Barium sulfate has excellent chemical inertness, high specific gravity, and low oil absorption, making it widely used in anti-corrosion coatings. The paint film exhibits good acid and alkali resistance, low viscosity, and smooth leveling.
However, inorganic fillers may have interface compatibility issues with organic resins, affecting the final physical and chemical properties of the paint film. To improve compatibility, inorganic fillers are typically surface-modified.
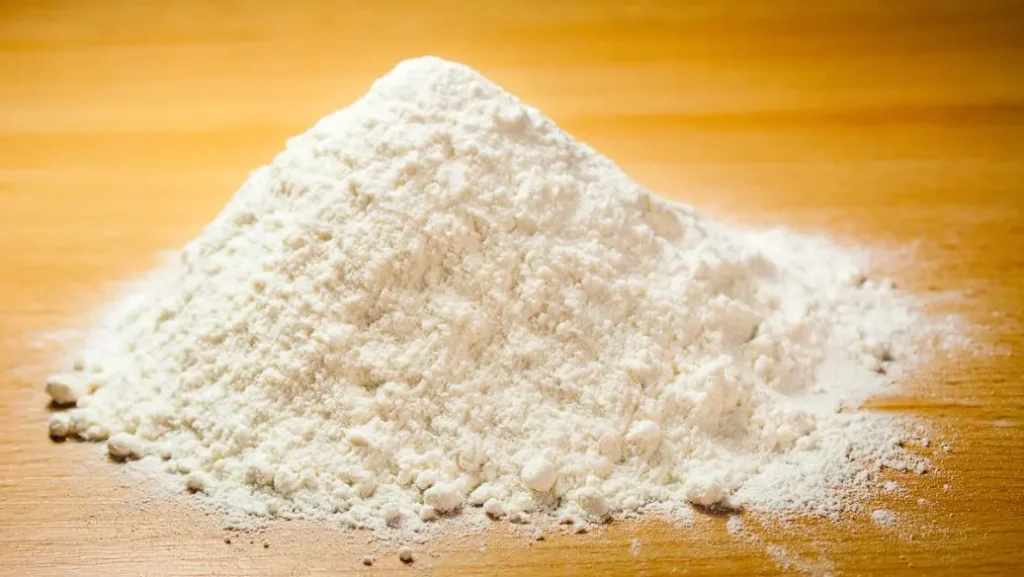
Since different surface modifiers have distinct functions, selecting the appropriate modifier is crucial for different systems. A comparative study was conducted by testing the conventional mechanical properties, initial water resistance, salt spray resistance, resistance to room temperature deionized water, resistance to 0.1 mol/L sulfuric acid, and resistance to 0.1 mol/L sodium hydroxide of the paint film.
1. Experimental process
Preparation Process:
(1) Add epoxy ester resin and water-based drying agent in sequence, stirring at 400-600 r/min at low speed. Then, add the neutralizer DMEA and continue stirring at low speed.
(2) Gradually add water in small amounts for emulsification, adjusting the speed to about 1000 r/min based on the emulsification process.
(3) After emulsification, add the dispersant and defoaming agent in sequence, ensuring even dispersion.
(4) Add carbon black, stir at low speed, and cover the lid after all materials are added. Disperse at approximately 1200 r/min, then add barium sulfate and strontium chrome yellow. Continue dispersing before adding all remaining components for further dispersion.
(5) Introduce zirconium beads for grinding at 3000-3500 r/min for 1 hour, adjusting the scraper fineness accordingly.
2. Experimental Results
2.1 Performance Comparison of Different Ultrafine Barium Sulfates
The basic physical properties of ultrafine barium sulfate were tested following the GB/T
37041-2018 standard, with results shown in Table 2.
Three different surface modifiers were used to modify barium sulfate powder. The modified product’s whiteness, particle size, and other indicators remained similar to the original powder. Oil absorption decreased by 1 point, but the reduction was not significant. This was because the coupling agent used as a modifier did not greatly affect the powder’s oil absorption.
The four types of barium sulfate fillers were prepared based on the formula in Table 1, and their application performance in water-based epoxy ester primers was compared.
2.2 Conventional Performance Test
When barium sulfate modified with different agents is used in water-based epoxy ester primer, its dispersibility remains consistent. It meets the product requirement of 10 µm within the same grinding time. This is because it is already one of the most dispersible non-metallic mineral fillers, leaving limited room for further improvement through surface modification.
In terms of hardness and adhesion, surface-modified barium sulfate shows no significant improvement over the original powder. The hardness variation among different fillers mainly depends on their Mohs hardness, with barium sulfate rated at 3, which is considered medium. Since it is not typically used to enhance paint film hardness, modification has little effect in this aspect.
Regarding glossiness, the modified barium sulfate performs similarly to the original powder. This is mainly because its oil absorption remains nearly unchanged, resulting in minimal gloss improvement.
For storage stability, barium sulfate modified with titanate coupling agent and epoxy silane shows coarsening, whereas the original powder and alkyl silane-modified barium sulfate do not exhibit this issue.
2.3 Anticorrosion Performance Test
Compared to the original powder, barium sulfate modified with titanate coupling agent shows significant improvement in acid and water resistance.
- Acid resistance increases from 14 days to 25 days.
- Resistance to deionized water at room temperature improves from 17 days to 32 days.
- Alkali resistance decreases slightly.
- Initial water resistance and salt spray resistance remain unchanged.
However, barium sulfate modified with alkyl silane and epoxy silane shows no significant improvement, with some properties even slightly decreasing. This is because silane coupling agents mainly rely on hydrolysis to form hydroxyl groups, which bond with hydroxyl groups on the mineral surface. Since barium sulfate has a low hydroxyl content, the modification effect is weak.
On the other hand, titanate coupling agents form a chemical bond with the inorganic filler through alkoxy groups, creating an organic active monolayer at the inorganic-organic interface. This improves the compatibility between barium sulfate and organic resins, significantly enhancing the acid and water resistance of the coating.
3. Conclusion
Barium sulfate offers advantages such as high specific gravity, dense particles, and low oil absorption, resulting in good dispersibility and adhesion. However, surface modification provides little improvement in these properties.
Since barium sulfate has a Mohs hardness of 3, it is not suitable for increasing paint film hardness. Additionally, due to its low hydroxyl content, modification with silane coupling agents is ineffective, leading to minimal performance enhancement.
Among the tested modifications, titanate coupling agents achieve the best results. When used in epoxy ester primers, they significantly enhance acid and water resistance, making them the most effective choice for improving the coating’s durability.
Choose Epic Powder for efficient, energy-saving, and environmentally friendly powder processing solutions!
Contact us to learn more about our products!