from ethylene monomers. It is categorized according to different polymerization methods. They’re free radical polymerization, Ziegler-Natta polymerization, metallocene catalytic polymerization, and proprietary polymerization technology.
2) Thermal cracking method involves using PE resin as a raw material. In this method the screw extrusion or reactors are employed for high-temperature cracking. Polyethylene resin or recycled polyethylene plastic is broken down into low relative molecular weight polyethylene wax. Compared with polyethylene wax produced by the polymerization method, the relative molecular weight distribution is broader. The odor from the low relative molecular weight can be difficult to eliminate completely. Additionally, it may be challenging to avoid the formation of black spots.
3) By-product polyethylene wax is a by-product of the synthesis of high-density polyethylene resin. It is an oligomer, usually a mixture of several oligomers with varying degrees of polymerization. The quality stability is difficult to control. If the distillation and cutting method is used, it can be divided into polyethylene waxes with different melting ranges.
II. Quality Indicators
Its molecular weight generally ranges from 1000 to 5000. The softening point is typically between 90 and 120°C. The density is about 0.92 to 0.95 g/cm³, as shown in the following table:
Item | Indicator | Influence |
Molecular weight | 1500-5000 | Generally speaking, the larger the molecular weight, the higher the melting point, and vice versa. |
Softening point | 90 0-120℃(varies with molecular weight) | If the softening point is too low, it is easy to vaporize and evaporate during high-temperature production. |
Hardness | Up to 3 – 8 | Affects the hardness of the final product. |
Viscosity | 10-600 (CPS140℃) | High viscosity will result in poor dispersion, but good glossiness, low viscosity will result in good dispersion and moderate glossiness. In addition, if the viscosity is too low, wax will easily precipitate, which is not conducive to the dispersion of fillers. If the viscosity is too high, it will affect the extrusion speed and production capacity. |
Needle penetration | 1-4 | The larger the needle penetration, the softer the grease, that is, the smaller the viscosity; vice versa, the harder the grease, that is, the greater the viscosity. |
III. Characteristics and Applications
Polyethylene wax exhibits excellent external lubrication and strong internal lubrication. It is well soluble in resins such as polyethylene, polyvinyl chloride, and polypropylene. Additionally, it has low viscosity, a high softening point, good hardness, non-toxicity, good thermal stability and low high-temperature volatility. It has excellent moisture resistance at room temperature, strong chemical resistance, and outstanding electrical properties.
In plastic processing, it serves as an efficient lubricant in the extrusion, calendering, and injection processing of polyolefins. This can improve processing efficiency, preventing the adhesion of films, pipes, and sheets, and enhancing the smoothness and gloss of finished products. Selecting the appropriate polyethylene wax in PVC processing can either delay or accelerate the gelation process. Once the homopolymer polyethylene wax is melted, it exists between the primary particles or nodules, reducing friction among them and thereby lowering the frictional heat of the melt, delaying the plasticization of PVC, and improving the thermal stability of PVC.
In the production of masterbatches, it plays a role in lubrication and dispersion, enhancing compatibility with various resins and improving production efficiency, gloss, and processing performance of products.
In coatings and inks, it contributes to matting, scratch resistance, wear resistance, anti-polishing, anti-imprinting, anti-adhesion, anti-precipitation, and thixotropy in solvent-based coatings. It also offers good lubricity and processability, as well as metal pigment positioning. Moreover, it can prevent the deposition of hard agglomerates such as silica, increase the storage stability of coatings, prevent metal scratches, and protect the storage stability of printed cans.