Os avanços nas tecnologias de processamento de carbonato de cálcio permitiram que ele evoluísse de um enchimento tradicional para um modificador. Essa evolução permite reduções de custo em produtos, ao mesmo tempo em que melhora suas propriedades. Algumas delas são exclusivas do carbonato de cálcio. Novas tecnologias de microespuma e carbonato de cálcio oco podem reduzir o peso. Eles produzem compostos de carbonato de cálcio mais leves. Eles estão prontos para produção industrial.
Podemos prever com segurança que no futuro o carbonato de cálcio plástico composto os materiais redefinirão a estrutura tradicional de “duas reduções e uma melhoria” — ou seja, reduzir custos e densidade enquanto melhora o desempenho. O carbonato de cálcio passará de um mero enchimento para um modificador revolucionário.
Os materiais compostos tradicionais de carbonato de cálcio plástico não resultam somente em uma redução de todas as propriedades do material. Em vez disso, eles também podem melhorar vários atributos enquanto causam algumas degradações de desempenho. Este artigo explorará especificamente os efeitos positivos e negativos do carbonato de cálcio como um modificador. Ele nos orienta no aprendizado do desenvolvimento na modificação do carbonato de cálcio de pesquisas futuras.
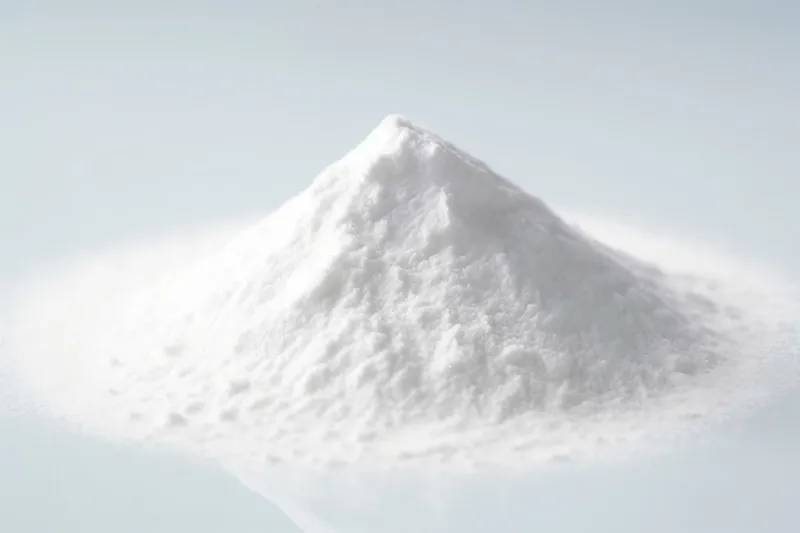
Efeitos de modificação positiva do carbonato de cálcio
1 Benefícios ambientais do carbonato de cálcio
1.1 Conservação dos Recursos Petrolíferos
Impacto calculado do carbonato de cálcio em embalagens plásticas
Usando carbonato de cálcio 30% em PE, 3 milhões de toneladas de sacolas plásticas poderiam economizar 900.000 toneladas de resina à base de petróleo e 2,7 milhões de toneladas de óleo.
1.2 Desempenho ecologicamente correto
Incorporar carbonato de cálcio em sacos plásticos de lixo destinados à incineração pode aumentar a eficiência da combustão e reduzir significativamente o tempo de incineração. Quando queimado, o carbonato de cálcio se expande dentro do filme plástico, criando vários pequenos furos que aumentam a área de superfície disponível para combustão. Esse fenômeno acelera o processo de queima. Por exemplo, o tempo de incineração para filme plástico de polietileno contendo carbonato de cálcio 30% é reduzido de 12 segundos (para plástico puro) para apenas 4 segundos.
Além disso, filmes plásticos cheios de carbonato de cálcio promovem uma combustão mais completa. Isso minimiza a fumaça preta do efeito pavio do carbonato de cálcio. A alcalinidade do carbonato de cálcio ajuda a absorver gases ácidos. Isso reduz a fumaça tóxica e o risco de chuva ácida.
No Japão, as regulamentações estipulam que sacos plásticos de lixo para incineração devem conter pelo menos 30% de carbonato de cálcio. Além da velocidade de queima melhorada, sacos cheios de carbonato de cálcio geram menos calor, não produzem gotejamentos ou fumaça preta, mitigam a poluição secundária e não são prejudiciais aos incineradores.
2. Efeitos comuns de modificação do carbonato de cálcio
2.1 Melhoria da rigidez dos materiais compósitos
O carbonato de cálcio aumenta a resistência à flexão, o módulo de flexão, a dureza e a resistência ao desgaste de materiais compostos. Em filmes plásticos, a rigidez aumentada melhora significativamente a rigidez, facilitando a ondulação plana e a integridade estrutural geral.
2.2 Estabilidade dimensional aprimorada de materiais compósitos
O carbonato de cálcio contribui para melhorar a estabilidade dimensional reduzindo a contração e a deformação, diminuindo o coeficiente de expansão linear, minimizando a fluência e promovendo a isotropia. A inclusão de carbonato de cálcio em compósitos melhora significativamente a estabilidade dimensional.
2.3 Melhoria da resistência ao calor em materiais compósitos
O carbonato de cálcio aumenta a estabilidade térmica de materiais compostos ao absorver substâncias que promovem a decomposição. Por exemplo, compostos de PBAT/carbonato de cálcio exibem estabilidade térmica significativamente maior em comparação ao PBAT puro. Além disso, a incorporação de carbonato de cálcio leve em produtos de PVC absorve efetivamente o cloreto de hidrogênio produzido durante a decomposição, aumentando muito a estabilidade térmica do processamento do PVC.
2.4 Resistência aprimorada ao rasgo de filmes
Filmes plásticos típicos geralmente têm alta resistência longitudinal, mas baixa resistência transversal, particularmente em materiais como filmes de poliéster alifático PBS, PLA e PHA. A adição de carbonato de cálcio pode melhorar a isotropia desses materiais compostos, levando a uma resistência significativamente melhorada ao rasgo.
3. Propriedades especiais modificadas do carbonato de cálcio
3.1 Efeitos nas propriedades de tração e impacto
O impacto do carbonato de cálcio na resistência à tração e ao impacto em filmes plásticos não é universal; ele é influenciado por fatores como tamanho de partícula e tratamento de superfície.
Efeito do tamanho das partículas: Diferentes tamanhos de partículas de carbonato de cálcio produzem efeitos de modificação variados em plásticos, conforme ilustrado na Tabela 1. Geralmente, tamanhos de partículas abaixo de 1000 mesh são usados para modificação incremental. Tamanhos de partículas entre 1000 e 3000 mesh, com uma quantidade de adição abaixo de 10%, podem atingir alguns efeitos de modificação. Em contraste, o carbonato de cálcio com tamanhos de partículas acima de 5000 mesh, classificado como carbonato de cálcio funcional, demonstra efeitos de modificação significativos e pode melhorar tanto a resistência à tração quanto a resistência ao impacto. Embora o carbonato de cálcio em nanoescala tenha um tamanho de partícula mais fino, sua dificuldade atual na dispersão limita sua eficácia, restringindo-o a resultados de modificação semelhantes ao carbonato de cálcio de 8000 mesh.
Tabela 1: Efeito do Carbonato de Cálcio Pesado com Diferentes Tamanhos de Partículas no Desempenho de Materiais Compósitos de PP
Tamanho da malha do carbonato de cálcio pesado tratado com agente de acoplamento (30%) | 2000 | 1250 | 800 | 500 |
Índice de fluxo de fusão (g/10min) | 4.0 | 5.0 | 5.6 | 5.5 |
Resistência à tração (MPa) | 19.3 | 18.4 | 18.7 | 18.1 |
Alongamento na ruptura (%) | 422 | 420 | 341 | 367 |
Resistência à flexão (MPa) | 28 | 28.6 | 28.2 | 28.4 |
Módulo de flexão (MPa) | 1287 | 1291 | 1303 | 1294 |
Resistência ao impacto Izod (J/m) | 113 | 89 | 86 | 78 |
Conforme mostrado na Tabela 1, tamanhos de partículas mais finas de carbonato de cálcio levam a maior resistência ao impacto, resistência à tração e alongamento na ruptura, enquanto a resistência à flexão e o módulo de flexão permanecem relativamente inalterados. No entanto, a fluidez do material compósito diminui com tamanhos de partículas mais finas.
Efeito do tratamento de superfície: O tratamento de superfície adequado do carbonato de cálcio com tamanhos de partículas adequados pode aumentar significativamente as resistências à tração e ao impacto de materiais compostos. Recentemente, avanços na teoria de compostos orgânicos/inorgânicos transformaram o carbonato de cálcio de um simples enchimento em um novo material de enchimento funcional. Por exemplo, a resistência ao impacto entalhado de um composto de polipropileno (PP)/carbonato de cálcio homopolímero pode mais que dobrar em comparação ao plástico base.
3.2 Supressão de fumaça durante a combustão
O carbonato de cálcio exibe excelentes capacidades de supressão de fumaça. Isso se deve à sua capacidade de reagir com haletos de hidrogênio na fumaça, formando cloreto de cálcio estável (CaCl₂). Portanto, ele pode ser usado como um supressor de fumaça em qualquer polímero que produza haletos de hidrogênio durante a combustão, incluindo cloreto de vinila, polietileno clorossulfonado e borracha de cloropreno.
Como a combustão é uma reação heterogênea sólido-gás que ocorre na superfície de partículas sólidas, o tamanho da partícula de carbonato de cálcio desempenha um papel crucial em sua eficácia de supressão de fumaça. Partículas mais finas possuem uma área de superfície específica significativamente maior, o que aumenta o efeito de supressão de fumaça.
3.3 Agente antiaderente
Filmes tubulares soprados contendo carbonato de cálcio demonstram excelentes propriedades de abertura e resistem à adesão durante a ondulação. Neste contexto, o carbonato de cálcio funciona efetivamente como um agente antiadesão.
3.4 Aumentar a condutividade térmica
Adicionar carbonato de cálcio aumenta a condutividade térmica do filme. A bolha do filme soprado esfria mais rápido. Isso aumenta a produção e aumenta a saída da extrusora. Usando carbonato de cálcio leve 25% em folha de PVC como exemplo, leva apenas 3,5 segundos para aquecê-lo a 200 °C. A folha de PVC puro leva 10,8 segundos. A condutividade térmica aumentou em 3 vezes.
3.5 Melhore a fluidez
O carbonato de cálcio pode melhorar a fluidez do sistema composto, reduzir a viscosidade do fundido e o torque da extrusora, aumentar a saída da extrusora e melhorar a eficiência da produção. Diferentes tipos de carbonato de cálcio têm diferentes efeitos no fluxo. A ordem da fluidez do material composto específico é carbonato de cálcio de calcita grande> carbonato de cálcio de mármore, carbonato de cálcio de dolomita> carbonato de cálcio de calcita pequena> carbonato de cálcio leve.
3.6 Desempenho de correspondência de cores
Substituição de alguns pigmentos brancos: Carbonato de cálcio de alta brancura pode substituir alguns pigmentos brancos, como dióxido de titânio, economizando assim o conteúdo do caro dióxido de titânio. Carbonato de cálcio de calcita grande é a primeira escolha devido à sua alta brancura e alto poder de cobertura. A razão pela qual o carbonato de cálcio pode ser usado como um pigmento branco é principalmente porque ele tem um certo poder de cobertura. O poder de cobertura de um revestimento se refere à quantidade mínima de tinta necessária para aplicar uniformemente a tinta na superfície de um objeto para que a cor base não apareça mais. É expresso em g/㎡.
O poder de cobertura de vários corantes em revestimentos é mostrado na Tabela 2:
Tabela 2: Poder de ocultação de alguns pigmentos inorgânicos e orgânicos
Nome do pigmento | Poder de cobertura (g/cm) |
Para vermelho (matiz claro) | 18.1-16.3 |
Para vermelho (tom escuro) | 17.1-15.0 |
Lago vermelho c | 23.8-18.8 |
Litol vermelho (lago Ba) | 33.7-21.7 |
Litol vermelho (lago Ca) | 49.0-33.7 |
Rubi litol | 33.9 |
Lago escarlate ianque | 88.5 |
Rodamina Y (precipitado de tungstato) | 25.1 |
Rodamina B (precipitado de fosfotungstato) | 16.1 |
Toluidina castanha vermelha | 34.8-37.7 |
Vermelho resistente à luz BL | 12.4 |
Dióxido de titânio | 18.4 |
(tipo rutilo, tipo anatase) | 19.5 |
Óxido de zinco | 24.8 |
Sulfato de bário | 30.6 |
Carbonato de cálcio | 31.4 |
Hansa amarelo G | 54.9 |
Hansa amarelo 10G | 58.8 |
Laranja permanente | 29.6 |
Verde malaquita | 5.4 |
Pigmento verde B | 2.7 |
Azul de malaquita (precipitado de fosfotungstato) | 7.7 |
Azul malaquita | 68.5 |
Violeta de metila (precipitado de fosfotungstato) | 7.6 |
Violeta de metila (precipitante de tanino) | 4.9 |
Violeta resistente à luz solar | 10.2 |
Azul de ftalocianina | 4.5 |
Argamassa de zinco e bário (pó de chumbo) | 23.6 |
Argamassa de chumbo (sulfato básico de chumbo) | 26.9 |
Trióxido de antimônio | 22.7 |
Talco | 32.2 |
O poder de cobertura de um material está intimamente relacionado ao seu índice de refração. Geralmente, um índice de refração mais alto resulta em maior poder de cobertura e uma tonalidade branca mais intensa. O índice de refração de vários materiais brancos é detalhado na Tabela 3.
Tabela 3: Índice de refração de vários materiais brancos
Materiais brancos | Número de índice de corante | Índice de refração |
Dióxido de titânio (tipo rutilo) | Argamassa pigmentada 6 | 2.70 |
Pó de titânio (tipo anatase) | Argamassa pigmentada 6 | 2.55 |
Óxido de zircônio | Argamassa pigmentada 12 | 2.40 |
Sulfeto de zinco | 2.37 | |
Trióxido de antimônio | Argamassa pigmentada 11 | 2.19 |
Óxido de zinco | Argamassa pigmentada 4 | 2.00 |
Litopona (pó de zinco-bário) | Argamassa colorida 21 | 2.10 |
Sulfato de bário | Argamassa pigmentada 18 | 1.64 |
Carbonato de cálcio | Argamassa pigmentada 27 | 1.58 |
Talco | Número de índice de corante | 1.54 |
Impacto na coloração A cor branca natural do carbonato de cálcio influencia sua capacidade de combinar cores brilhantes, tornando desafiador obter combinações de cores brilhantes. Além disso, pode complicar a combinação de pretos especiais.
Impacto na luz colorida Além de sua cor branca natural, o carbonato de cálcio pode exibir diferentes luzes coloridas, afetando a pureza da cor. Luz colorida se refere aos matizes adicionais que um objeto exibe junto com sua cor principal. Por exemplo, cores complementares são encontradas em extremidades opostas do espectro de cores; o azul, por exemplo, é complementado pelo amarelo. A mistura delas pode produzir luz branca, um método eficaz para neutralizar a luz colorida.
A cor base emitida pelo carbonato de cálcio varia conforme a origem. Por exemplo:
- O carbonato de cálcio de Sichuan tem uma cor base azul.
- O carbonato de cálcio de Guangxi tem uma cor base vermelha.
- O carbonato de cálcio de Jiangxi também tem uma cor de base azul.
Ao combinar cores, a luz colorida do carbonato de cálcio deve se alinhar com o matiz de coloração primário. Por exemplo, o carbonato de cálcio com uma tonalidade azul pode neutralizar o poder de coloração dos pigmentos amarelos. Ele também é comumente usado para neutralizar a luz colorida amarela em produtos.
Melhorando o astigmatismo em produtos plásticos: embora a adição de carbonato de cálcio não melhore o brilho dos produtos plásticos, ela efetivamente reduz o brilho, proporcionando um efeito fosco.
3.7 Aumentando a respirabilidade
Filmes plásticos cheios de carbonato de cálcio criam poros minúsculos durante o alongamento, permitindo que o vapor de água passe enquanto previne a infiltração de água líquida. Essa característica os torna adequados para produzir produtos plásticos respiráveis. Para resultados ótimos, somente carbonato de cálcio com um tamanho de partícula de 3000 mesh ou mais fino deve ser usado, com uma distribuição de tamanho de partícula estreita.
3.8 Promovendo o desempenho de degradação dos produtos
Quando sacos plásticos de polietileno contendo carbonato de cálcio são enterrados, o carbonato de cálcio pode reagir com dióxido de carbono e água para formar bicarbonato de cálcio solúvel em água (Ca(HCO₃)₂), que pode deixar o filme. Esse processo cria pequenos furos no filme, aumentando a área de superfície em contato com o ar e micro-organismos, facilitando assim a degradação do produto.
3.9 Papel da nucleação do carbonato de cálcio
O nanocarbonato de cálcio (CaCO₃) desempenha um papel crucial na nucleação da cristalização do polipropileno, aumentando o conteúdo de cristais β e, assim, melhorando a resistência ao impacto do polipropileno.
3.10 Redução da absorção de água em plásticos PA
A absorção de água de compósitos de poliamida (PA)/carbonato de cálcio é significativamente menor do que a da resina PA pura. Por exemplo, incorporar carbonato de cálcio 25% em PA6 pode reduzir a taxa de absorção de água do material compósito em 56%.
3.11 Melhoria das propriedades da superfície
O carbonato de cálcio pode melhorar a tensão superficial de materiais compostos. Ele tem ótimas propriedades de adsorção. Isso melhora suas qualidades de galvanoplastia, revestimento e impressão.
3.12 Efeitos do carbonato de cálcio na formação de espuma
A influência do carbonato de cálcio no desempenho da formação de espuma de materiais plásticos é complexa e depende tanto do tamanho das partículas quanto da quantidade utilizada:
Carbonato de cálcio Tamanho: Quando o tamanho de partícula do carbonato de cálcio se alinha com o agente espumante, ele pode atuar como um agente nucleante. Este processo influencia positivamente a formação de espuma. O tamanho ideal de partícula é menor que 5 μm e deve evitar aglomeração. Se o tamanho de partícula exceder 10 μm ou for muito fino e aglomerar, pode impactar negativamente a formação de espuma. É recomendado usar carbonato de cálcio de malha 3000 (aproximadamente 4 μm) para garantir um tamanho abaixo de 5 μm sem aglomeração.
Os mecanismos pelos quais o carbonato de cálcio promove a formação de espuma incluem:
Atua como um agente nucleador, absorvendo gás espumante para criar núcleos de bolhas, controlando assim o número de poros e refinando seu tamanho.
Fornecendo rigidez que desacelera a deformação e a mobilidade do fundido, o que ajuda a inibir a expansão rápida dos poros e permite tamanhos de poros mais finos. O nanocarbonato de cálcio pode até gerar plásticos de espuma microporosos devido ao pequeno tamanho do agente nucleante.
Quantidade de carbonato de cálcio adicionado: A quantidade ideal de enchimento de carbonato de cálcio para melhorar a qualidade da espumação varia tipicamente de 10% a 30%. Se muito pouco for adicionado. Não haverá pontos de nucleação suficientes, levando a uma baixa taxa de formação de espuma. Por outro lado, se muito for usado, enquanto mais pontos de nucleação são criados, a resistência do derretimento pode diminuir excessivamente. Isso resulta em inúmeras bolhas quebradas e uma taxa de formação de espuma reduzida.
Dispersibilidade do Carbonato de Cálcio: A dispersão uniforme do carbonato de cálcio é essencial para promover a qualidade da espuma. O carbonato de cálcio distribuído uniformemente garante que não haja aglomeração. Se o tamanho da partícula estiver dentro de 5 μm, ele funcionará efetivamente como um agente nucleante sem afetar adversamente a formação de espuma.
Conteúdo de água do carbonato de cálcio: Se o teor de água do pó inorgânico for inferior a 0,5%, haverá impacto mínimo na formação de espuma.
Outras propriedades: O carbonato de cálcio também contribui para melhorar a resistência ao desgaste e a dureza em materiais compósitos.
Modificações negativas de enchimentos
1. Aumento da densidade de materiais compostos
A adição de carbonato de cálcio à resina resulta em um rápido aumento na densidade do material composto. Para produtos vendidos por peso, comprimento ou área, essa densidade aumentada pode compensar algumas vantagens de custo. A extensão do ganho de peso varia entre diferentes tipos de carbonato de cálcio, com a ordem de densidade específica da seguinte forma:
Carbonato de cálcio leve < Carbonato de cálcio de calcita grande < Carbonato de cálcio de mármore < Carbonato de cálcio de dolomita < Carbonato de cálcio de calcita pequena.
Como reduzir a densidade de plásticos compostos de carbonato de cálcio:
1.1 Alongamento de produtos para redução de peso:
O alongamento cria lacunas de deformação entre o plástico e o carbonato de cálcio, reduzindo ligeiramente a densidade geral. Por exemplo, um filme de polietileno esticado preenchido com carbonato de cálcio 30% tem uma densidade de 1,1 g/cm³, em comparação com 1,2 g/cm³ para a versão não esticada. Esta técnica é aplicável a vários produtos plásticos, como arame plano, filme soprado, fita de cintagem e filme lacrimal.
1.2 Microespuma do produto para redução de peso:
Utilizar a umidade absorvida pelo enchimento para microespuma pode reduzir significativamente a densidade sem comprometer o desempenho. Por exemplo, nosso material composto de carbonato de cálcio leve 50% pode atingir uma densidade mínima de 0,7 g/cm³ quando usado para produzir filmes, representando uma redução de 45%.
1.3 Preenchimento oco para redução de peso:
Empregar tecnologia de escavação de pó inorgânico simples e econômica permite a produção de produtos de carbonato de cálcio ocos, o que reduz muito a densidade. A densidade desses produtos ocos pode ser reduzida para aproximadamente 0,7 g/cm³.
2. Redução do brilho em materiais compósitos
O método de processamento e o tipo de carbonato de cálcio afetam o brilho da superfície de produtos compostos. A ordem de brilho para diferentes materiais compostos é a seguinte:
- Processo úmido > Processo seco
- Carbonato de cálcio leve > Carbonato de cálcio de calcita grande > Carbonato de cálcio de mármore > Carbonato de cálcio de calcita pequena > Carbonato de cálcio de dolomita.
3. Redução da transparência em materiais compósitos
O carbonato de cálcio tem um índice de refração que difere significativamente do de resinas comuns como polietileno e polipropileno. Como resultado, enchimentos de carbonato de cálcio de tamanho convencional podem impactar negativamente a transparência dos filmes. Apenas o nanocarbonato de cálcio, com um tamanho abaixo de 200 nanômetros, pode manter a transparência do composto. Ondas de luz podem efetivamente contornar essas partículas pequenas.
4. Redução do alongamento na ruptura em materiais compósitos
A alta rigidez do carbonato de cálcio pode diminuir a ductilidade original do material compósito. Essa rigidez aumentada reduz a mobilidade das cadeias macromoleculares, resultando em um alongamento reduzido na ruptura do produto final.
5. Diminuição da resistência à tração e ao impacto
Em muitos casos, a adição de carbonato de cálcio pode levar à redução da resistência à tração e à resistência ao impacto no material composto. Isso é particularmente verdadeiro se as partículas de carbonato de cálcio forem muito grandes ou se o tratamento de superfície do carbonato de cálcio for inadequado. O declínio mais notável é frequentemente visto na resistência à tração.
6. Aumento do fenômeno de clareamento por estresse
Quando você adiciona muito carbonato de cálcio à resina, pode causar lacunas e riscos prateados quando o produto é esticado. Isso piora o clareamento por estresse da resina.
7. Aceleração do envelhecimento do produto
Todos os materiais em pó inorgânicos, incluindo carbonato de cálcio, podem acelerar o envelhecimento de materiais compostos, levando à redução da longevidade e do desempenho dos produtos.
8. Redução da força de ligação entre materiais
O uso de carbonato de cálcio pode diminuir a resistência de ligação dos filmes, como reduzir a resistência da selagem a quente, e também pode diminuir a resistência da soldagem dos tubos.