Silicon micro powder is a silica powder. It is made from crystalline quartz, fused silica, and other raw materials. The process is through grinding, precision classification, impurity removal, and other processes. It has many uses. These include copper-clad laminates, epoxy plastics, and electrical insulation. It’s in rubbers, plastics, coatings, adhesives, artificial stones, honeycomb ceramics, and cosmetics.
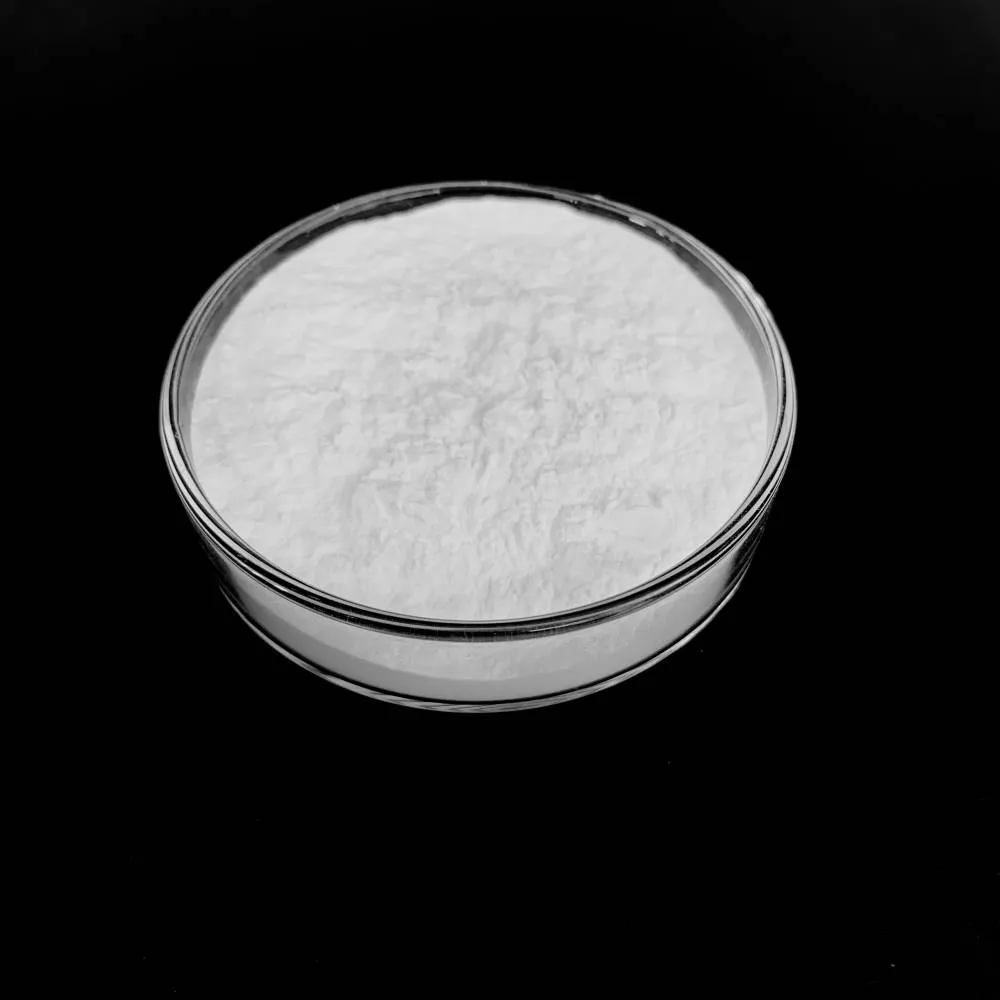
1. Copper-Clad Laminates
Currently, silicon powder used in copper-clad laminates can be categorized into crystalline silicon powder, molten silicon micro powder, spherical silicon powder, and composite silicon powder. The resin content in copper-clad laminates is about 50%, and the typical filling rate of silicon powder in the resin is around 30%. This means the filling weight ratio of silicon micro powder in copper-clad laminates is approximately 15%.
As an inorganic filler, silicon powder enhances the thermal stability, stiffness, thermal expansion coefficient, and thermal conductivity of copper-clad laminates, improving the reliability and heat dissipation of electronic products. It also has good dielectric properties. They can improve signal speed and quality in electronics. Crystalline silicon powder is cheaper. So, it is used in low-demand industries. These include air conditioners, refrigerators, washing machines, and desktop computers. Copper-clad laminates for smartphones, tablets, automobiles, network communication, and industrial equipment generally use molten silica micro powder due to specific requirements for dielectric constant and linear expansion coefficient. For uses like supercomputers and 5G, we need low-dielectric, low-loss spherical silicon micro powder. They are high-frequency and high-speed. It is a key filler. It must have low impurities and a high filling rate.
2. Epoxy Plastic Sealing Material
Silicon micro powder is a crucial filler in epoxy sealants (EMC), accounting for about 60%–90% of the composition. Improving the performance of epoxy sealants depends on enhancing the quality of silicon powder, thus imposing higher requirements on its particle size, purity, and sphericity. Middle and low-end epoxy plastic sealants often use angular silicon powder, while high-end sealants mainly utilize spherical silicon powder. Plastic sealing materials for discrete devices and small integrated electrical appliances typically contain crystalline and molten silicon micro powders. High thermal conductivity packaging for power devices mainly uses crystalline silicon powder along with other high thermal conductivity materials. For low expansion and low warpage packaging of large-scale integrated circuits, spherical silicon powder is preferred. Finally, low modulus packaged memory devices commonly use low-radiation spherical silicon powder as the filler.
It is estimated that China’s demand for spherical silicon powder for semiconductor packaging in 2022 will be 71,000 tons. As the proportion of advanced packaging continues to increase, it is expected to reach 93,000 tons in 2025, with a CAGR of 9.25%. Based on the price of spherical silicon powder of 15,000 yuan/ton, the market size in 2025 will be nearly 1.5 billion yuan.
3. Electrical Insulation Materials
Silicon micro powder is an epoxy resin insulation filler for electrical products. It reduces the cured material’s linear expansion coefficient and shrinkage during curing. This reduces stress and improves the insulation’s strength. It enhances its mechanical and electrical properties.
Therefore, customers in this field have specific functional requirements for silicon micro powder, such as a low linear expansion coefficient, high insulation, and high mechanical strength, while their demand for dielectric and thermal conductivity properties is relatively lower. In the field of electrical insulation materials, single-specification silicon powder products with an average particle size between 5 microns and 25 microns are typically selected based on the characteristics of electrical insulation products and the requirements of their production processes. There are also high standards for product whiteness and particle size distribution.
4. Rubber
Silicon micro powder offers advantages such as a small particle size, large specific surface area, good heat resistance, and wear resistance, which can improve the wear resistance, tensile strength, modulus, and high tear resistance of rubber composite materials. However, the surface of silicon powder contains many acidic silanol groups. If not modified, these groups can cause uneven dispersion of the silicon powder in rubber and may react with alkaline accelerators, prolonging the vulcanization time of rubber composite materials.
Currently, modification of silicon micro powder is mainly applied in rubber research, with silane coupling agent modification being the primary method. Examples include phenyltrimethoxysilane, ethylenetrimethoxysilane, hexamethyldisilazane, 3-mercaptopropyl triethoxysilane, and (3-aminopropyl) trimethoxysilane.
5. Plastics
Silicon micro powder can be used as a filler in plastics. This includes polyethylene (PE), polyvinyl chloride (PVC), polypropylene (PP), and polyphenylene oxide (PPO). It is widely used in many fields, including construction, automotive, and electronics. It is also used in insulation, agriculture, daily goods, and the military.
KH-550 modifies powdered quartz. Then, it is mixed with PE to make a plastic film for agricultural greenhouses. The results showed that, with 8%-12% powdered quartz, the film’s properties exceeded those of pure resin and met national standards. I used a silane coupling agent to modify silicon micro powder. I mixed the modified silicon powder with polyphenylene ether. This made a polyphenylene ether automotive plastic material. The results showed that the material was very hard. It had high wear, high-temperature, and corrosion resistance. So, it is suitable for automotive plastic products.
6. Paint
Manufacturers can use silicon micro powder as a filler in coatings. It lowers coating costs and improves properties. They must resist high temperatures, acids, alkalis, wear, and weather. It is commonly used in building materials, cars, pipes, hardware, and appliances.
In architectural coatings
Bai Wenkui et al. I used silica powder as a filler in exterior wall paints. They had a good look, high stability, and low cost. Yuan Rui et al. used ultrafine silica powder as a filler in phenylpropanoid coatings. The results showed that, with 35% or more silicon micro powder, the coating’s alkali resistance, washability, water absorption, and reflectivity were much better.
For latex coatings
Titanium dioxide is the main pigment and filler. But it is expensive and hard to make. Thus, research now focuses on using fillers with titanium dioxide. These fillers are calcium carbonate, anhydrous calcium sulfate, and silicon powder. Wang Pengzhu and colleagues used modified silica micro powder as a filler. It served as a partial replacement for titanium dioxide in latex coatings. A 1:3 mass ratio of titanium dioxide to silicon micro powder greatly improved the latex coating’s hardness, impact strength, and flexibility.
In epoxy floor coatings,
Silicon micro powder as a filler enhances wear resistance, acid and alkali resistance, high-temperature resistance, and mechanical strength. Hu Gaoping et al. mixed silicon powder of different particle sizes with epoxy resin, curing agents, and other raw materials to prepare strong acid-resistant epoxy floor coatings. These coatings were used in acetic acid distillation workshops to prevent local powdering caused by acetic acid corrosion.
In flame retardant insulation coatings, Liu Tongwang et al. I added activated silica micro powder to unsaturated polyester resin. I used it to make polyester insulation paint. The results showed that, at 35% activated silica micro powder, the paint improved. Its volume conductivity, water absorption, and mechanical strength all increased.
7. Adhesives
Silicon micro powder, as an inorganic functional filler, effectively reduces the linear expansion coefficient and shrinkage rate of cured adhesive resin. It improves the mechanical strength, heat resistance, permeability resistance, and heat dissipation performance of adhesives, thereby enhancing bonding and sealing effectiveness.
The particle size distribution of silica powder will affect the viscosity and sedimentation of the adhesive, thereby affecting the processability of the adhesive and the linear expansion coefficient after curing. Therefore, the adhesive field pays attention to the function of silica powder in reducing the linear expansion coefficient and improving the mechanical strength. It has high requirements for the appearance and particle size distribution of silica powder, and usually uses different particle size products with an average particle size of 0.1 micron-30 microns for compound use.
They change the silica powder and then apply it to vinyl silicone. As storage time increases, the viscosity of vinyl silicone remains stable. The product has high strength and good stability. Manufacturers can use it in heat-conducting silicone, gaskets, and dental materials for impressions.
8. Artificial Quartz Stone
Silicon micro powder used as a filler in artificial quartz boards can reduce unsaturated resin consumption and improve wear resistance, acid and alkali resistance, and mechanical strength. The filling ratio of silicon powder in artificial marble is generally around 30%. For example, Liu Huichen et al. proposed using silicon powder modified with a silane coupling agent in artificial quartz boards. This approach can reduce unsaturated resin usage and lower the processing cost of artificial quartz boards.
9. Automotive Honeycomb Ceramics
The Diesel Particulate Filter (DPF), made from honeycomb ceramic carriers for automobile exhaust purification and cordierite material for diesel engine exhaust purification, involves mixing, extruding, drying, and sintering materials such as alumina and silica micro powder. The main component of molten silicon micro powder is SiO2, which has an amorphous structure, ultrafine particles, and a large specific surface area. It acts as a mineralizer for solid-state reactions and sintering of silicate materials. Silicon powder enhances the strength of honeycomb ceramic carriers, reduces the thermal expansion coefficient of cordierite, and improves its service life. Spherical silicon powder can enhance the forming rate and stability of honeycomb ceramic products, with a weight ratio of about 13% in the honeycomb ceramic carrier.
10. Cosmetics
Spherical silica micro powder is in cosmetics like lipstick and powder. It has good fluidity and a large surface area. Its characteristics include:
- Improved fluidity and storage stability in powder products, preventing caking.
- Smaller average particle size providing good smoothness and fluidity.
- Larger specific surface area for better adsorption of sweat, fragrances, and nutrients, making formulations more economical.
- Spherical shape offering good skin affinity and tactile sensation.
In addition, spherical silica micro powder is easy to mix with other cosmetic components, is non-toxic, odorless, and naturally white. Its notable features include a strong ability to reflect ultraviolet rays, good stability, and no decomposition or discoloration when exposed to UV radiation. Furthermore, it does not react with other components in the formula, making it an excellent choice for sunscreen cosmetic ingredients.
The specification requirements for spherical silica micro powder used in cosmetics generally include:
- Silicon content of 99.9%
- Controllable particle size ranging from 0.2 to 2 microns
- Sphericity above 95%
Low radiation (uranium content < 0.5 ppb)
Conclusion
Different application fields have varying quality requirements for silicon powder. Therefore, when selecting silicon powder for a particular application, it is essential to consider the needs of downstream industries, as well as factors such as cost, efficiency, and performance. Choosing the appropriate type of silicon micro powder, along with the correct modification process and formula, is crucial.
With the continuous advancement of China’s economy and society, research on the application of silicon powder will increasingly focus on high-tech fields such as high-end copper-clad laminates, high-end coatings, high-performance adhesives, and insulation materials made from spherical silicon powder. Refinement and functional specialization are expected to be the main trends in the future application of silicon micro powder.
If you’re interested in jet mills to make silicon powder, please contact Epic’s technical team for more info.