Kuru presleme gibi özel seramiklerin oluşturulması için birçok yöntem vardır. slip döküm, enjeksiyon kalıplama ve jel döküm. Kuru presleme, düşük bağlayıcı içeriği, kurutma olmadan doğrudan sinterleme gibi avantajlar sunar. Basit bir üretim süreci, yüksek verimlilik, küçük yeşil gövde büzülmesi ve otomatik üretim. Özel seramiklerin üretiminde en yaygın kullanılan yöntemdir.
Yüksek yoğunluklu ve tekdüze yoğunluk gradyanlı yeşil bir gövdenin nasıl hazırlanacağı araştırmanın odak noktasıdır. Genel olarak, kuru presleme sırasında yeşil gövdenin yoğunluğunu etkileyen faktörler kuru presleme işlemi ve toz özellikleridir.
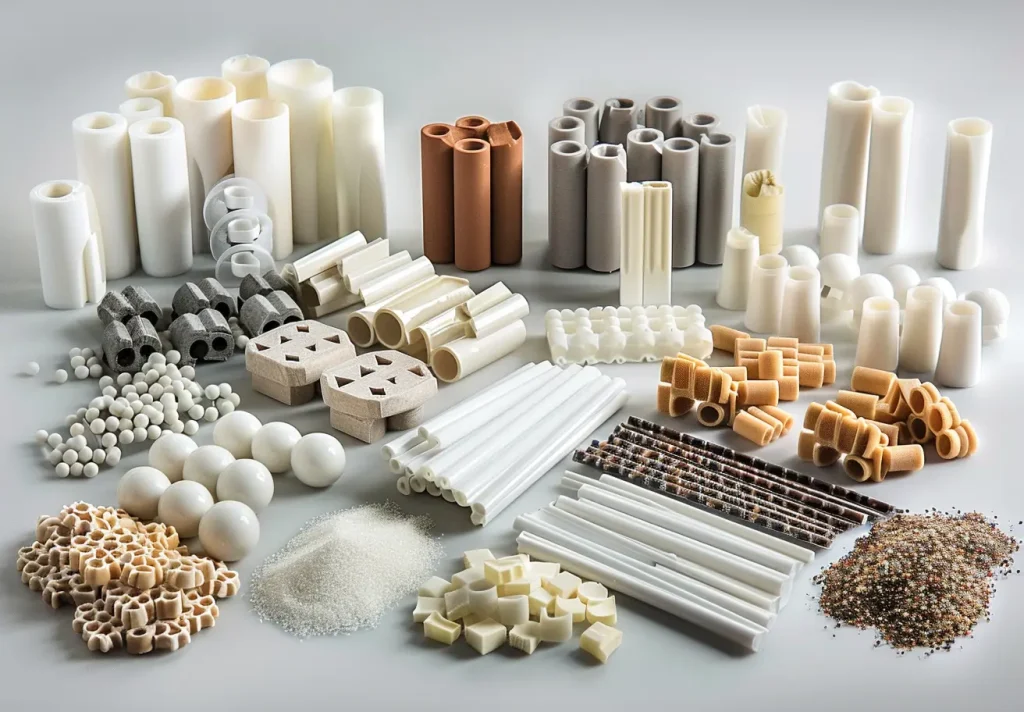
Kuru presleme işleminin etkisi
Kuru presleme işlemi esas olarak basınçlandırma yöntemi, basınçlandırma basıncı, basınçlandırma hızı ve tutma süresini ifade eder.
Basınçlandırma yöntemi
Kuru pres kalıplamada, basınçlandırma yöntemleri tek yönlü basınçlandırma ve çift yönlü basınçlandırmayı içerir. Farklı basınçlandırma yöntemleri, kalıpta farklı basınç iletimi ve dağılımıyla sonuçlanacaktır.
Baskı Basıncı
Genel olarak konuşursak, yeşil gövdenin yoğunluğu basınçtaki artışla artar. Özel seramik presleme işlemi sırasında, basıncın yeşil gövdenin yoğunluğu, mukavemeti ve gözenekliliği üzerindeki etkisi diğer faktörlerden daha önemlidir. Ayrıca, sinterlemeden sonra yeşil gövdenin performansı üzerinde önemli bir etkiye sahiptir.
Basınç çok düşükse, yeşil gövde maksimum yoğunluğa ulaşamaz ve bu da sinterleme sürecini etkiler. Öte yandan, basınç çok yüksekse, katman çatlamasına benzer kusurlar ortaya çıkabilir. Sadece basınç optimum seviyede olduğunda ideal yeşil gövde elde edilebilir.
Basınçlandırma Hızı ve Tutma Süresi
Basınçlandırma hızı ve tutma süresi, basınç iletimi ve gazın boşaltılmasıyla yakından ilişkili oldukları için, boşluğun performansını önemli ölçüde etkiler. Basınçlandırma çok hızlı ve tutma süresi çok kısaysa, gaz kolayca boşaltılmayacaktır. Benzer şekilde, basınç gerekli derinliğe iletilmediğinde, dış kuvvet uygun yoğunlaştırmadan önce kaldırılacak ve istenen boşluk kalitesine ulaşılması zorlaşacaktır. Ancak, basınçlandırma hızı çok yavaş ve tutma süresi çok uzunsa, üretim verimliliği düşecektir. Bu nedenle, basınçlandırma hızı ve tutma süresi, boşluğun boyutuna, şekline ve kalınlığına göre ayarlanmalıdır.
Araştırmanın birincil odak noktası, yüksek yoğunluklu ve tekdüze yoğunluk gradyanlı yeşil bir gövdenin nasıl hazırlanacağıdır. Genel olarak, kuru presleme sırasında yeşil gövdenin yoğunluğunu etkileyen faktörler arasında kuru presleme işlemi ve toz özellikleri yer alır.
Kuru Presleme İşleminin Etkisi
Kuru presleme işlemi öncelikle basınçlandırma yöntemi, basınçlandırma basıncı, basınçlandırma hızı ve tutma süresini ifade eder.
Kuru pres kalıplamada, basınçlandırma yöntemleri tek yönlü ve çift yönlü basınçlandırmayı içerir. Farklı basınçlandırma yöntemleri, kalıpta basıncın farklı iletimi ve dağılımıyla sonuçlanır.
Tozun özellikleri esas olarak parçacık boyutu, parçacık sınıflandırması, bağlayıcı ve su içeriği ve toz akışkanlığını ifade eder.
Parçacık Boyutu ve Parçacık Derecelendirmesi
Aynı basınç altında, büyük parçacık boyutuna sahip tozun yeşil kompakt yoğunluğu daha yüksekken, daha küçük parçacık boyutuna sahip tozun sinterleme yoğunluğu daha fazladır. Aynı parçacık boyutuna sahip tozlar için, hem yeşil kompakt yoğunluğu hem de sinterleme yoğunluğu daha yüksek basınçla artar. Bu nedenle, parçacık boyutunu artırmak yeşil gövde yoğunluğunu iyileştirmek için faydalıdır.
Bağlayıcı ve Su İçeriğinin Etkisi
Özel seramikler kuru preslendiğinde, seramik tozu öncelikle gereksinimleri karşılamak için granüle edilmeli ve ardından granüle edilmiş toz preslenerek yeşil gövde oluşturulmalıdır. Granüle edilmiş tozun özellikleri (örneğin, sözde parçacıkların şekli, boyutu, boyut dağılımı ve akışkanlığı) nihayetinde seramik yeşil gövdenin yoğunluğunu etkileyecektir. Bağlayıcı içeriği de granüle edilmiş tozun performansında önemli bir rol oynar. Özel seramik kuru presleme sırasında, bağlayıcı öncelikle bir bağlayıcı madde olarak görev yapar, sözde parçacıkların parçacık boyutunu artırır ve parçacık mukavemetini geliştirir.
Granülasyon işlemi sırasında bağlayıcı içeriği çok yüksekse, bulamacın viskozite katsayısı artar ve bu da daha küçük bir püskürtme atomizasyon açısıyla sonuçlanır. Bu, damlacıkların kurutma ve granülasyondan sonra kümelenmesine neden olur ve geniş bir parçacık boyutu dağılımına ve zayıf akışkanlığa sahip bir toza yol açar. Sonuç olarak, kuru presleme sırasında yüksek yoğunluklu bir yeşil gövde elde etmek zorlaşır. Tersine, bağlayıcı içeriği çok düşükse, yeşil gövdenin mukavemeti işleme gereksinimlerini karşılamada başarısız olur.
Su içeriği ayrıca yeşil gövdenin yoğunluğunu önemli ölçüde etkiler. Su içeriği çok yüksekse, kuruma büzülmesi önemli olacaktır ve yeşil gövdenin boyutunu kontrol etmeyi zorlaştıracaktır. Ek olarak, toz kalıplama sırasında kalıba yapışabilir ve yeşil gövdenin yoğunluğunu olumsuz etkileyebilir. Öte yandan, su içeriği çok düşükse, granülasyon tozunun ezme performansını engelleyecek ve yüksek yoğunluklu yeşil gövde elde etmeyi zorlaştıracaktır.
Toz akışkanlığı
İyi akışkanlık, özel seramik kuru presleme sırasında parçacıklar arasındaki iç sürtünmenin minimum olmasını sağlayarak tozun kalıbın her köşesini düzgün bir şekilde doldurmasını sağlar. Bu ayrıca tozun doldurma yoğunluğunun artmasına yardımcı olarak daha düşük basınç altında yoğun ve düzgün bir seramik gövdenin oluşmasını sağlar.
Seçmek Epik Toz Verimli, enerji tasarruflu ve çevre dostu kaolin işleme çözümleri için hava sınıflandırıcı!
Bize Ulaşın Ürünlerimiz hakkında daha fazla bilgi edinmek için!