Việc phát triển các công thức kết dính có thể vô cùng khó khăn. Vấn đề chính nằm ở nhu cầu về các công thức có mục tiêu. Nhiều nguyên liệu thô phù hợp phải được kết hợp để đạt được các đặc tính mong muốn, đòi hỏi phải liên tục thử nghiệm và sai sót để giải quyết các mâu thuẫn vốn có. Đặc biệt là khi đối mặt với tình trạng tắc nghẽn, việc đưa ra thêm một lựa chọn có thể dẫn đến một bước đột phá đáng kể.
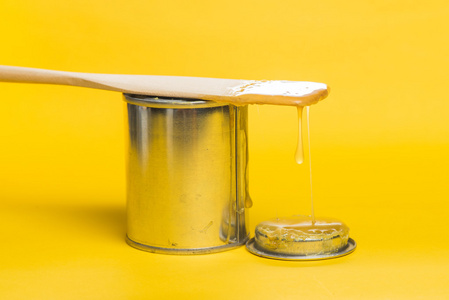
Những khó khăn chính trong việc phát triển công thức keo dán
Những thách thức trong việc tạo ra công thức keo dán có thể được hiểu rõ hơn thông qua các ví dụ thực tế. Tang Long và cộng sự đã khám phá một phương pháp phát triển công thức mới dành riêng cho các thành phần polyol trong keo dán polyurethane hai thành phần. Phương pháp của họ nhằm mục đích cân bằng sự đánh đổi hiệu suất giữa độ cứng thấp và cường độ liên kết cao.
Tối ưu hóa nguyên liệu thô
Các tác giả bắt đầu bằng cách sử dụng thiết kế thử nghiệm trực giao để tối ưu hóa các loại nguyên liệu thô được sử dụng. Bước này rất quan trọng để xác định các thành phần phù hợp nhất cho công thức kết dính.
Tỷ lệ tinh chỉnh
Sau đó, họ sử dụng thiết kế thử nghiệm tùy chỉnh của JMP để tối ưu hóa tỷ lệ nguyên liệu thô đã chọn. Phương pháp này thực sự tránh được thách thức chung là giải quyết đồng thời cả loại nguyên liệu và tỷ lệ trong quá trình phát triển công thức thông thường.
Kết quả nghiên cứu của họ chứng minh rằng phương pháp cải tiến này đã giải quyết thành công các yêu cầu xung đột về độ cứng thấp và cường độ liên kết cao trong chất kết dính. Họ đã tạo ra một chất kết dính polyurethane có đặc điểm:
- Độ cứng keo: 40 ngày
- Độ bền kéo cắt: 11,34 MPa (tấm nhôm với tấm nhôm)
- Sức mạnh liên kết: 283,5 kPa/D trên một đơn vị độ cứng
Thí nghiệm phát triển đã hoàn tất chưa? Chưa hẳn. Các tác giả lưu ý rằng vẫn còn một số "vấn đề", làm nổi bật những khó khăn đang diễn ra trong quá trình phát triển công thức kết dính. Những thách thức này thường là nơi có thể nảy sinh những cải tiến đáng kể.
Tầm quan trọng của việc đánh giá các giả định không chính xác sau đây
Tương tác giữa các danh mục chính:Quá trình tối ưu hóa không tính đến sự tương tác giữa các loại nguyên liệu thô khác nhau, điều này có thể ảnh hưởng đáng kể đến phản ứng thử nghiệm.
Tính chất vật lý của nguyên liệu thô:Các yếu tố như độ tinh khiết, độ ẩm và tính đồng nhất của nguyên liệu thô đã bị bỏ qua trong quá trình phân tích, có khả năng làm sai lệch kết quả.
Độc lập của Hiệu ứng Nguyên liệu:Giả định rằng loại và tỷ lệ nguyên liệu thô ảnh hưởng độc lập đến phản ứng thử nghiệm là sai lầm vì các yếu tố này thường ảnh hưởng lẫn nhau.
Với những bất ổn này trong quá trình xây dựng, điều quan trọng là phải tìm cách giảm thiểu tác động của chúng. Một chiến lược hiệu quả là sử dụng các yếu tố có thể kiểm soát được tương đối để bù đắp những bất ổn này.
Tận dụng chất độn trong chất kết dính
(1) Lựa chọn chất độn chính thống
Việc lựa chọn chất độn được sử dụng rộng rãi—như canxi cacbonat và silica—có thể tăng cường hiệu suất của chất kết dính. Chất độn khoáng không chỉ cung cấp giải pháp tiết kiệm chi phí mà còn cung cấp nhiều chức năng đa dạng. Chúng đã là thành phần chính trong công thức chất kết dính trong nhiều năm, cho phép tinh chỉnh các đặc tính. Tang Long và cộng sự đã nhấn mạnh rằng trong nghiên cứu của họ, phạm vi của nhựa nền và chất kéo dài chuỗi/chất liên kết ngang có tác động lớn nhất đến kết quả thử nghiệm. Chất phụ gia lưu biến có ảnh hưởng thứ cấp, trong khi chất độn có tác động đáng kể, nằm giữa các tác động chính và thứ cấp.
Khi lựa chọn chất độn, có sự linh hoạt đáng kể và chất độn truyền thống thường là lựa chọn tốt nhất. Việc sử dụng lâu dài trong sản xuất mang lại cho chúng hiệu quả về chi phí và độ ổn định cao hơn. Ví dụ, canxi cacbonat - được biết đến với độ mịn, độ đồng đều và độ trắng cao - đã được sử dụng rộng rãi làm chất độn trong chất kết dính.
Cui Lidong và cộng sự đã tiến hành nghiên cứu sử dụng canxi cacbonat 850 lưới làm chất độn trong keo dán nhũ tương cho gỗ. Họ đã nghiên cứu tác động của các tỷ lệ bổ sung khác nhau đến hiệu suất keo dán thông qua phương pháp thử nghiệm một yếu tố. Kết quả chỉ ra rằng:
- Độ nhớt và độ cứng: Tăng theo tỷ lệ canxi cacbonat cao hơn.
- Sức mạnh liên kết: Ban đầu tăng, sau đó giảm ở tỷ lệ cao hơn.
- Sự ổn định: Bị hư hỏng khi hàm lượng chất độn tăng cao.
Tác động của chất độn lên hiệu suất keo dán
Mối quan hệ giữa tỷ lệ bổ sung canxi cacbonat và độ cứng Shore A
Zhou Xiao và cộng sự đã nghiên cứu ảnh hưởng của bột thạch anh như một chất độn trong keo dán polyurethane một thành phần. Phát hiện của họ chỉ ra rằng bột thạch anh thể hiện khả năng tương thích tốt với hệ thống polyurethane, tăng cường đáng kể các đặc tính như độ bền kéo, độ giãn dài khi đứt và độ bền xé của các sản phẩm keo dán thu được.
(2) Khám phá chất độn tiên tiến: Silicon Carbide và Alumina
Li Zhaoyuan và cộng sự đã sử dụng nano-silicon carbide khối (β-SiC) làm chất độn để phát triển chất kết dính vô cơ đã được biến đổi. Các thí nghiệm của họ cho thấy rằng với hàm lượng chất độn là 40%, chất kết dính đạt được các chỉ số hiệu suất đáng chú ý:
- Độ bền kéo cắt: 13,5MPa
- Số lần lặp lại tuổi thọ mệt mỏi: 67 chu kỳ
- Sức mạnh bóc vỏ: 46,7 N/mm²
Những kết quả này nhấn mạnh rằng việc biến đổi hạt nano có thể cải thiện đáng kể hiệu suất liên kết của chất kết dính vô cơ, mang lại độ tin cậy vượt trội trong nhiều ứng dụng khác nhau.
Chen Zeming và cộng sự đã khám phá tác động của nhiều chất độn vô cơ khác nhau—bao gồm bột silica, Al₂O₃, mullite, boron nitride, bột talc và mica—trên chất kết dính nhựa epoxy biến tính. Nghiên cứu của họ đánh giá cách các loại và liều lượng chất độn khác nhau ảnh hưởng đến cường độ liên kết và giao diện liên kết. Những phát hiện chính bao gồm:
Xu hướng sức mạnh liên kết:Độ bền liên kết ban đầu tăng theo liều lượng chất độn, sau đó giảm ở mức cao hơn.
Hiệu suất Filler tối ưu:Trong số các chất độn được thử nghiệm, 15 phần Al₂O₃ mang lại kết quả tốt nhất, đạt giá trị cường độ cắt và cường độ bóc lần lượt là 22,42 MPa và 12,84 N/cm.
Việc bổ sung chất độn Al₂O₃ tạo điều kiện cho sự hình thành các liên kết hóa học, chẳng hạn như C-Al và Al-OC, làm giảm lực kết dính của nhựa epoxy biến tính. Sự cải tiến này làm tăng lực liên kết tại giao diện hợp kim nhôm-chất kết dính, do đó cải thiện cả độ bền bóc và độ bền cắt.
(3) Nghiên cứu có hệ thống về chất độn trong chất kết dính
Keo dán kết cấu acrylic hai thành phần được sử dụng rộng rãi để liên kết các vật liệu kim loại và phi kim loại trong nhiều ngành công nghiệp khác nhau, bao gồm hàng không vũ trụ, ô tô, xây dựng và điện tử. Mặc dù chất độn không hòa tan trong hệ thống keo dán do các đặc tính vốn có của chúng, nhưng việc sửa đổi có thể tăng cường sự tương tác giữa chất độn và chất kết dính. Sự tương tác này cải thiện các đặc tính cơ học của chất kết dính, tăng độ nhớt và thúc đẩy độ bám dính mạnh hơn vào chất nền.
Quy định về tính chất cơ học
Tính chất cơ học rất quan trọng đối với hiệu suất của cấu trúc acrylic chất kết dính trên nhiều ứng dụng khác nhau. Các nhà nghiên cứu đã đề xuất một số chiến lược để tăng cường các đặc tính này, bao gồm việc kết hợp các hợp chất nhiệt dẻo và chất độn vô cơ.
Điều chỉnh độ dẫn nhiệt
Việc kết hợp các chất độn vô cơ thích hợp với các đặc tính cách điện có thể cải thiện đáng kể độ dẫn nhiệt của hệ thống keo dán acrylic. Các chất độn thích hợp bao gồm:
- Nhôm hydroxit
- Magiê Hydroxit
- Nhôm oxit
- Magie oxit
- kẽm oxit
- Silic Dioxit
- Titan Dioxide
- Canxi Silicat
- Nhôm Silicat
- Canxi cacbonat
- Nitrua silic
- Cacbua silic
- Nhôm Borat
Ngoài ra, các sợi ria làm từ silicon carbide, nhôm oxit hoặc nhôm borat có thể cải thiện khả năng dẫn nhiệt và chống cháy của chất kết dính trong khi vẫn duy trì các đặc tính cơ học và đóng rắn của nó.
Điều chỉnh độ ẩm và khả năng chịu nhiệt
Liu Chengliang và cộng sự đã giới thiệu một phương pháp để chế tạo keo dán kết cấu acrylic có khả năng chống chịu thời tiết cao trong bằng sáng chế của họ. Bằng cách thêm 0 đến 30 phần chất độn vô cơ, chẳng hạn như silica khói, canxi cacbonat và nano-alumina, vào các thành phần A và B, keo dán đã chứng minh hiệu suất ấn tượng:
- Độ bền kéo cắt ở nhiệt độ phòng: 9,36 MPa (thép không gỉ/PMMA) và 10,35 MPa (magiê/PMMA).
- Độ bền kéo cắt sau khi lão hóa: Giá trị được giữ lại là 9,83 MPa và 9,64 MPa sau 2 tuần ở nhiệt độ 85°C và độ ẩm 85%, với tỷ lệ giữ lại lần lượt là 105% và 93%.
Quy định về khả năng chống ăn mòn
Sử dụng keo dán kết cấu acrylic có thể làm giảm hoặc loại bỏ nhu cầu về các hoạt động hoàn thiện tốn kém như tán đinh và hàn, mang lại vẻ ngoài thẩm mỹ hơn với ít lỗ hoặc điểm chịu ứng suất dễ bị ăn mòn hơn. Các kim loại khác nhau có thể được liên kết với nguy cơ ăn mòn điện hóa thấp hơn. Có thể tăng cường khả năng chống ăn mòn bằng cách thêm hỗn hợp molybdate kim loại (ví dụ, molybdate kẽm, molybdate canxi, molybdate bari hoặc molybdate stronti) và chất độn trơ như kẽm phosphat, canxi phosphat và magiê phosphat.
Quy định về các tài sản khác
Ngoài việc tăng cường các đặc tính cơ học và nhiệt, một số chất độn vô cơ còn đóng vai trò quan trọng như chất làm tăng độ nhớt, chất làm đặc và chất gia cường. Chúng có thể thay đổi hiệu quả nhiều đặc điểm khác nhau của hệ thống keo dán kết cấu acrylic hai thành phần, bao gồm mật độ, độ nhớt và độ nhớt. Liu Suyu và cộng sự đã phát triển một phương pháp tạo ra keo dán acrylic được thiết kế riêng để dán các tấm ốp chân tường ô tô. Trong công thức này, canxi cacbonat được sử dụng làm chất độn chính. Việc đưa canxi cacbonat vào đã mang lại một số kết quả có lợi:
- Giảm Thixotropy:Chất kết dính dễ bôi và cạo hơn.
- Nhiệt độ tỏa nhiệt thấp hơn:Nhiệt độ tỏa nhiệt được giảm từ 115°C xuống dưới 85°C, thúc đẩy quá trình đóng rắn ổn định hơn.
- Giảm thiểu co ngót khi đóng rắn:Độ co ngót khi đông cứng được giữ dưới 1%, giúp rút ngắn thời gian thi công một cách hiệu quả.
Phần kết luận
Khi đối mặt với những thách thức trong công thức keo dán, hãy cân nhắc sử dụng chất độn vô cơ. Tính linh hoạt của chúng có thể cung cấp giải pháp hiệu quả cho nhiều vấn đề khác nhau.