Ultra ince kalsiyum karbonat için, parçacık boyutu, yüzey alanı, kristal formu ve yağ emilimi temel teknik göstergelerdir. Bu faktörler doğrudan ürün performansını etkiler. Diğer göstergeler de önemlidir ancak genellikle endüstriyel üretimde kontrol edilmesi daha kolaydır. Ancak, uzmanlaşmış uygulamalar için farklı kullanımlar farklı öncelikler gerektirir. Bu nedenle, göstergeler tüm durumlar için aynı şekilde ele alınmamalıdır.
Parçacık Boyutu ve Özgül Yüzey Alanı
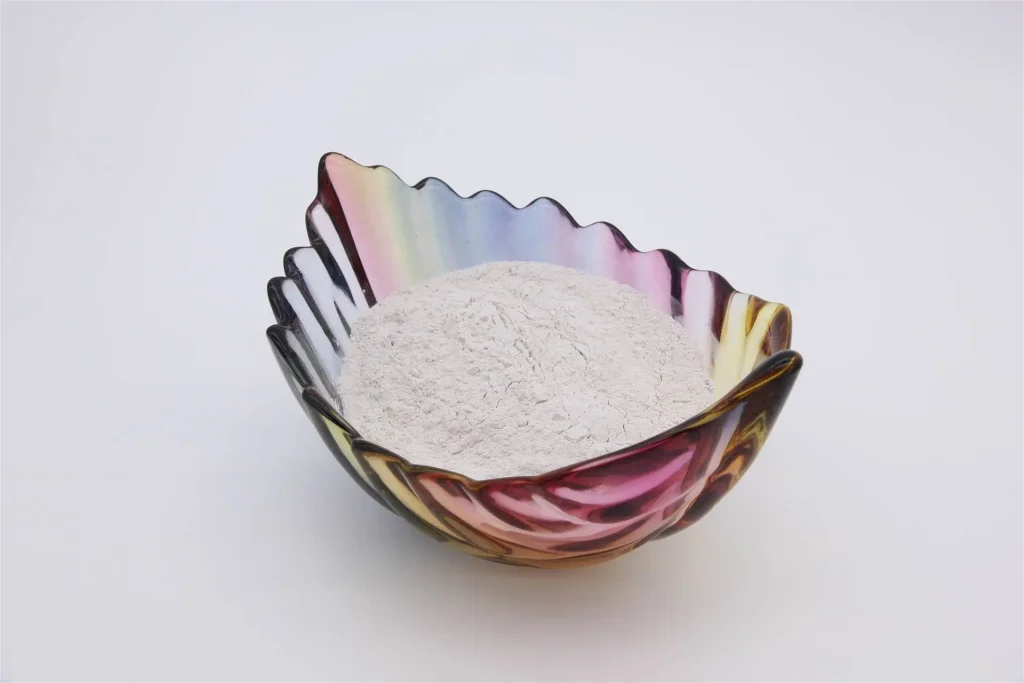
0,02–0,1 μm birincil parçacık boyutuna ulaşmak ultra ince kalsiyum karbonat için temel bir gerekliliktir. Bu olmadan, "ultra ince" olarak adlandırılamaz.
Ancak bu, kaliteli ultra ince kalsiyum karbonat yapımındaki görevin yalnızca yarısıdır. Yüzey işleme ve dispersiyon teknikleri eksikse, parçacıklar daha büyük ikincil parçacıklar halinde birleşecektir.
Bu kümeler yüzlerce nanometre boyutuna ulaşabilir. Transmisyon Elektron Mikroskobu (TEM) görüntüleri yalnızca birincil parçacıkları gösterir.
Numune hazırlama nedeniyle, gerçek aglomere parçacık boyutlarını yansıtmazlar. Yüksek aglomere ürünler genellikle daha düşük BET yüzey alanına sahiptir.
Bu nedenle, TEM ve BET yüzey alanı testini birleştirmek parçacık boyutu, şekli ve dağılımı hakkında daha eksiksiz bir görüş sağlar. Ortalama parçacık boyutu ile yüzey alanı arasında doğal bir ilişki vardır.
Bazı araştırmacılar parçacık boyutunu tahmin etmek için çökelme hacmini kullanır. Ancak çökelme hacmi yalnızca boyuttan etkilenmez.
Kireçtaşı kalitesi, kalsinasyon, sindirim ve karbonasyon koşulları gibi faktörlerin hepsi nihai boyutu etkiler. Ayrıca, kalsiyum karbonatın çeşitli kristal formları vardır. Bir form içinde bile, şekiller farklılık gösterir ve genellikle düzensizdir. Bu nedenle, kristal şekli çökelme hacmi sonuçlarını karmaşıklaştırır.
Tek bir form içinde bile şekiller farklılık gösterir ve genellikle düzensizdir. Bu nedenle, kristal şekli çökelme hacmi sonuçlarını karmaşıklaştırır. Parçacık boyutunu değerlendirmek için yalnızca çökelme hacmini kullanmak bilimsel değildir ve genellikle yanlıştır. Toplanmayı azaltmak için, ultra ince kalsiyum karbonat genellikle yüzey modifikasyonuna uğrar.
Bu sadece yüzey aktivitesini artırmakla kalmaz, aynı zamanda parçacık kümelenmesini önlemeye de yardımcı olur. Özel ürünler için kristal formu, parçacık boyutu, yüzey işleme maddesi ve hatta işleme teknikleri değişir. İşlem sırasında deneyim ve teknik bilgi çok önemlidir. Bu nedenle, tüm ultra ince kalsiyum karbonat türlerini değerlendirmek için tek bir standart kullanmak çok zordur.
Kristal Formu
Kristal formu ayrıca ultra ince kalsiyum karbonat için önemli bir teknik göstergedir. Standart hafif kalsiyum karbonat iğ şeklindedir.
PVC'de kullanılır, stres yaratır ve plastik filmlerde beyazlamaya neden olur. Ultra ince kalsiyum karbonat, belirli uygulamalara göre kristal formunda değişiklik göstermelidir. Plastikler için basit bir yapı, düşük paketleme hacmi ve düşük yağ emilimi tercih edilir. Kübik veya küresel şekiller idealdir.
0,072μm parçacık boyutuna sahip ultra ince kalsiyum karbonat PVC plastik performansını artırabilir. Yüzey pürüzsüzlüğünü, parlaklığını ve elektrik yalıtımını iyileştirir.
Yumuşak kablo bileşiklerinde, çift dolgu dozajıyla bile performans ulusal standartlar içinde kalır. Plastik filmlerde beyazlamayı azaltır ve düşük sıcaklıkta uzamayı artırır.
Ancak kapılar ve profiller gibi sert plastiklerde darbe dayanıklılığını artırır. Çentikli darbe direnci 49,1 kJ/m²'ye ulaşabilir. Kauçuk için zincir benzeri şekiller en iyi takviyeyi sunar.
Zincir şeklindeki kalsiyum karbonat, birçok parçacığın tek bir yönde hizalanmasıyla oluşur. Bu yapı, uzaysal kararlılığa sahiptir ve kauçukta iyi dağılır.
Karıştırma sırasında zincirler kırılır ve aktif yüzeyler açığa çıkar. Bu yüzeyler kauçuk zincirlerle sıkıca bağlanarak takviyeyi artırır.
Kauçukta, şekle göre takviye mukavemeti: zincir > iğne > küre > küptür. Mürekkep için, mürekkep özellikleri nedeniyle kübik şekiller en iyisidir. Reçine bazlı mürekkeplerde, ultra ince kalsiyum karbonat parlaklık, şeffaflık ve akışkanlık sağlamalıdır.
Kübik kristaller en iyi parlaklık performansını sağlar. Kağıt kaplamalar için genellikle çökeltilmiş kalsiyum karbonat kullanılır. Çok ince değildir; boyutu 0,1 ila 1 μm arasındadır. Yine de kristal şekli önemlidir.
Kağıt kaplamalar iyi opaklık, parlaklık, yüksek viskozite ve mürekkep emilimi gerektirir. İdeal kristal şekilleri arasında plaka benzeri ve kübik formlar bulunur. Özetle, ultra ince kalsiyum karbonat yalnızca boyut gereksinimlerini (0,02–0,1 μm) karşılamamalıdır
Ancak aynı zamanda kullanıma bağlı olarak kristal formunda tasarlanarak pazara hazır ürünler de oluşturulabilir.
Yağ Emilim Değeri
Ultra ince kalsiyum karbonatın yağ emilim değeri, uygulama performansını önemli ölçüde etkiler. Bu özellikle plastiklerde, kaplamalarda ve mürekkeplerde geçerlidir.
Yüksek yağ emilimi plastiklerde daha fazla plastikleştirici tüketilmesine neden olur.
Kaplamalarda ve mürekkeplerde viskoziteyi artırır. Bu nedenle yağ emilimi düşük kalmalıdır. Malzemenin fiziksel özelliklerinin ötesinde birçok faktör yağ emilimini etkiler.
Bunlar arasında partikül boyutu önemli bir faktördür. Bu nedenle, öncelikle ince partikül boyutu ve iyi dağılım sağlanmalıdır.
Ayrıca parçacık boyutuna uygun bir yüzey alanına sahip olması gerekir.
Ancak o zaman yağ emiliminin azaltılması düşünülmelidir. Eğer dağılım zayıfsa ve parçacıklar ciddi şekilde kümeleniyorsa, yüzey alanı çok düşüktür.
Yağ emilimi düşük olsa bile bu malzemenin pratik değeri pek azdır.
Ana İçerik
Ultra ince kalsiyum karbonatın (CaO) ana içeriği belirli bir aralıkta çok sıkı bir şekilde sınırlandırılmamalıdır. Çoğu durumda, ultra ince kalsiyum karbonat, kimyasal özelliklerden ziyade fiziksel özellikleri etkileyen işlevsel bir dolgu maddesi görevi görür.
Makul bir aralıkta, CaO içeriği hala performans ihtiyaçlarını karşılayabilir. Çeşitli kristal formları, iyi dağılım ve yüksek yüzey aktivitesine sahip kalsiyum karbonat üretmek için, değiştiriciler, dağıtıcılar ve yüzey aktif maddeler gibi katkı maddeleri sıklıkla eklenir.
Bu kasıtlı olarak eklenen "kirlilikler" genellikle ürün performansına zarar vermez ve hatta bazen onu iyileştirir. Ancak, nihai üründe ölçülen CaO içeriğini azaltabilirler. Elbette, demir ve manganez gibi zararlı elementler sıkı bir şekilde kontrol edilmelidir.
İster ham maddelerden ister işleme sırasında girsinler, rengi etkilerler ve reçinenin bozulmasını ve eskimesini hızlandırırlar. Bunlardan kesinlikle kaçınılmalıdır. Silisyum, alüminyum ve magnezyum gibi diğer safsızlıklar ürünün beyazlığını etkiler ve işleme verimliliğini engelleyebilir.
Bu nedenle, kireç taşı gibi ham maddeler dikkatlice seçilmeli ve kontrol edilmelidir. Bu nedenle, aşırı sıkı CaO içeriği sınırları, uzmanlaşmış ultra ince kalsiyum karbonat ürünlerinin geliştirilmesini kısıtlayabilir. Dengeli bir aralık daha pratiktir. Özet Ultra ince kalsiyum karbonat için temel yön, uzmanlaşma, seri geliştirme, çeşitlilik ve işlevselliktir.
Yalnızca 0,02–0,1 μm parçacık boyutunun kauçuk, plastik, mürekkep, kaplamalar veya kağıt gibi tüm endüstriler için uygun olduğunu varsaymak yanlıştır. Uygulamalar parçacık boyutu, kristal şekli, yüzey alanı, yağ emilimi ve ana içerik için özel gereksinimler gerektirir. Bu nedenle, tek bir evrensel standart tüm özel ultra ince kalsiyum karbonat ürünlerine uygulanamaz.
Epic Powder Machinery Hakkında
Epik Toz Machinery, ultra ince toz işleme için son teknoloji çözümler sunar. Müşterilerimizin plastik, kauçuk, kaplamalar ve daha fazlası genelinde yüksek performanslı, özelleştirilmiş sonuçlar elde etmelerine yardımcı oluyoruz.