Powder coatings can not only reduce costs but also significantly improve the performance of coating products. For example, it can enhance the wear resistance, scratch resistance of the coating film. It can even improve the sagging of the paint during leveling. Additionally, it can boost the anti-corrosion properties of powder coatings.
When selecting materials, it is essential to consider factors such as density, dispersion performance, and distribution. Generally speaking, the higher the density, the lower the coverage of the powder coating. Large particles tend to have better dispersion than small particles. Chemical dyes should be used to avoid reactions with certain components of the powder formula, such as pigments. The color of the dye should be white.
Common materials used in powder coatings include calcium carbonate, sulfuric acid kinetics, talc powder, mica powder, kaolin, silica, and wollastonite. Today, we will learn about the roles of sulfuric acid kinetics, mica powder, and kaolin in powder coatings.
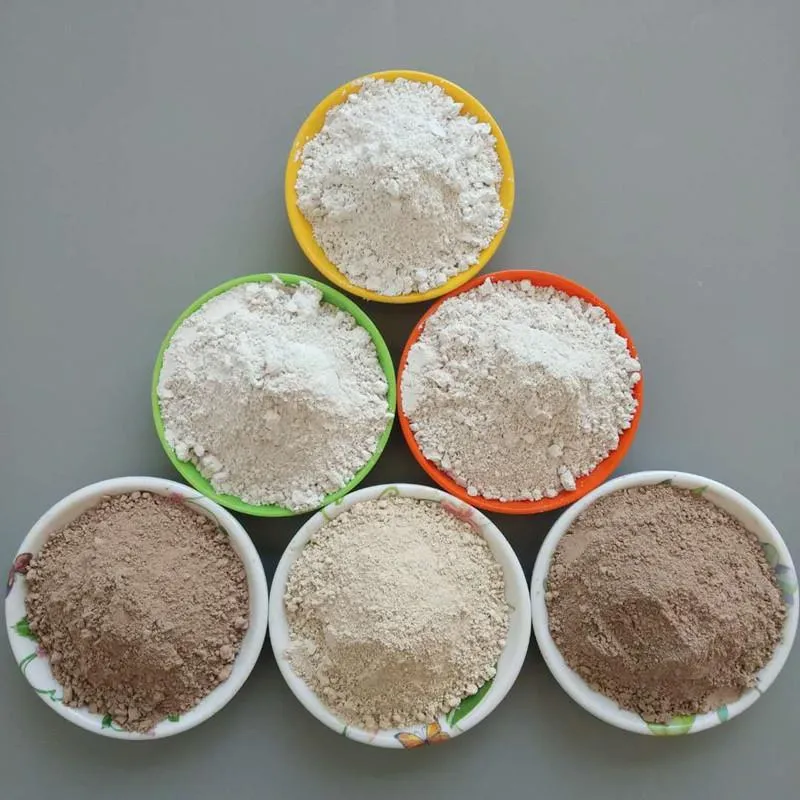
Application of Barium Sulfate in Powder Coatings
There are two types of barium sulfate used as paint extender pigments: natural and synthetic. The natural product is called barite powder, while the synthetic product is known as precipitated barium sulfate.
In powder coatings, precipitated barium sulfate can enhance the leveling and gloss retention of the coatings. It has good compatibility with all pigments. It helps the powder coating achieve the ideal film thickness during spraying, leading to a high powder coating rate.
Barite powder is primarily used in industrial primers and automotive intermediate coatings where high coating strength, high filling power, and high chemical inertness are required. It is also used in topcoats that need a higher gloss.
In latex paint, fine barite powder can act as a translucent white pigment due to its high refractive index (1.637). It can partially replace titanium dioxide in the paint. Ultrafine barium sulfate is ideal for powder coatings because of its large filling capacity, good brightness, excellent leveling, strong gloss retention, and compatibility with all colorants.
Application of Mica Powder in Powder Coatings
Mica powder consists of complex silicates with particles in the form of scales. It offers excellent heat resistance, as well as resistance to acids and alkalis. Mica powder affects the melt fluidity of powder coatings and is typically used in temperature-resistant and insulating coatings. It can also serve as a filler for texture powder.
Among the various types of mica, sericite has a chemical structure similar to kaolin. It combines many characteristics of both mica and clay minerals. When used in coatings, sericite can significantly improve the weather resistance, water resistance, adhesion, and strength of the coating film. It also enhances the appearance of the coating. Dye particles can easily enter the interlayers of sericite powder, which helps maintain long-lasting color without fading. Additionally, sericite powder has anti-algae and anti-mold properties. Therefore, sericite powder is an excellent multifunctional filler for coatings with a high cost-performance ratio.
Application of Kaolin in Powder Coatings
Kaolin in powder coatings can improve thixotropy and anti-settling properties. Calcined clay does not affect rheological properties but can provide a matte effect, increase opacity, and enhance whiteness, similar to talcum powder. Generally, kaolin has high water absorption and is not suitable for improving the thixotropy of coatings or preparing hydrophobic coatings. The particle size of kaolin products ranges from 0.2 to 1μm. Larger particle size kaolin has lower water absorption and better matting effect. In contrast, smaller particle size kaolin (less than 1μm) is suitable for semi-gloss and interior coatings.
Kaolin, also known as hydrated aluminum silicate, can be classified into calcined kaolin and water-washed kaolin based on processing methods. Generally, calcined kaolin has higher oil absorption, opacity, porosity, hardness, and whiteness compared to water-washed kaolin. However, it is also more expensive.
If you are interested in producing these three mineral powders, please contact Epic Powder customer service staff for related production machines.