De uma perspectiva profissional sobre processos de modificação de partículas de pó, as principais diferenças entre os métodos úmido e seco podem ser analisadas em seis dimensões principais:
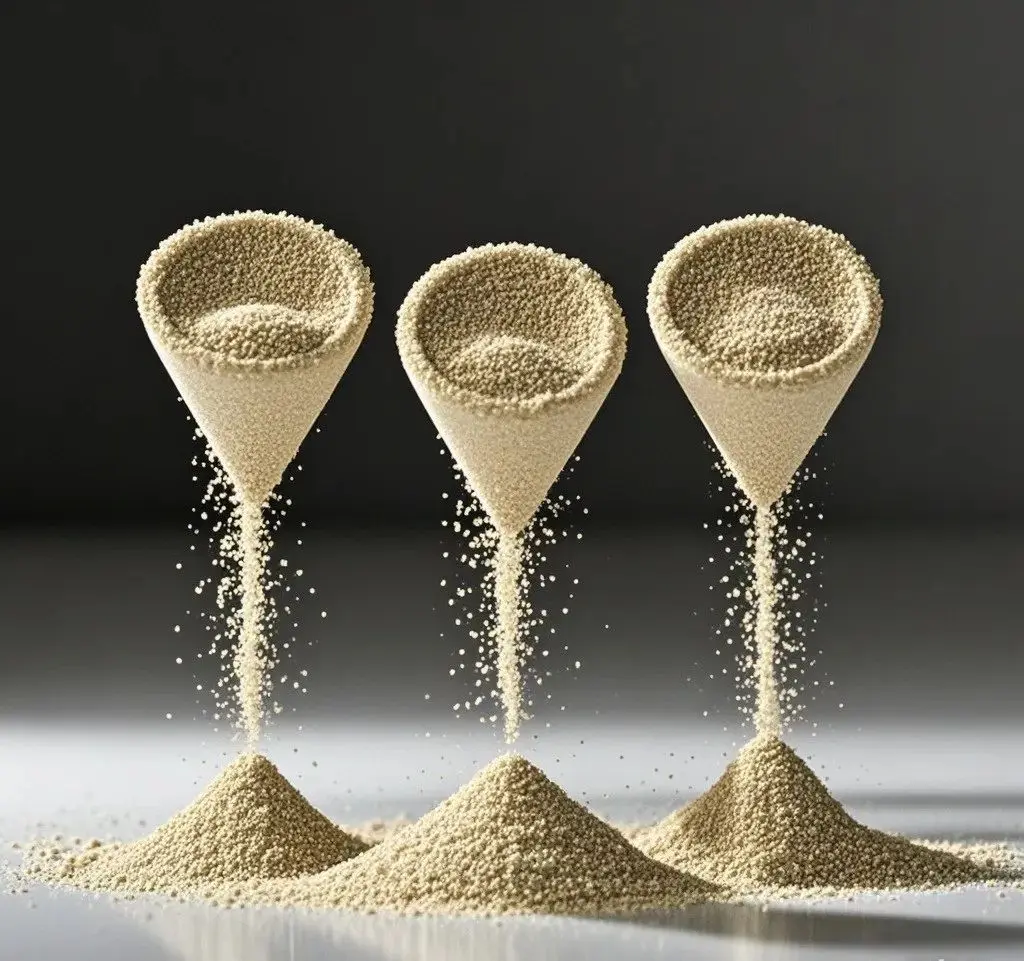
Adaptabilidade do Processo
Método Molhado: Adequado para pós ultrafinos com tamanhos de partículas
≤5μm (por exemplo, nano carbonato de cálcio). O ambiente líquido previne aglomeração dura durante a secagem. Por exemplo, na produção de pigmentos de mica perolados que requerem revestimento de TiO₂, o método úmido garante uniformidade de revestimento dentro de ± 5 nm.
Método Seco: Adequado para pós de tamanho micrométrico com D50 ≥10μm (por exemplo, carbonato de cálcio moído convencional). Misturadores de alta velocidade (300-1500 rpm) permitem modificação rápida, com capacidade de processamento de unidade única de até 5t/h.
Mecanismo de dispersão de modificadores
Método Úmido: Utiliza solventes (por exemplo, água, etanol) para formar uma camada dupla de difusão. A suspensão estável é obtida quando o potencial Zeta é controlado em ±30mV. Por exemplo, agentes de acoplamento de silano sofrem hidrólise e então condensam com grupos hidroxila em superfícies de SiO₂, aumentando a eficiência de ligação para mais de 90%.
Método Seco: Depende de energia mecânica (força de cisalhamento >10⁴ s⁻¹) para quebrar aglomerados modificadores. No entanto, as taxas de revestimento reais normalmente não excedem 75%, exigindo a adição de auxiliares de dispersão de 0,5-1% (por exemplo, ácido esteárico).
Equipamentos e Consumo de Energia
Método úmido: requer caldeiras de reação revestidas (coeficiente de transferência de calor: 200-500 W/m²·K). Após a modificação, os materiais passam por desidratação centrífuga (consumo de energia: 0,8 kWh/kg) e secagem por pulverização (temperatura do ar de entrada: 180-220℃).
Método Seco: Utiliza máquinas de modificação contínua do tipo SLG, com consumo específico de energia em torno de 0,15 kWh/kg. O investimento em equipamento é reduzido em 40%, mas a concentração de poeira deve ser controlada abaixo de 10 mg/m³.
Indicadores-chave de qualidade
Método úmido: Índice de ativação ≥98%, com valor de absorção de óleo reduzido em 30% (por exemplo, caulim modificado diminui de 80g/100g para 55g/100g).
Método seco: desvio de espessura do revestimento ±15 nm, resistividade de volume ajustável dentro de 10¹²-10¹⁵ Ω·cm (por exemplo, hidróxido de alumínio modificado para aplicações de cabo).
Cenários de aplicação
Método úmido:
Plásticos de engenharia de alta qualidade (por exemplo, PA6 + fibra de vidro 30%) requerem cargas modificadas com D99 ≤3μm.
Revestimento de Al₂O₃ para materiais de cátodo de bateria de lítio (por exemplo, NCM811).
Método Seco:
Carbonato de cálcio pesado modificado (malha 1250) para tubos de PVC, com controle de custo de 800 RMB/tonelada.
Caulim calcinado para revestimentos arquitetônicos, mantendo um nível de brancura acima de 92%.
Economia de Processos
Método Úmido: O custo total é 25-40% mais alto do que o método seco, com recuperação de solvente respondendo por 18% de custos. No entanto, o prêmio do produto pode chegar a 30-50% (por exemplo, pigmentos perolados sendo vendidos por 80.000-150.000 RMB/tonelada).
Método a seco: o consumo de energia por tonelada é reduzido em 60%, tornando-o adequado para modificação de pó em larga escala (produção anual > 50.000 toneladas), com um período de retorno do investimento reduzido para 2 a 3 anos.
Os avanços tecnológicos atuais indicam que o método úmido está evoluindo para o processamento contínuo de microrreator (tempo de residência <5 minutos), enquanto o método seco está fazendo avanços em equipamentos de modificação de moinho de vórtice integrado (aumentando a área de superfície específica em 20%). Ao selecionar um processo de modificação, as empresas devem avaliar de forma abrangente o posicionamento do produto (produção de ponta vs. em massa), intensidade de investimento de capital (diferença de CAPEX de 2-3 vezes) e regulamentações ambientais (limites de emissão de COVs: 30 mg/m³).
Conclusão
Pó épico A Machinery é especializada em soluções avançadas de modificação de partículas de pó, oferecendo tecnologias de processamento úmido e seco para atender a diversas necessidades industriais. Com expertise central europeia e décadas de experiência, fornecemos equipamentos de modificação de alta eficiência que garantem revestimento de partículas ideal, eficiência energética e custo-benefício. Seja para materiais de ponta, como cátodos de bateria de lítio ou processamento de pó a granel em larga escala, Pó épico A Machinery oferece soluções personalizadas para melhorar o desempenho do produto e atender às crescentes demandas do mercado.